中小製造業の現場で働く我々の多くは、日々時間に追われています。人員はギリギリ、設備も昔ながらで決して新しくない。それでも顧客の要求に応えようと、現場は常にフル稼働。それなのにいつもなぜか残業が必要となる。従業員のモチベーションも上がらないし、いまいち職場も盛り上がってない。
「一体なぜこんなに時間がかかるんだ?もっと効率的に仕事を進める方法はないのか?」
リーダーの多くは頭を抱えています。しかし、問題の根本原因は、日常業務の中に溶け込んでしまい、見つけることができません。まるで透明人間のように、ムダな作業や非効率なプロセスが、あなたの現場に潜んでいるのです。
「この見えないムダを見つけ出し、生産性を劇的に向上させる方法はないのか?」
そんな悩みを抱える職場には効果抜群です。
トヨタ自動車が世界に誇る「トヨタ生産方式」を支える「IE手法(インダストリアル・エンジニアリング手法)」をご存知でしょうか?
IE手法は、現場の隠れたムダを見えるようにし、ムダのない生産性の高い職場を実現するための手法です。まるで透明人間を見つける特殊なメガネのように、問題点を浮き彫りにし、具体的な改善策を導き出すことができます。トヨタのみならず、多くの企業がIE手法を導入し、目覚ましい成果を上げているんです。
「でも、IE手法って難しそう…。大企業がやることでしょ?」
そう思っていませんか?
実は、IE手法は中小製造業の現場でも、意外と難しくなく、そして効果的に導入できるのです。
そこで今回は現場を良くしたいと願うあなたに向けて、IE手法の基礎から実践的な活用方法まで、完全ガイドとしてシンプルな解説を進めていきます。
- IE手法とは何か?
- なぜIE手法が重要なのか?
- トヨタはどのようにIE手法を活用しているのか?
- IE手法の7つ道具とは?: 隠れたムダを見える化する 7つのツール
- 具体的にどのようにIE手法を導入すればいいのか?
こういった疑問に答えながら、あなたの現場に潜む「見えないムダ」を「見える化」し、ムダのない生産性の高い職場を実現するための具体的なヒントを提供したいと思います。
それでは今回も読み終えるまでのお時間、しばらくお付きくださいませ。
IE手法とは:定義と重要性
それではそのIE手法とはどんなものか?定義とその重要性について詳しく説明を進めてまいります。
IE(インダストリアル・エンジニアリング=科学的管理法)手法の基本概念
IE手法とは、「人間の作業、物の流れ、設備の配置など、生産活動に関わるあらゆる要素を分析し、改善することで、生産性を向上させる手法」です。
まるで職場のレントゲン写真のように、普段は見えないムダな動きや非効率なプロセスを可視化し、具体的な改善策を導き出すことができます。
IE手法は、以下の3つの要素を柱としています。
- 人間:作業者の動作、作業環境、安全性などを分析し、より効率的で安全な作業方法を追求します。
- 物:製品や材料の流れ、在庫状況などを分析し、ムダな移動や保管を削減します。
- 設備:機械の稼働状況、配置などを分析し、設備の効率的な活用を図ります。
ビジネスにおけるIE手法の重要性
現代のビジネス環境は、グローバル競争の激化、顧客ニーズの多様化、技術革新の加速など、変化の激しい時代となっています。このような環境下で生き残るためには、常に生産性を向上させ、コストを削減していくことが不可欠です。
IE手法は、まさにこの課題を解決するための強力なツールとなります。IE手法を導入することで、
- 生産性の向上:ムダを排除し、作業効率を向上させることで、より多くの製品を、より短い時間で生産できるようになります。
- コスト削減:材料費、人件費、設備費などのコストを削減し、利益率を向上させることができます。
- 品質向上:作業の標準化や品質管理の強化により、製品の品質を向上させることができます。
- 納期短縮:生産リードタイムを短縮し、顧客満足度を高めることができます。
- 従業員満足度の向上:安全で働きやすい職場環境を実現し、従業員のモチベーションを高めることができます。
これらの効果により、企業は競争力を強化し、持続的な成長を遂げることができるのです。
IE手法の歴史と発展
IE手法は、20世紀初頭にアメリカの機械技術者であるフレデリック・テイラーによって提唱された「科学的管理法」を起源としています。その後、第二次世界大戦を経て、生産管理技術として発展を遂げ、現代のIE手法へと進化してきました。
日本では、戦後、トヨタ自動車がIE手法を積極的に導入し、「トヨタ生産方式」として世界にその名を轟かせました。トヨタの成功は、他の日本企業にもIE手法導入の波を起こし、現在では多くの企業がIE手法を活用しています。
近年では、AIやIoTなどの最新技術とIE手法が融合し、さらなる進化を遂げています。これらの技術を活用することで、より高度なデータ分析が可能となり、より効果的な改善策を導き出すことができるようになっています。
IE手法は、時代とともに進化を続け、常に「生産性向上」という企業の根源的な課題解決に貢献してきました。そして、これからも、企業の成長を支える重要な役割を果たしていくことでしょう。
トヨタ生産方式におけるIE手法の活用
実はこのIE手法は、日本で唯一世界の企業資産ランキングに入っているトヨタ自動車をつくりあげた考え方がベースとなっています。そのためトヨタ生産方式とはきってもきれない関係があります。
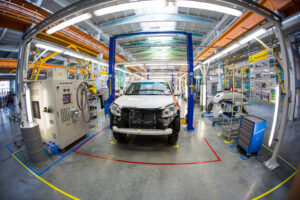
トヨタのIE手法導入背景
トヨタ自動車は、戦後の資源不足や厳しい経済状況の中、大量生産方式を採用するアメリカの自動車メーカーに対抗するため、独自の生産方式を模索していました。その中で、「必要なものを、必要な時に、必要なだけ作る」というジャストインタイム生産の概念を確立し、それを実現するためのツールとしてIE手法を積極的に導入していったのです。
工程分析:ジャストインタイム生産の基盤
トヨタは、IE手法の一つである工程分析を活用し、生産ライン全体の流れをスムーズにすることに注力しました。各工程の作業時間や作業内容を詳細に分析し、ボトルネックとなっている工程を特定、改善することで、滞りなく製品が流れる生産ラインを実現したわけです。これにより、過剰な在庫や待ち時間を削減し、ジャストインタイム生産を可能にしました。

動作分析:ムダの排除と標準作業の確立
さらにトヨタは、動作分析を通じて、作業者の一つ一つの動作を細かく観察し、ムダな動きを徹底的に排除しました。そして、最も効率的な作業方法を標準作業として定め、作業者全員が同じ方法で作業を行うようにしたのです。これにより、作業のばらつきがなくなり、品質の安定化と高い生産性向上を実現した、というわけです。すごいですよね!これは真似したいです。
トヨタ式IE手法の成功要因
トヨタのIE手法導入の成功は、以下の要因によると考えられます。
- トップダウンとボトムアップの融合:経営層がIE手法の重要性を理解し、積極的に導入を推進すると同時に、現場の作業者も改善活動に主体的に参加することで、全社的な取り組みとなりました。
- 継続的な改善:一度改善したら終わりではなく、常に問題意識を持ち、改善を続ける文化を醸成しました。「カイゼン」という言葉は、まさにトヨタのこの姿勢を表しています。
- 人材育成:IE手法を理解し、実践できる人材を育成することに力を入れました。これにより、現場の改善能力を高め、持続的な改善を可能にしました。
トヨタの成功は、IE手法が単なるツールではなく、企業文化の一部として根付いた結果と言えるでしょう。
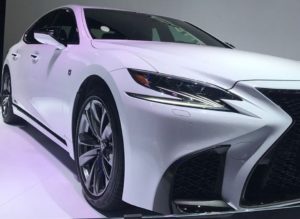
IE手法の実践事例:業界別分析
では具体的にどんな業界でどのような成果を上げているのでしょうか。業界別に実際の事例を紹介しながら分析していきましょう。
金属切削業におけるIE手法の適用
金属切削加工は、高い精度と品質が求められる一方で、加工時間や段取り替え時間が長く、生産性の向上が課題となることが多い業界です。
IE手法を導入することで、
- 加工時間短縮:工具や加工条件の最適化、段取り替え時間の短縮などにより、加工時間を大幅に短縮することができます。
- 品質向上:加工条件の標準化や検査工程の効率化により、製品の品質を安定化させることができます。
- 作業環境改善:作業者の動作分析や作業環境の改善により、安全で働きやすい職場環境を実現することができます。
例えば、ある金属切削加工会社では、IE手法を導入し、段取り替え時間を約50%削減、加工時間を約30%短縮することに成功しました。
プラスチック樹脂成型業でのIE手法活用事例
プラスチック樹脂成型業は、多品種少量生産が特徴であり、金型交換や材料変更に伴う段取り替え時間が生産性に大きく影響します。
IE手法を活用することで、
- 段取り替え時間短縮:金型交換作業の標準化や、金型設計の工夫などにより、段取り替え時間を大幅に短縮することができます。
- 不良品削減:成形条件の最適化や品質管理の強化により、不良品発生率を低減することができます。
- 生産計画最適化:生産計画のシミュレーションや、生産進捗の見える化などにより、生産計画の精度を高めることができます。
あるプラスチック樹脂成型会社では、IE手法を導入し、段取り替え時間を約70%削減、不良品発生率を約50%低減することに成功しました。
食品製造業界でのIE手法導入効果
食品製造業界は、衛生管理や品質管理が厳しく、作業の標準化や効率化が求められる業界です。
IE手法を導入することで、
- 作業標準化:作業手順の明確化や、作業時間の標準化などにより、作業のばらつきをなくし、品質の安定化を図ることができます。
- 衛生管理強化:作業環境の改善や、衛生管理手順の見直しなどにより、衛生管理レベルを高めることができます。
- レイアウト最適化:作業動線の改善や、設備配置の見直しなどにより、作業効率を向上させることができます。
ある食品製造会社では、IE手法を導入し、作業時間を20%短縮、不良品発生率を約30%低減することに成功しました。
IE手法の7つ道具:詳細解説
そしてIE手法には代表的な問題の見える化ツールが7つあり「IE手法の7つ道具」が存在しています。今回はその7つについて解説を進めてまいります。
時間研究(タイムスタディ):作業時間の測定と改善
時間研究とは、ストップウォッチやビデオカメラなどを使い、作業時間を細かく測定・分析する手法です。まるで職人の技をスローモーションで見るように、作業の各動作にかかる時間を明らかにし、ムダな動きや遅れの原因を特定することができます。
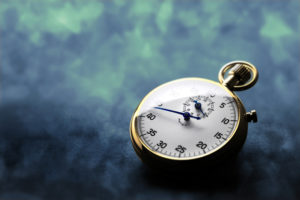
時間研究で何がわかる?
- 仕事量の定量的な把握:作業手順を標準化し、所要時間を数値化することで、改善の優先順位を客観的に判断できます。
- 事実の見落とし防止:作業構成を見える化することで、改善ポイントの見落としを防ぎ、具体的な対策を検討できます。
- ムダ作業の抽出と改善:要素作業レベルでムダを特定し、標準時間との比較から改善案を導き出せます。
時間研究の進め方
- 対象作業の区分:改善効果が大きく、標準化しやすい作業を選びます。
- 作業の細分化:作業を細かい動作要素に分解します。
- 時間測定:ストップウォッチやビデオカメラを使い、各動作要素にかかる時間を複数回測定します。
- 測定値の整理と分析:測定値を統計的に処理し、標準時間や余裕率などを算出します。
- 改善案の立案と実施:ムダな動作を排除し、作業手順やレイアウト、工具などを改善します。
- 効果の確認:改善後の作業時間を測定し、効果を確認します。
時間研究の活用事例:製造業
- 金属切削業:製品の加工時間や段取り替え時間を測定し、ボトルネック工程を特定、改善することで生産効率を向上させました。
- 製缶業:溶接作業の各動作時間を測定し、ムダな動きを削減、作業手順を改善することで、作業時間短縮と品質向上を実現しました。
- 食品製造業:包装作業の各工程の時間を測定し、作業バランスを見直すことで、ライン全体の生産性を向上させました。
- 金型製造業:金型の組み立て作業の各動作時間を測定し、工具の配置や作業手順を改善することで、作業効率と品質を向上させました。
時間研究は、一見単純な作業に見えても、実は多くのムダが潜んでいることを明らかにします。ストップウォッチを片手に、あなたの現場の「見えないムダ」を「見える化」し、生産性向上への第一歩を踏み出しましょう。
稼働分析:設備・人員の効率化
稼働分析とは、設備や人員の稼働状況を時間比率で把握し、問題点を見つけ出す手法です。まるで工場のレントゲン写真のように、設備や人員がどのくらい働いているのか、どのくらい休んでいるのかを明らかにし、効率化の余地を見つけることができます。
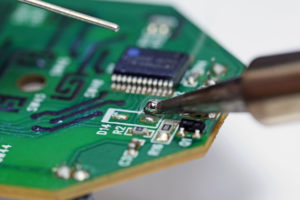
稼働分析で何がわかる?
- 生産性の向上余地:設備や人員の稼働率を把握することで、全体の生産性がどの程度向上できるか、おおまかに把握できます。
- 各作業・状態の時間値:それぞれの作業や状態にどれだけの時間が費やされているかを把握できます。
- ロスの定量化と改善対象の絞り込み:稼働していない時間やムダな作業を数値化することで、改善すべきポイントを明確にできます。
稼働分析の種類
稼働分析には、主に3つの種類があります。
- 連続観測法:対象を連続的に観察し、稼働時間と非稼働時間の比率を算出します。
- ワークサンプリング法:ランダムなタイミングで瞬間的に観察を行い、その結果を集計して稼働率を推定します。
- その他の方法:日報の集計や計測器の活用など、状況に応じて適切な方法を選択します。
稼働分析の進め方
- 分析対象の選定:改善効果が大きく、測定しやすい設備や人員を選びます。
- 状態の定義:稼働と非稼働の状態を明確に定義します。
- 測定方法の決定:連続観測法、ワークサンプリング法など、状況に応じて適切な測定方法を選択します。
- 測定の実施:測定方法に従って、設備や人員の稼働状況を測定します。
- 測定値の整理と分析:測定値を集計し、稼働率やムダな時間を算出します。
- 改善案の立案と実施:分析結果をもとに、ムダな時間を削減するための具体的な対策を検討し、実施します。
- 効果の確認:改善後の稼働率を測定し、効果を確認します。
稼働分析の活用事例:製造業
- 金属加工業:機械の段取り替え時間や待ち時間を削減し、稼働率を向上させました。
- 製缶業:溶接作業の段取りを見直し、作業者の手待ち時間を削減することで、人員の稼働率を向上させました。
- 食品製造業:製造ラインのボトルネックを解消し、設備の稼働率を向上させました。
- 金型製造業:作業手順の標準化と改善により、作業者のムダな動きを削減し、稼働率を向上させました。
工程分析:生産ラインの最適化
工程分析とは、製品やモノの流れに着目し、生産プロセス全体を分析する手法です。まるで工場のレントゲン写真のように、製品がどのように流れているのか、どこで滞っているのかを明らかにし、効率化の余地を見つけることができます。
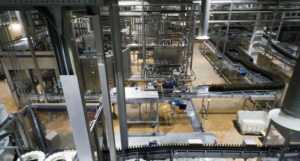
工程分析で何がわかる?
- 工程系列の概要把握:生産プロセス全体の流れを可視化し、各工程の役割や相互関係を把握できます。
- ムダな工程の特定:生産ライン全体の流れを分析し、ムダな工程や非効率な手順を特定することができます。
- ボトルネックの特定:生産ラインの中で、特に滞りやすい箇所(ボトルネック)を特定することができます。
- 生産ラインの最適化:ムダな工程を排除し、ボトルネックを解消することで、生産ライン全体を最適化することができます。
工程分析の種類と目的
工程分析には4つの種類があり、それぞれ分析対象や目的が異なります。
- フロープロセスチャート(加工工程分析):1つの製品の加工工程を分析し、ムダな工程や非効率な手順を特定します。
- アッセンブリーチャート(組立工程分析):複数の部品を組み立てる工程を分析し、ムダな工程や非効率な手順を特定します。
- 経路分析(類似工程分析):複数の製品の工程を比較分析し、工程間の負荷バランスや運搬量などを把握します。
- フローダイヤグラム(流れ分析):工程系列が異なる複数の製品の生産ラインを分析し、工程間の相互関係や物流の流れを把握します。
工程分析の進め方
- 対象製品・工程の選定:改善効果が大きく、測定しやすい製品や工程を選びます。
- 工程の分類:各工程を「加工工程」「運搬工程」「検査工程」「停滞工程」の4種類に分類します。
- 工程図の作成:各工程の順序や内容、時間などを図式化します。
- ムダの特定と分析:工程図をもとに、ムダな工程や非効率な手順、ボトルネックなどを特定し、その原因を分析します。
- 改善案の立案と実施:ムダを排除し、ボトルネックを解消するための具体的な対策を検討し、実施します。
- 効果の確認:改善後の工程を分析し、効果を確認します。
工程分析の活用事例:製造業
- 金属加工業:加工工程を分析し、段取り替え時間や加工時間を短縮することで、生産性を向上させました。
- 製缶業:溶接工程を分析し、作業手順や設備配置を見直すことで、作業効率と品質を向上させました。
- 食品製造業:包装工程を分析し、ムダな動きを削減し、作業手順を標準化することで、作業効率と衛生管理レベルを向上させました。
- 金型製造業:金型の設計・製造工程を分析し、情報共有やコミュニケーションを改善することで、設計変更に伴う手戻りを削減しました。
作業分析(動作分析):タスクの最適化
作業分析(動作分析)とは、作業者の動作を細かく観察し、ムダな動きや非効率な手順を特定する手法です。まるで職人の技をスローモーションで見るように、作業者の動きを分解し、効率化の余地を見つけることができます。
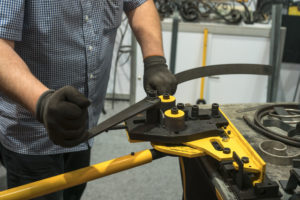
作業分析(動作分析)で何がわかる?
- ムダな動作の特定:作業者の動作を細かく観察し、ムダな動きや非効率な手順を特定することができます。
- 作業の標準化:最も効率的な作業方法を標準化し、作業者全員が同じ方法で作業を行うようにすることができます。
- 作業環境の改善:作業者の動作や作業環境を分析し、作業環境の改善を図ることができます。
作業分析の種類と選択
作業分析にはいくつかの分析手法があり、それを工程の特性や改善目的などにより活用手法を選択する必要があります。代表的な手法は以下の2つです。
- ライン作業分析:ライン編成が主である場合に活用し、ピッチダイアグラムなどを用いて目標サイクルタイムとのバランスを見て改善を検討します。
- 連合作業分析:設備と作業者、あるいは作業者同士の連携が主である場合に活用し、各作業主体のプロセスのタイミングをチャートに表すことで改善点を抽出します。
動作分析の種類と選択
動作分析は、取り扱う最も小さな単位の分析です。代表的な分析手法は以下の3つです。
- サーブリック分析:人の最小の動作を18の基本要素に区分し、手や目の動きを記号を使って表現することで、問題点を抽出し改善を進める方法です。
- フィルム分析:動画撮影を用いて、低速度撮影や高速度撮影などで作業を観察し、問題点を特定する方法です。
- PTS法(Predetermined Time Standard: 規程時間法):人間の作業に含まれる動作要素について予め定めておいた「標準時間」を組み合わせ、作業そのものの標準時間を設定する方法です。MTM法とWF法が代表的な手法として挙げられます。
作業分析(動作分析)の活用事例:製造業
- 金属加工業:機械加工における作業者の動作を分析し、ムダな動きを削減することで、加工時間を短縮し、生産性を向上させました。
- 製缶業:溶接作業における作業者の姿勢や工具の使い方を分析し、作業環境を改善することで、作業効率と品質を向上させました。
- 食品製造業:食品の包装作業における作業者の動作を分析し、ムダな動きを削減し、作業手順を標準化することで、作業効率と衛生管理レベルを向上させました。
- 金型製造業:金型の組み立て作業における作業者の動作を分析し、工具の配置や作業手順を見直すことで、作業効率と品質を向上させました。
レイアウト分析:作業空間の効率化
レイアウト分析とは、工場内における設備、作業場所、通路などの配置を分析し、ムダな移動や作業の滞りを解消する手法です。まるで工場の設計図を最適化するように、作業空間全体を見直し、効率的で働きやすい環境を作り出すことができます。
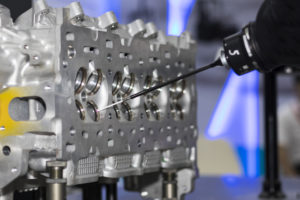
レイアウト分析で何がわかる?
- ムダな移動の特定:作業者の移動経路やモノの運搬経路を分析し、ムダな移動を特定できます。
- ボトルネックの特定:作業空間の中で、作業が滞りやすい場所(ボトルネック)を特定できます。
- 作業空間の最適化:ムダな移動を排除し、ボトルネックを解消することで、作業空間全体を最適化できます。
レイアウト分析の進め方:SLP(Systematic Layout Planning)
レイアウト分析を行う際には、SLP(Systematic Layout Planning)と呼ばれる体系的な手法を活用することが一般的です。SLPは、以下の4つのステップで進めます。
- P-Q分析の実施:製品ごとの生産量や重要度を分析し、どの製品を優先的に配置するかを決定します。
- 相互関連分析図およびアクティビティ相互関連図の作成:各作業間の関連性や、作業場所間の移動頻度などを分析し、最適な配置を検討します。
- 面積相互関連図の作成:各作業に必要な面積を考慮し、作業場所の配置や広さを検討します。
- 改善案の検討:分析結果をもとに、複数のレイアウト案を作成し、生産性、安全性、コストなどの観点から評価を行い、最適な案を選定します。
レイアウト分析の活用事例:製造業
- 金属加工業:機械の配置を見直し、作業動線を短縮することで、加工時間を短縮し、生産性を向上させました。
- 製缶業:材料置き場を作業場所の近くに配置し、移動距離を短縮することで、作業効率を向上させました。
- 食品製造業:生産ラインのレイアウトを見直し、工程間の移動をスムーズにすることで、生産リードタイムを短縮しました。
- 金型製造業:設計部門と製造部門の距離を近づけ、コミュニケーションを円滑にすることで、設計変更に伴う手戻りを削減しました。
マテハン分析:工場内の「運ぶ」を効率化
マテハン分析とは、工場内におけるモノの移動(マテリアルハンドリング)を分析し、ムダな運搬や非効率な保管方法を特定する手法です。まるで工場の物流網をレントゲン写真のように可視化し、モノの流れをスムーズにすることで、生産性向上に繋げることができます。
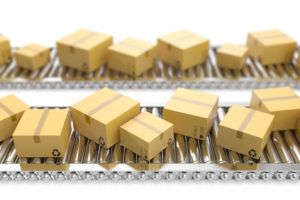
マテハン分析で何がわかる?
- ムダな運搬の特定:モノの移動経路や頻度を分析し、ムダな運搬や非効率な保管方法を特定できます。
- ボトルネックの特定:モノの流れの中で、滞りが発生しやすい箇所(ボトルネック)を特定できます。
- 物流の最適化:ムダな運搬を排除し、ボトルネックを解消することで、工場全体の物流を最適化できます。
マテハン分析の進め方
マテハン分析は、主に運搬工程分析と運搬活性化分析の2つの手法を用いて行います。
- 運搬工程分析:モノの流れを図式化し、各工程における運搬の状況(時間、距離、手段など)を記録・分析します。
- 運搬活性化分析:モノの運搬のしやすさ(活性度)を評価し、改善の余地を特定します。
これらの分析結果をもとに、以下の点を考慮しながら改善策を検討します。
- 運搬回数の削減:モノの移動距離を短縮したり、一度に運ぶ量を増やすことで、運搬回数を減らすことができます。
- 運搬距離の短縮:レイアウト変更や、保管場所の見直しなどにより、運搬距離を短縮することができます。
- 運搬方法の改善:適切な運搬機器の選定や、運搬経路の整備などにより、運搬効率を向上させることができます。
- 保管方法の改善:保管場所のレイアウト変更や、保管方法の見直しなどにより、保管効率を向上させることができます。
マテハン分析の活用事例:製造業
- 金属加工業:加工済み部品の運搬経路を見直し、工程間の移動距離を短縮することで、運搬時間を削減し、生産性を向上させました。
- 製缶業:材料の保管場所を加工場所の近くに配置し、移動距離を短縮することで、作業効率を向上させました。
- 食品製造業:製品の保管方法を見直し、パレット化やラック導入により、保管スペースを削減し、作業効率を向上させました。
- 金型製造業:金型の運搬に専用台車を導入し、運搬の安全性と効率性を向上させました。
事務工程分析:事務業務のタスクの最適化
事務工程分析とは、事務作業の流れや内容を分析し、ムダな作業や非効率な手順を特定する手法です。まるで事務作業のレントゲン写真のように、業務プロセスを可視化し、改善ポイントを明確にすることができます。
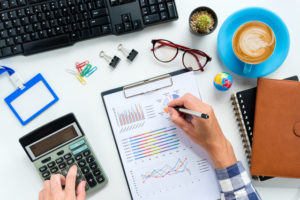
事務工程分析で何がわかる?
- ムダな作業の特定:事務作業の流れを分析することで、ムダな作業や非効率な手順を特定できます。
- ボトルネックの特定:事務プロセスの中で、特に滞りが発生しやすい箇所(ボトルネック)を特定できます。
- 事務プロセスの最適化:ムダな作業を排除し、ボトルネックを解消することで、事務プロセス全体を最適化できます。
事務工程分析の進め方
事務工程分析は、主に日報分析と業務山積表の作成を通じて行います。
- 日報分析:各作業者が、日々の業務内容や所要時間、問題点などを日報に記録します。これにより、個々の作業の実態や問題意識を把握できます。
- 業務山積表の作成:日報の内容を集計し、業務ごとの作業時間や発生頻度などを一覧表にまとめます。これにより、重点的に改善すべき業務を特定できます。
これらの分析結果をもとに、以下の点を考慮しながら改善策を検討します。
- 作業の標準化:業務プロセスを標準化し、作業のばらつきをなくすことで、効率化と品質向上を図ります。
- ITツールの活用:定型的な作業を自動化したり、情報共有をスムーズにするためのITツールを導入することで、作業効率を向上させます。
- レイアウトの改善:書類や備品の配置を見直すことで、作業動線を短縮し、ムダな動きを減らします。
- コミュニケーションの改善:業務の引継ぎや情報共有の方法を見直すことで、ミスや手戻りを減らします。
事務工程分析の活用事例:製造業
- 受発注業務の効率化:FAXやメールでの受注処理をシステム化し、入力ミスや処理時間の短縮を実現。
- 在庫管理業務の改善:在庫管理システムを導入し、リアルタイムな在庫状況の把握と発注業務の効率化を実現。
- 生産管理業務の最適化:生産計画や進捗管理をシステム化し、情報共有の迅速化と生産効率の向上を実現。
- 請求書発行業務の自動化:請求書発行システムを導入し、請求書作成の手間とミスを削減。
IE手法の実践ステップ:導入から改善まで
ではこれらのIE手法はどのような実践すればよいのでしょうか?それぞれわかりやすいよう5つのステップで解説をしたいと思います。
ステップ1:現状分析:問題点の特定
まずなんと言ってもIE手法導入の第一歩は、現状分析です。現状を正しく把握することで、具体的な問題点や改善ポイントが見えてきます。
現状分析の進め方
- 全体像の把握:生産プロセス全体の流れ、人員配置、設備の稼働状況などを確認し、全体像を把握します。
- 例えば、工場内を歩き回り、製品がどのように作られているのか、作業者がどのように動いているのかを観察してみましょう。
- 問題点の洗い出し:現場の観察、従業員へのヒアリング、データ分析などを通じて、具体的な問題点を洗い出します。
- 例えば、「あの機械の前でいつも作業者が待っているな」「この作業、もっと簡単にできそうなのに」といった気づきをメモしておきましょう。
- 問題の分類と優先順位付け:洗い出した問題点を重要度や緊急度などで分類し、優先順位をつけます。
- 例えば、「安全に関わる問題は最優先で対応しよう」「まずは、作業時間が長い工程から改善に取り組もう」といった具合に、優先順位を決めましょう。
- 原因分析:優先順位の高い問題について、その原因を深く掘り下げて分析します。
- 例えば、「なぜあの機械の前で作業者が待ってしまうのか?」「この作業が複雑なのは、なぜだろう?」といった疑問を解決するために、現場を観察したり、作業者に話を聞いてみましょう。
- 改善目標の設定:分析結果を踏まえ、具体的な改善目標を設定します。
- 例えば、「機械の段取り替え時間を30分短縮する」「製品の不良率を5%減らす」など、数値で目標を設定することで、改善の効果を測定しやすくなります。
ステップ2:改善目標の設定とKPI
現状分析によって問題点が明らかになったら、次は具体的な改善目標を設定します。目標を設定することで、改善活動の方向性を明確にし、効果測定の基準を設けることができます。
改善目標の設定方法
- 具体的な数値目標を設定する:現状の問題点を数値化し、改善後の目標値を具体的に設定します。例えば、「段取り替え時間を30%削減する」「不良品発生率を50%低減する」などです。
- 達成可能な目標を設定する:目標は、現状の能力や資源を考慮し、達成可能な範囲で設定します。高すぎる目標は、従業員のモチベーション低下につながる可能性があります。
- 期限を設定する:目標達成のための期限を明確に設定します。期限を設定することで、改善活動の進捗管理がしやすくなります。
KPI(重要業績評価指標)の設定
改善目標を達成するために、具体的なKPIを設定します。KPIは、改善活動の進捗状況や効果を測定するための指標です。KPIを設定することで、改善活動の効果を客観的に評価し、改善活動の軌道修正を行うことができます。
KPI設定のポイント
- 目標達成に直結する指標を選ぶ:改善目標に直接関係する指標を選びます。例えば、段取り替え時間の削減が目標であれば、段取り替え時間そのものをKPIとするのが適切です。
- 測定可能な指標を選ぶ:数値で測定できる指標を選びます。測定できない指標は、改善活動の評価に活用できません。
- 分かりやすい指標を選ぶ:現場の従業員にも理解しやすい指標を選びます。複雑な指標は、改善活動への参加意欲を低下させる可能性があります。
ステップ3:データ収集と分析手法
改善目標とKPIを設定したら、次はデータ収集を行います。データ収集は、現状を数値で把握し、改善の効果を測定するために不可欠なプロセスです。
データ収集方法
- 直接観察:ストップウォッチやカウンターなどを用いて、作業時間や発生頻度などを直接測定します。
- 記録の活用:作業日報や生産実績データなど、既存の記録を活用します。
- 従業員へのヒアリング:従業員に直接話を聞き、問題点や改善アイデアなどを収集します。
データ分析手法
収集したデータを分析し、問題点の原因や改善ポイントを特定します。分析手法としては、
- パレート図:問題の発生頻度や影響度を棒グラフで表し、重要な問題を特定します。
- 特性要因図:問題の原因と結果の関係を図で表し、根本原因を特定します。
- 散布図:2つの変数間の相関関係をグラフで表し、関係性を分析します。
- ヒストグラム:データの分布状況をグラフで表し、ばらつきや異常値を把握します。
などを活用します。
ステップ4:改善案の立案と実施プロセス
データ分析結果をもとに、具体的な改善案を立案します。改善案は、
- 実現可能性:現状の資源や能力で実現可能な案であるか
- 効果:目標達成に貢献できる効果が見込めるか
- 安全性:作業者の安全を確保できる案であるか
などを考慮して検討します。
改善案の実施プロセス
- 改善案の選定:複数の改善案を比較検討し、最適な案を選定します。
- 実施計画の作成:改善案の実施に必要な手順、担当者、スケジュールなどを明確にします。
- 従業員への説明と協力依頼:改善案の内容と目的を従業員に丁寧に説明し、協力を得ます。
- 改善案の実施:計画に従って、改善案を実施します。
- 進捗管理:定期的に進捗状況を確認し、必要に応じて計画を修正します。
ステップ5:効果測定とフィードバックループ
改善案を実施したら、効果測定を行います。KPIを用いて、改善前と改善後の状況を比較し、目標達成度を評価します。
効果測定のポイント
- 定量的な評価:KPIを用いて、数値で効果を測定します。
- 定性的な評価:従業員へのアンケートやヒアリングなどを通じて、改善による変化を把握します。
- 継続的な測定:改善の効果が持続しているか、定期的に測定します。
フィードバックループの構築
効果測定の結果を分析し、改善活動の成果と課題を明らかにします。そして、その結果を次の改善活動に活かすフィードバックループを構築することで、継続的な改善を実現します。
IE手法の実践ステップは、現状分析から始まり、改善目標の設定、データ収集と分析、改善案の立案と実施、効果測定とフィードバックループへと続きます。これらのステップを一つずつ着実に進めることで、あなたの現場は、ムダのない生産性の高い職場へと生まれ変わることでしょう。
IE手法の学習と資格取得
ではこれらIE手法 はどのようにして学べばよいのか、想像がつきませんよね。そこでIE手法の学習方法と、その学習の証となる資格取得について説明していきましょう。
IE手法に関する推奨書籍と学習リソース
IE手法を深く理解し、実践に活かすためには、体系的な学習が欠かせません。書籍やオンライン学習など、様々な学習リソースを活用して、知識とスキルを磨いていきましょう。
【書籍】
- 入門書
- IEの基礎(日本能率協会マネジメントセンター)
- 図解入門 よくわかる最新IEの基本と仕組み(秀和システム)
- トヨタ生産方式 徹底解剖 (日経文庫)(日本経済新聞出版)
- 実践書
- IEで会社を変える 実践のための7つのステップ(日刊工業新聞社)
- すぐできる! 現場改善 (現場の教科書)(日本能率協会マネジメントセンター)
- トヨタ式仕事術 (PHP文庫)(PHP研究所)
- 専門書
- インダストリアル・エンジニアリングハンドブック(丸善出版)
- 生産管理入門(日本経済新聞出版)
- ロジスティクス工学ハンドブック(朝倉書店)
【オンライン学習】
- Udemy:IE手法に関する様々な講座が提供されています。
- Coursera:海外の大学が提供するIE関連のコースを受講できます。
- YouTube:IE手法に関する解説動画や事例紹介動画が多数公開されています。
IE手法の研修プログラムと受講方法
体系的な知識と実践的なスキルを習得したい方には、研修プログラムへの参加がおすすめです。研修プログラムでは、専門家による講義やワークショップ、現場実習などを通じて、IE手法を深く学ぶことができます。
【研修プログラム例】
- 日本能率協会:IE基礎講座、IE実践講座、トヨタ生産方式講座など、様々なレベルの研修プログラムを提供しています。
- 企業内研修:自社内でIE手法の研修を実施することも可能です。外部コンサルタントを招いたり、社内のIE専門家が講師を務めることができます。
- オンライン研修:近年では、オンラインで受講できるIE研修も増えてきています。場所を選ばずに、自分のペースで学習を進めることができます。
IE関連の資格と検定試験
IE手法に関する知識やスキルを客観的に証明したい方には、資格取得に挑戦することもおすすめです。資格を取得することで、自身のスキルアップだけでなく、キャリアアップにもつながります。
【IE関連の資格】
- IE士(日本能率協会):IE手法に関する幅広い知識と実践能力を証明する資格です。
- 生産管理士(日本生産管理学会):生産管理に関する専門知識と実践能力を証明する資格です。
- 物流技術管理士(日本ロジスティクスシステム協会):物流技術に関する専門知識と実践能力を証明する資格です。
IE手法の学習と資格取得は、自己成長とキャリアアップのための貴重な投資です。積極的に学び、実践することで、あなたの市場価値を高め、企業の成長に貢献できる人材を目指しましょう。
IE手法と最新技術の融合
近年のIE手法は単独にとどまらずあらゆる最新技術との融合が進んでいます。その一部を紹介してみましょう。
デジタルツールを活用したIE手法
かつてはストップウォッチや紙とペンが中心だったIE手法も、現代では様々なデジタルツールを活用することで、より効率的かつ効果的な分析・改善が可能になっています。
- ビデオ解析ソフトウェア:高精度な動作分析や時間研究を実現。作業者の動きを細かく観察し、ムダな動作や改善ポイントを特定できます。
- シミュレーションソフトウェア:生産ラインやレイアウトの変更を仮想空間でシミュレートし、最適な配置や作業手順を検討できます。
- 工程管理システム:生産進捗や品質データなどをリアルタイムで収集・分析し、問題の早期発見や改善につなげます。
- タスク管理ツール:事務作業の進捗管理やタスクの割り当てを効率化し、業務の見える化を促進します。
AI・IoTとIE手法の相乗効果
AI(人工知能)やIoT(モノのインターネット)などの最新技術は、IE手法の進化を加速させています。
- AIによる画像認識:作業者の動作や設備の稼働状況を自動で認識し、データ収集や分析の効率化を図ります。
- IoTセンサーによるデータ収集:設備の稼働状況や環境データなどをリアルタイムで収集し、異常検知や予防保全に役立てます。
- AIによる予測分析:過去のデータから将来の需要や生産量などを予測し、生産計画の最適化や在庫管理の効率化に貢献します。
ビッグデータ分析によるIE手法の進化
IoTの発展により、膨大な量のデータが収集できるようになりました。これらのビッグデータを分析することで、従来は見逃されていたような隠れたムダや改善ポイントを発見することができます。
- 顧客データ分析:顧客の購買履歴や行動パターンを分析し、ニーズに合わせた製品開発やマーケティング戦略に活かします。
- 生産データ分析:生産実績や品質データなどを分析し、生産効率の向上や不良品発生率の低減につなげます。
- 設備データ分析:設備の稼働状況や故障履歴などを分析し、予防保全や設備投資の最適化に役立てます。
これらの最新技術とIE手法の融合は、生産性向上やコスト削減だけでなく、品質向上、顧客満足度向上、従業員満足度向上など、企業のあらゆる側面にプラスの影響を与えます。
IE手法の未来展望
そんな進化を果たし続けているIE手法ですが、その未来展望としてはどのように発展していくのでしょうか?将来的に果たすべき役割を大きな視点で見てみましょう。
グローバル化時代におけるIE手法の役割
グローバル化が加速する現代において、企業は世界中の競合との厳しい競争にさらされています。そのような中、IE手法は、企業が生き残るための重要な鍵となります。
- コスト競争力強化:グローバル市場では、低コストで高品質な製品を提供することが求められます。IE手法を活用し、生産性向上とコスト削減を継続的に進めることで、企業はコスト競争力を強化し、市場での優位性を確保できます。
- サプライチェーン最適化:グローバルサプライチェーンは、複雑かつ広範囲に及びます。IE手法を用いて、物流や在庫管理を最適化することで、リードタイム短縮や在庫削減を実現し、サプライチェーン全体の効率化を図ることができます。
- 品質管理の強化:グローバル市場では、高い品質基準が求められます。IE手法を活用し、作業標準化や品質管理体制を強化することで、製品の品質を向上させ、顧客満足度を高めることができます。
持続可能な生産とIE手法の関係性
環境問題への意識が高まる中、持続可能な生産活動が求められています。IE手法は、資源の効率的な利用や環境負荷の低減にも貢献します。
- 省エネルギー:設備の稼働状況を分析し、エネルギー消費量を削減するための改善策を立案・実施することで、省エネルギー化を推進できます。
- 廃棄物削減:生産プロセスを見直し、ムダな材料や不良品の発生を抑制することで、廃棄物削減に貢献できます。
- リサイクル促進:製品の設計段階からリサイクルを考慮したり、廃棄物の再資源化を促進することで、循環型社会の実現に貢献できます。
次世代IE技術者に求められるスキルセット
IE手法は、今後も進化し続け、企業の成長を支える重要な役割を果たしていくでしょう。そのため、次世代のIE技術者には、以下のスキルセットが求められます。
- 専門知識:IE手法に関する専門知識はもちろん、生産管理、品質管理、物流管理など、関連分野の知識も幅広く習得する必要があります。
- 問題解決能力:現場の課題を的確に捉え、分析し、解決策を導き出す能力が必要です。
- コミュニケーション能力:現場の作業者や経営層など、様々な立場の人と円滑にコミュニケーションを図り、協力を得る能力が必要です。
- データ分析能力:IoTやAIなどの最新技術を活用し、データを収集・分析し、改善に活かす能力が必要です。
- リーダーシップ:改善活動を推進し、チームをまとめるリーダーシップが必要です。
- 継続的な学習意欲:技術革新のスピードが速い現代において、常に新しい知識や技術を学び続ける姿勢が必要です。
IE技術者は、企業の生産性向上やコスト削減、持続可能な生産活動の実現など、企業の未来を左右する重要な役割を担っている、と言えそうです。
効果的なIE手法導入のポイント
これまでの説明でIE手法の素晴らしさを理解いただいたかと思いますが、実際に導入を図る時に注意すべきポイントがいくつかあります。それを説明しておきましょう。
成功のための重要ファクター
IE手法を導入するだけでは、現場の生産性向上は実現できません。成功には、以下の3つの重要ファクターが欠かせません。
- 経営層のコミットメント:IE手法導入は、現場だけの取り組みでは限界があります。経営層がその重要性を理解し、積極的に支援することが不可欠です。
- 現場の巻き込み:改善活動は、現場の作業者が主体的に取り組むことで、より大きな効果を生み出します。作業者の意見を尊重し、積極的に改善活動に参加してもらう環境を作りましょう。
- 継続的な改善:IE手法導入は、一度実施すれば終わりではありません。継続的に改善活動を続け、常に最適な状態を追求していくことが重要です。
よくある課題と解決策
IE手法導入には、いくつかの課題がつきものです。しかし、これらの課題を事前に把握し、適切な対策を講じることで、スムーズな導入と効果的な改善を実現できます。
- 課題1:従業員の抵抗
- 解決策:IE手法導入の目的やメリットを丁寧に説明し、従業員の理解と協力を得るように努めましょう。また、改善活動への参加を促し、主体的な取り組みを促しましょう。
- 課題2:データ収集・分析の負担
- 解決策:デジタルツールを活用し、データ収集・分析の効率化を図りましょう。また、外部コンサルタントの活用も有効です。
- 課題3:効果が見えにくい
- 解決策:改善目標とKPIを設定し、改善の効果を数値で「見える化」しましょう。小さな成功体験を積み重ねることで、従業員のモチベーション向上にもつながります。
継続的改善のためのアプローチ
IE手法導入はゴールではなく、スタートです。真の生産性向上を実現するためには、継続的な改善活動を続けなければなりません。
- PDCAサイクルの徹底:Plan(計画)→ Do(実行)→ Check(評価)→ Act(改善)のサイクルを回し、改善活動を継続的に行いましょう。
- 改善提案制度の導入:従業員からの改善提案を積極的に受け入れ、現場主導の改善活動を促進しましょう。
- IE専門家の育成:社内にIE専門家を育成し、継続的な改善活動をサポートできる体制を作りましょう。
IE手法は、中小製造業の現場においても、生産性向上を実現するための強力なツールです。経営層のコミットメント、現場の巻き込み、継続的な改善という3つの重要ファクターを意識し、IE手法を効果的に導入することで、あなたの現場は、ムダのない生産性の高い職場へと生まれ変わることでしょう。
まとめ:IE手法完全ガイド:7つ道具と実践事例
さて、今回はIE手法の基礎から実践的な活用方法、そしてトヨタ生産方式における活用事例や最新技術との融合、さらには未来展望まで、幅広く解説してきました。
IE手法は、決して大企業だけのツールではなく、中小製造業の現場でも、比較的お手軽に、そして効果的に導入することができます。
あなたの現場にも、まだ見えていない「ムダ」が潜んでいます。
- 作業時間の長さに悩んでいませんか?
- 設備や人員がフル活用されていないと感じていませんか?
- 生産ラインの効率が悪く、納期に間に合わないことはありませんか?
- モノの移動に無駄が多く、作業効率が低いと感じていませんか?
- 事務作業に時間がかかり、残業が増えていませんか?
これらの悩みは、IE手法の7つ道具を活用することで解決できるかもしれません。
- 時間研究:作業時間を細かく測定し、ムダな動きを特定する
- 稼働分析:設備や人員の稼働状況を把握し、非効率な部分を改善する
- 工程分析:生産ライン全体の流れを分析し、ムダな工程やボトルネックを解消する
- 作業分析:作業者の動作を分析し、ムダな動きを排除する
- レイアウト分析:作業空間の配置を見直し、ムダな移動を削減する
- マテハン分析:モノの移動を効率化し、運搬コストを削減する
- 事務工程分析:事務作業の流れを分析し、ムダな作業を排除する
これらIE手法の7つ道具を使いこなすことで、あなたは現場の「見えないムダ」を「見える化」できるので、具体的な改善策を生み出す前提を整えることができるようになります。
IE手法導入は、決して難しいことではなく、小さな一歩から始め、改善を積み重ねていくことで、あなたの現場は、そして会社は、大きく変わることができます。
トヨタ自動車のように、世界に誇る生産性を実現するのも夢ではありません。
さあ、今日から、あなたの現場も「カイゼン」を自分のモノにしましょう!