TPS=トヨタ生産方式てよく聞くけど
その本質まで理解しているヒトって
大企業でも結構少ないのが現実です
でもこのTPSの優秀さを理解すれば
将来、自分達がどのような工場を
目指すべきか?の選択が広がります
なぜならこのトヨタ生産方式とは
多品種少量生産の時代だからこそ
真価を発揮する方式だからです
そこでTPS:トヨタ生産方式とは何か
どのようなスタイルの何が有効で
導入するには何が必要なのか?
今回は解説していこうと思います
ぜひ読み終えるまでのお時間
しばらくお付き合いください
TPS:トヨタ生産方式とは
それではいつものようにまずは
辞書から調べてみたいと思います
トヨタ生産方式(読み方)とよた‐せいさんほうしき
生産性向上への取り組みを体系化した業務方式の一つ。もとは、顧客のオプション選択などの組合わせで、1台ごとに異なる仕様で受注した車を生産するため、トヨタ自動車が確立した手法。「ジャストインタイム」や「自働化」などにより製造工程の無駄を排除する。1990年代、米国の研究者がリーン生産方式として紹介し、さまざまな業種に応用された。
[略称]TPS(Toyota Production System)
出典 デジタル大辞泉/小学館 より
簡単に説明すると
ムダを排除できる世界的に有名な
生産方式のひとつです
米国ではリーン生産方式と呼ばれ
もちろんトヨタ自動車が考えました
と言うか大野耐一という元副社長が
体系化したと言われていますが
この導入には3つの特殊の考え方が
必要だと言われています
考え方2:自働化
考え方3:人間尊重
ではこの3つの考え方について
前編&後編に分けて解説します
まずはその中でも重要な
ジャストインタイム=JITについて
考え方1:ジャストインタイム=JIT
英語でオンタイムは「定時に」
インタイムは「間に合わせる」の意
これにジャストを加えることで
ちょうど間に合う供給機能として
Just In Time:ジャストインタイム
の仕組みが必要になりこの実現が
トヨタ生産方式の大きな特徴です
その発想の元は在庫ムダの撲滅です
計画・見込生産の弊害=在庫増大
トヨタ自動車でも過去そうだったが
部品点数約3万点の自動車製品は
とにかく在庫が増えやすいのです
つまり計画・見込生産はどうしても
設備稼働効率を優先する仕組みが
働いてしまう構造を持っています
たとえばエンジンの製造工程が
以下の順番で構成されてたとします
生産工程 | 生産LT | 生産能力/日 |
コンロッド | 5分 | 500個 |
ピストン | 10分 | 250個 |
クランクシャフト | 15分 | 166個 |
シリンダヘッド | 30分 | 83個 |
シリンダーブロック | 15分 | 166個 |
まずコンロッドが1日500個生産
でも次のピストン生産は250個だけ
そうするとピストン前に差引き
250個の在庫が残ってしまいます
同様にクランクシャフト前には
250個-166個で84個
シリンダヘッド前には
166個-83個で83個
と、能力差分だけ積みあがりますね
さらに最終的にシリンダブロックの
166個の生産能力があるものの
シリンダヘッドの83個分しか
供給できない状況だということです
結果的に83個のエンジンを作るのに
コンロッド250個
ピストン84個
クランクシャフト83個の在庫を
生み出すことになるわけです
なんだそりゃ?ですよね
こんな状況がいまだに日本の
至る所で起こっているんです
部品点数分だけ在庫を生む
そのため自動車では約3万点の
在庫リスクを抱えることになります
恐ろしいほどのリスクです
しかも現代では同じカローラでも
カローラセダン
カローラスポーツ
カローラフィールダーなど
はたまたエンジンもハイブリッドや
ディーゼルやオプションも含めると
幾何学的に部品数は増えていく
多品種少量生産の時代
トヨタ自動車全体の在庫リスクは
販売量が増えれば増えるほど
倒産リスクが増大していったほど
だったとのことです
在庫増大が生み出すロスとは具体的に何?
在庫くらい何が大変なの?と思う
管理職はもう少し勉強が必要です
在庫は現金を食いつぶします
まず在庫は購入品であるので
原材料を買うだけの現金を使います
そして仕掛品は加工も進めてくので
後工程に進めば進むほどその分の
皆さまの給料や他経費もかさむので
その現金も支払っていきます
なので在庫が増えれば増えるほど
その分の現金が消費されていきます
一方で現金が増えるのは自動車が
売れて入金したタイミングであって
在庫の部品の分まで入ってきません
ご存じかと思いますが
会社が倒産するのは赤字が増えた時
ではなくてお金を支払なくなった時
そのため在庫はそのお金を減らす
しかもムダを生む元凶なわけです
その代表的なムダは以下のとおり
①在庫の置くスペースそのもの
②在庫を置く土地代や倉庫代
③在庫を移動させる時間
④在庫を移動させるヒト
⑤在庫を移動させる運搬設備代
⑥移動先の棚やパレットの購入費
⑦在庫管理システムの構築・運営費
⑧必要なくなった在庫の破棄費用
これらは在庫量に比例して増大します
この在庫問題をJust In Timeでは
徹底的に排除するために着想された
究極の考え方だと言われています
在庫を生み出さないジャストインタイム:JIT
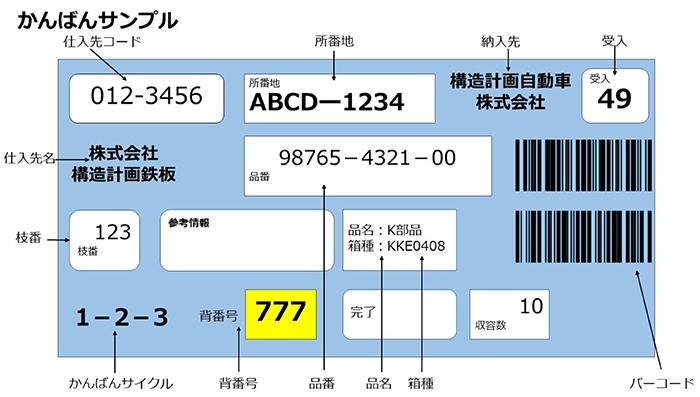
『かんばん』のサンプル画像 出典:構造計画研究所
ジャストインタイム:JITでは
『かんばん』という道具を使います
『かんばん』とは
使用側と供給側を行ったり来たりする
在庫制御ツールを指します
この『かんばん』を使うことで
各々の生産計画を立てることなく
自然と受給バランスが取れることで
不必要な在庫がなくなることを狙い
生み出された方法論です
『かんばん』の運用ルール
この『かんばん』ルールは簡単です
ある部品の『かんばん』どおり
部品が運搬されてきたとします
そして生産に使えば『かんばん』は
生産する側に生産指示として戻る
戻ったらその『かんばん』のとおり
生産して部品を運搬する
つまり『使われる分だけ生産する』
工程間の情報板として使うわけです
『かんばん』の運用メリット
たとえば先程のエンジンの例では
83個のエンジンを作るのに
83個のシリンダーブロックを要求し
83個のシリンダヘッドを要求し
83個のクランクシャフトを要求し
83個のピストンを要求し
83個のコンロッドを要求します
必要な時に必要なだけ必要な部品を
供給できる仕組みが回るということ
これで不必要な在庫は生まれません
すごいのは何のシステム投資もなく
『かんばん』という道具だけで
在庫が生まれないしくみを生み出し
日程計画の策定時間もなくすなど
大きな運用メリットが出てきます
これは画期的な運用システムです
ですが画期的なゆえにその運用には
3つの改善の推進が前提になります
ジャストインタイムに必要な3つの前提
前述の通りジャストインタイムとは
設備稼働効率を優先するのではなく
在庫最少化を実現する考え方だと
そしてその運用には
3つの改善が前提になり
その3つの改善とは以下の通りです
改善1:生産の平準化
改善2:多能工化
改善3:段取替え時間の短縮
それぞれどういった改善なのか
少し補足をしていきましょう
改善1:生産の平準化
『かんばん』を回すにはある程度
安定した生産量が維持できないと
効率化に結びつきません
たとえばエンジンの例でいくと
ある日の需要量が50個で
次の日の需要量が100個だった時
1日目はエンジン生産50個に対して
各50個の『かんばん』が回って
在庫は発生しません
しかし次の日の100個は
各100個の『かんばん』が回っても
シリンダーヘッド83個がMAXなので
17個不足することになります
しかしこの不足17個を事前調整で
前日に作りだめするように生産量を
平準化する改善機能を装備すれば
『かんばん』は正常に機能します
つまり需要が変動しても
生産量が平準化できる機能や仕組み
それは業種・業態や取引先により
最適なスタイルが変わってくるため
各スタッフの工夫や改善力が
試される、というわけです
改善2:多能工化
次に重要になるのは多能工化です
今回のエンジンの例では
シリンダーヘッド工程が83個と
全体の生産量=スループットを
決めている構図となっています
だったらこの83個を増やせば
全体の効率は向上するはずですよね
そのための有効な方法が
多能工化への改善です
多能工(読み方)たのう‐こう
複数の工程に対応できる技術をもつ工員。
[反対語]単能工
出典 デジタル大辞泉/小学館 より
作業員は一人ひとり
出来ることが違い得意不得意もある
だけど大切で難しい作業ほど
一定のヒトしか対応できない状況は
非常にリスクが高い状態です
なぜならそのヒトが病気や退社等で
席を外す事件が起こるとすぐさま
その職場のQCDレベルが落ちます
だから多能工化を進めよう!とする
職場も多いんじゃないかと思います
ただしこのジャストインタイムでは
この多能工化が進むことで
その他の余剰工程の能力を使え
その結果ボトルネック工程の能力を
向上できる可能性に期待します
つまりシリンダーヘッド生産83個を
余剰工程の行員の多能工化を進めて
シリンダヘッド工程を助けることで
90個に、あるいは100個できないか
相互補助の精神で助けることで
全体効率を高める能力を装備する
こういった改善が2番目に
重要な改善だということです
改善3:段取替え時間の短縮
対品種少量生産において重要なのは
同設備で多くの品種を少量生産する
機会が多いことを再認識することです
そうすると、大量生産では必要ない
段取替えが必ず必要になってきます
ただし。。。
この段取替えを嫌がる職場は多い
なぜなら時間がかかるからです
そりゃ誰だって同じ生産を続ける
効率的で楽で手間がかからない
大量生産をみんなずっとしていたい
けど、そういう時代は戻って来ない
だから。。。
ぜひ、あきらめてください!笑
あきらめた上でこの段取替え時間を
短縮していく改善に真剣に取り組む
そのための工夫とアイデアを試行錯誤し
独自ノウハウとして蓄積していく
ジャストインタイムの実現には
必ずこの改善も必要になります
実際にトヨタ自動車は昭和20年代
何トンもある金型の段取替えに
3時間もかかっていたらしい
ところが改善に改善を重ねて
昭和40年後半には3分まで短縮
3分だったら、1日に何回も
段取替えしても大丈夫ですよね
皆さまの職場はどうですか?
っていうことなんです
TPS:トヨタ生産方式とは何か?(前編)まとめ
まずは前編としてもっとも重要な
ジャストインタイムについて
簡単に解説を進めてみました
うちには無理かなぁと思う方へ
2つメッセージとしてお伝えします
3つの改善が進まないと思う方へ
ジャストインタイムでなくても
必要となる改善だと思います
多能工化は進んでも
平準化と段取替え改善はできない
これはいつか他社に負ける構図です
覚悟しておいて損はないと思います
我社の受注体系と合わないと思う方へ
これは応用問題です
計画・見込生産のプッシュでなく
『かんばん』の引っ張る構図で
在庫をゼロにする仕掛け
そのままズバリはできなくても
このJITを自社流に応用するなら
どんな形がベターなのか?
ぜひお仲間と考えてみてください!
仲間いなければ一緒に考えますので
お問い合わせフォームから相談下さい
そして、理解が進まなかった方は
後編をまとめて読めば
きっと理解は深まるはずです
ぜひ続編を楽しみにお待ちください
[getpost id=”5500″]
それでは今日はここまでです
今後とも宜しくお付き合い下さい☆
長文乱文を最後まで読んでくださり
いつもありがとうございます♪
すべては御社の発展のために
すべてはあなたの笑顔のために