多くの製造業では、多かれ少なかれ5S活動に取り組んでいるとは思います。しかし、現実には5S活動がうまくいかず、かえって工場を追い詰めてしまうケースも少なくありません。5S活動が形骸化したり、現場の実情を無視したトップダウンの活動になったりすると、従業員のモチベーションが低下し、生産性や品質にも悪影響を及ぼします。
そこで今回は5S活動を進めるうえで生まれるデメリットが工場を追い詰める3つの理由について解説を進めたいと思います。そして、製造業で5S活動を成功させるための正しい進め方についても紹介します。なのでぜひ、現場のリーダーとして5S活動を効果的に推進するためのヒントを見つけていただければと思います。
5S活動は、本来は製造業の現場に大きなメリットをもたらすはずのものです。しかし、なぜ5S活動が工場を追い詰めてしまうのでしょうか。その理由を知り、正しい進め方を理解することが、5S活動を成功させるための鍵となります。
では今回も読み終えるまでのお時間、しばらくお付き合いください。
5Sという活動について
5S活動とは、職場環境の改善を通じて生産性と品質の向上を目指す活動です。まず5Sの各要素について理解し、その目的を明確にすることが重要です。また、製造業における5S活動の重要性を認識し、期待される効果と現実のギャップを把握することが、活動を成功させるための第一歩となります。
5S活動の定義と目的
5Sとは、「整理・整頓・清掃・清潔・習慣(しつけ)」の頭文字をとったものです。各要素の意味は以下の通りです。
整理(Seiri):不要なものを取り除き、必要なものだけを残すこと
整頓(Seiton):必要なものを使いやすく配置すること
清掃(Seiso):職場を清潔に保ち、異常を発見しやすくすること
清潔(Seiketsu):整理・整頓・清掃を維持するため、未然防止策を考えること
習慣/しつけ(Syukan/Shitsuke):決められたルールを守り、しっかり5S活動を習慣化すること
5S活動を進めて職場環境を整えることで、以下のような効果を得ることができます。
- ムダな作業を減らし、生産性を向上させる
- 不良品の発生を防ぎ、品質を向上させる
- 事故やけがのリスクを減らし、安全性を高める
- 従業員のモラルを向上させ、働きやすい職場環境を作る
製造業における5S活動の重要性
製造業では、5Sの活動レベルが工場の評価とされることが一般的です。その理由は以下の通りです
- 生産性:整理整頓された職場では、必要なものがすぐに取り出せるため、作業効率が上がります。
- 品質:清潔な職場環境では、不良品の発生率が低下します。
- 安全性:整理整頓された職場では、事故のリスクが減ります。
- コスト:ムダな作業や在庫が減ることで、コストが削減できます。
- 従業員のモラル:働きやすい職場環境では、従業員のモチベーションが上がります。
製造業において、5S活動は品質管理や生産管理の基礎となる活動であり、継続的に取り組むことが求められています。
5S活動に期待される効果と現実のギャップ
多くの企業が5S活動に取り組む理由は、生産性や品質の向上を期待してのことです。しかし、実際には期待通りの効果が得られないケースも少なくありません。
その原因の一つは、5S活動が形骸化してしまうことです。例えば、「整理・整頓」に力を入れるあまり、現場の実情を無視した非現実的なルールを設定してしまうと、従業員の反発を招き、活動がカタチだけとなってしまい、実質的な効果を生み出さなくなります。
また、5S活動の効果を定量的に測定する仕組みがないと、活動を継続するためのモチベーションが維持できません。さらに、フィードバックループが欠如していると、5S活動の改善が進まず、期待された効果が得られないことがあります。
5S活動に取り組む際は、これらのギャップを理解し、適切な進め方を選ぶことが重要です。
5S活動の失敗事例が示す3つのデメリット
5S活動は、正しく行えば生産性や品質の向上につながる一方で、間違った方法で進めると逆効果になることがあります。ここでは、5S活動の失敗事例から見えてくる3つのデメリットについて解説します。
デメリット1:形式的な5S活動が生産性向上を阻害する
最初のデメリットは形式的な5S活動となってしまった場合には、生産性工場を逆に阻害してしまう状況が起こることです。
5S活動の形骸化がもたらす悪影響
形式的な5S活動は、現場の実態から乖離し、従業員の反発を招きます。その結果、ムダな作業が増え、生産性が低下してしまいます。
現場の実情を反映しない5S活動の弊害
現場の意見を取り入れずに決められた5Sルールは、現実的でない場合があります。そのような活動は、従業員のモチベーションを下げ、定着を妨げてしまいます。
効果測定方法の誤りが改善を遅らせる原因
5S活動の効果を適切に測定しないと、改善点が見えてきません。不適切な効果測定方法では、改善が遅れ、生産性向上の機会を逃してしまうでしょう。
デメリット2:無駄な時間と労力を強いる5S活動
2つ目のデメリットは、ただただ、ムダな時間と労力をかけただけになる5S活動となってしまい勝ちになることです。
現場の声を無視した5S活動の弊害
現場の意見を聞かずに決められた5Sルールは、従業員にとって負担になります。そのような活動は、不満を募らせ、協力を得られなくなってしまいます。
過剰な5S活動がもたらす従業員のモチベーション低下
必要以上に厳しい5Sルールを設定すると、従業員の負担が増え、モチベーションが下がります。それにより、本来の業務に支障をきたし、生産性の低下を招いてしまうのです。
デメリット3:リーダーシップとチームワークの欠如が5S活動を失敗に導く
最後のデメリットは、リーダーシップとチームワークを育てないまま5S活動を進めてしまうと、その後の組織体制にも大きな悪い影響を及ぼすことになることです。
5S活動におけるリーダーの役割と重要性
5S活動を推進するリーダーは、現場の意見に耳を傾け、適切な判断を下す必要があります。活動の成否は、リーダーの理解と行動にかかっているのです。
チームワークの欠如が5S活動の効果を低下させる
5S活動は、現場の全員が協力して取り組む必要があります。チームワークが欠如していると、効果が上がらず、形骸化してしまうでしょう。
これらの失敗事例から学び、5S活動のデメリットを理解することが、活動を成功させるための第一歩です。次の章では、5S活動の失敗が工場に与える影響について詳しく見ていきます。
追い詰められた工場はその後どうなってしまうのか?
5S活動の失敗は、工場に深刻な影響を与えます。生産性の低下、品質管理の悪化、従業員のモチベーション低下など、様々な問題が連鎖的に発生し、工場を追い詰めてしまうのです。
想定される結果1:生産性の低下と納期遅延の連鎖
まずは生産性が低下するうえに、納期遅延の危険性まで高まることです。
5S活動の失敗による現場の混乱と生産効率の低下
5S活動が失敗に終わると、現場は混乱し、かえって生産効率が大幅に低下します。必要な工具や部品が見つからない、作業スペースが確保できないなど、様々な問題が発生し、スムーズな作業が困難にります。
生産性低下が納期遅延を引き起こす悪循環
そういった生産効率の低下は、必ず後に納期遅延につながります。そうなれば納期を守るために残業が増え、従業員の負担が増大します。そうした状況が続くと、更なる生産性の低下を招き、悪循環に陥ってしまうことになります。怖いですよねー。
納期遅延による顧客満足度の低下と信頼の喪失
納期遅延は、顧客満足度の低下を招きます。約束した納期を守れない状況が続けば、顧客との信頼関係が損なわれ、取引を失うリスクが高まります。
想定される結果2:品質管理の悪化と不良品の増加
そして品質管理体制が弱くなっていき、結果的に不良品が増加する結果が予測できます。
5S活動の形骸化が品質管理体制を弱体化させる
形骸化した5S活動は、品質管理体制を弱体化させます。整理・整頓・清掃が適切に行われない状態では、不良品の発生を防ぐことが難しくなります。
品質管理の悪化が不良品の増加を招く
品質管理体制の弱体化は、不良品の増加につながります。不良品が出荷されてしまえば、顧客からのクレームや返品が増え、手直しのための工数が増大します。
不良品の増加による収益の悪化と企業イメージの低下
不良品の増加は、収益の悪化を招きます。手直しや返品対応のコストが増え、利益率が低下するのです。また、品質の低下は企業イメージにも悪影響を与え、競争力の低下につながります。
想定される結果3:従業員のモチベーション低下と離職率の上昇
そういった状態が続けば働く側の意欲にも大きな影響を及ぼすようになります。
無駄な5S活動が従業員のモチベーションを低下させる
無駄な5S活動は、従業員のモチベーションを低下させます。形式的で現場の実情に合わない活動に時間を割かれることで、本来の業務に集中できなくなるのです。
モチベーション低下が離職率の上昇を招く
モチベーションの低下は、離職率の上昇につながります。働きがいを感じられない職場環境では、優秀な人材が去っていってしまいます。
熟練工の離職が生産技術の継承を困難にする
特に、熟練工の離職は深刻な問題です。長年培ってきた技術やノウハウが失われ、生産技術の継承が困難になります。
このように、5S活動の失敗は工場に様々な悪影響を及ぼし、競争力の低下や存続の危機につながりかねません。
工場を追い詰める3つの理由
5S活動が失敗に終わり、工場を追い詰めてしまう原因は様々ありますが、ここでは特に重要な3つの理由について解説します。
理由1:5S活動の本質的な目的の理解不足
まずは5S活動の本質的な目的について、理解が進んでいないことです。
5S活動を単なる整理整頓と捉える表面的な理解
5S活動を単なる整理整頓と捉える表面的な理解は、活動の本質を見失わせます。5Sは、整理整頓だけでなく、ムダの削減や業務の標準化など、生産性向上に直結する活動なのです。
5S活動が目指す生産性向上や品質管理の意義を見失う
5S活動の本質的な目的である生産性向上や品質管理の意義を理解していないと、活動の優先順位を誤ってしまいます。目的を見失った活動は、形骸化し、効果を発揮できなくなります。
目的理解の欠如が形骸化した5S活動を招く
5S活動の目的を理解していない状態では、形式的な活動に陥りやすくなります。現場の実情に合わない形骸化した活動は、従業員の反発を招き、定着しません。
理由2:現場の実情を無視したトップダウンの5S活動
次の理由は現場の状況を考慮せずに、トップの命令のみで5S活動を進めると従業員を追い詰めてしまうことにつながりますので注意してください。
現場の声を聞かずに5S活動を押し付ける管理者
現場の声を聞かずに5S活動を押し付ける管理者は、現場の実情を理解していません。現場の意見を取り入れない一方的な指示は、従業員の反発を招き、活動の定着を妨げます。
現場の実情を考慮しない非現実的な5S活動の要求
現場の実情を考慮しない非現実的な5S活動の要求は、従業員に過度な負担を強います。実現不可能な目標を掲げられても、現場は混乱するだけです。
トップダウンの5S活動が現場の反発を招き、活動が形骸化
トップダウンで進められる5S活動は、現場の反発を招きやすくなります。現場の理解と協力を得られない活動は、形骸化し、効果を発揮できなくなってしまいます。
理由3:5S活動の効果測定とフィードバックの欠如
最後は実際に進めた5S活動に対する効果測定を進めること、またそれらをフィードバックが欠如していることが、よくある状況です。そりゃ、実行している側を追い込みますよね。
5S活動の効果を定量的に測定する仕組みの不在
5S活動の効果を定量的に測定する仕組みがないと、活動の成果を把握できません。効果が見えない状態では、改善につなげることが難しくなります。
効果測定なしで5S活動を継続するための動機づけの欠如
効果測定なしで5S活動を継続すると、従業員のモチベーションが低下します。活動の意義が実感できない状況では、継続的な取り組みを維持することが困難になるのです。
フィードバックループの欠如が5S活動の改善を阻害
フィードバックループが欠如していると、5S活動の改善が進みません。効果測定の結果を活動に反映させる仕組みがなければ、同じ失敗を繰り返すことになってしまいます。
以上の3つの理由が、5S活動の失敗を招き、工場を追い詰めてしまうのです。では、こうした失敗を避け、5S活動を成功させるにはどうすればよいのでしょうか。次の章では、その具体的な方法について見ていきます。
製造業で5S活動を成功させるための正しい進め方
5S活動を成功させるためには、現場主導の活動推進、効果の最大化、成功事例からの学ぶことが重要となります。ここでは、それぞれの点について詳しく解説します。
進め方1:現場主導の5S活動の推進と定着
まずは現場を主導とした5S活動の推進を進めること、そしてその定着を図るためのしくみづくりが大切です。
現場の意見を取り入れた5S活動の計画立案
5S活動の計画立案では、現場の意見を取り入れることが重要です。現場の従業員は、日々の業務の中で改善点や問題点を最もよく知っています。その知見を活かすことで、実効性の高い計画を立てることができるのです。
全員参加型の5S活動で改善意識を醸成
5S活動は、現場の全員が参加することで、改善意識を醸成できます。一人一人が主体的に活動に関わることで、職場環境を改善しようという意識が高まります。全員参加型の活動は、5Sの定着にも役立ちます。
5S活動の定着化のための教育と啓発活動
5S活動を定着させるためには、教育と啓発活動が欠かせません。従業員に5Sの意義や方法を正しく理解してもらうための研修を行い、活動の重要性を繰り返し伝えることが必要です。
進め方2:5S活動の効果を最大化するためのポイントを推させる
そしてせっかく活動した5S活動の効果を最大化するために押さえるべきポイントを把握し、実行に移すことです。
明確な目的と目標設定による5S活動の方向性確保
5S活動の効果を最大化するには、明確な目的と目標設定が重要です。活動の方向性を明確にすることで、従業員の意識を一つの方向に集中させることができます。目的や目標は、具体的かつ達成可能なものであることが求められます。
定期的な5S活動の評価と改善サイクルの実践
5S活動の評価と改善サイクルを定期的に実践することも、効果の最大化につながります。活動の成果を定量的に評価し、改善点を明らかにすることで、PDCAサイクルを回すことができるのです。
5S活動の効果測定方法の確立と適切な運用
5S活動の効果測定方法を確立し、適切に運用することも重要です。生産性や品質、作業環境など、様々な指標を用いて活動の成果を可視化することで、従業員のモチベーションを高め、活動の継続性を担保できます。
進め方3:5S活動の成功事例から教訓を学ぶ
さらにはやはり多くの製造業で実行されている5S活動ですから、成功事例も多く存在しています。そのためそこから学ぶことはとても大切な感覚です。
製造業における5S活動の成功事例とその要因
製造業における5S活動の成功事例を分析することで、多くの教訓を得ることができます。成功企業がどのように5S活動を進めているのか、どのような工夫を行っているのかを学ぶことが重要です。
成功事例から学ぶ5S活動の適切な進め方
成功事例から学んだ知見を自社の5S活動に活かすことが、適切な進め方につながります。他社の事例をそのまま真似るのではなく、自社の状況に合わせて応用することが求められます。
自社の5S活動への応用と展開のための留意点
自社の5S活動への応用と展開には、いくつかの留意点があります。自社の組織文化や業務の特性を考慮し、無理のない形で5Sを導入することが重要です。また、活動の進捗状況を定期的に確認し、必要に応じて軌道修正を行うことも必要不可欠です。
以上のような正しい進め方を実践することで、製造業における5S活動の成功確率を高めることができるのです。次の章では、5S活動の効果をさらに高めるためのツールと手法について解説します。
5S活動の効果を最大化するためのツールと手法
5S活動の効果を最大化するためには、適切なツールの活用と効果的な手法の導入が欠かせません。ここでは、5S活動を支援するツールと、効果を高めるための手法について詳しく解説します。
5S活動を支援する定番ツールの活用
5S活動の効果を高めるためには、5S活動で使われている定番ツールを使うことが有効です。ではどんなツールがあるのか見ていきましょう。
5S活動チェックリストの作成と運用
5S活動チェックリストは、活動の進捗状況を確認し、改善点を明らかにするための重要なツールです。チェックリストを作成し、定期的に運用することで、5Sの定着度を評価し、必要な対策を講じることができます。
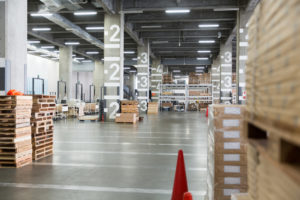
5S活動の見える化ツールの導入と効果
5S活動の見える化ツールを導入することで、活動の成果を視覚的に把握することができます。例えば、5S活動の報告書を作成して貼り出していることで、5S活動でどの程度改善が進んでいるのか?と見える化することができます。そのことによって改善に前向きな工場であることをアピールできて、実際の引き合いに繋がることもあるため強力です。それに単純に、自分の報告書が貼りだしてあったら「もっと頑張らなきゃ」って思いますよね。

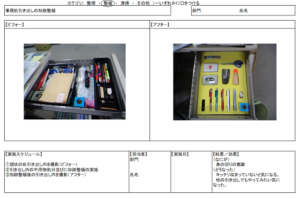
ITツールを活用した5S活動の効率化
ITツールを活用することで、5S活動の効率化を図ることができます。例えば、タブレット端末を用いて現場の情報を収集・共有したり、専用のソフトウェアを使って活動の進捗管理を行ったりすることで、ペーパーレス化や業務の自動化を進められます。

5S活動の効果を高めるための手法
また定番ツール以外にも5S活動の効果を高める手法がいくつか存在していますので、ぜひ連携しながら進めてください。そんな手法もいくつか紹介しておきましょう。
5S活動と他の改善活動との連携
5S活動と他の改善活動を連携させることで、相乗効果を生み出すことができます。例えば、TPM(Total Productive Maintenance)やQC(Quality Control)活動と5Sを組み合わせることで、設備の稼働率向上や不良品の削減につなげられます。
5S活動の成果を評価するための指標設定
5S活動の成果を適切に評価するためには、明確な指標設定が重要です。生産性、品質、安全性など、様々な観点から指標を設定し、定期的に測定・分析することで、活動の効果を定量的に把握できます。
5S活動の優良事例の共有と横展開
5S活動の優良事例を社内で共有し、他部門への横展開を図ることも効果的です。成功事例を共有することで、従業員の意識を高め、活動へのモチベーションを高められます。また、他部門での導入を促進することで、会社全体での5Sレベルの向上を図ることができるのです。
以上のようなツールと手法を積極的に活用することで、5S活動の効果を最大限に引き出すことが可能となります。次の章では、5S活動を正しく進めることの重要性と、それによって期待される効果について解説します。
5S活動の正しい進め方の重要性と期待される効果
5S活動を正しく進めることは、製造業の競争力強化と継続的な改善・発展において非常に重要な役割を果たします。ここでは、その重要性と期待される効果について詳しく解説します。
製造業の競争力強化における5S活動の役割
製造業において、5S活動は競争力強化の基盤となる取り組みです。5Sを正しく実践することで、以下のような効果が期待でき、企業の競争力向上につながります。
- 生産性の向上 整理整頓された職場環境では、ムダな動作や探し物の時間が減り、作業効率が向上します。また、不要なものを排除することで、スペースの有効活用が図れ、生産性の向上につながります。
- 品質の向上 清潔で整然とした職場環境は、不良品の発生を防ぎ、品質の向上に寄与します。また、5Sの実践により、作業手順の標準化が進み、品質のばらつきを抑えることができます。
- 安全性の向上 整理整頓された職場では、作業者の動線が確保され、事故やけがのリスクが減少します。また、危険物の管理や機械設備の点検が徹底され、安全性の向上が図れます。
- 従業員のモラルとモチベーションの向上 5S活動に積極的に取り組む職場では、従業員のモラルとモチベーションが向上します。自分たちの職場環境を自ら改善する活動を通じて、従業員の自主性と責任感が高まるのです。
これらの効果を総合的に発揮することで、製造業の競争力強化に大きく貢献できます。
継続的な5S活動の改善と発展の必要性
5S活動は、一度実践すれば終わりではありません。継続的な改善と発展が必要不可欠です。以下のような取り組みを通じて、5S活動を進化させていくことが求められます。
- PDCAサイクルの実践 5S活動の成果を定期的に評価し、改善点を明らかにすることが重要です。計画(Plan)、実行(Do)、評価(Check)、改善(Act)のサイクルを回すことで、活動のレベルアップを図ることができます。
- 従業員の意識と行動の変革 5S活動を定着させ、更なる改善を進めるには、従業員の意識と行動の変革が欠かせません。教育や啓発活動を通じて、5Sの重要性を浸透させ、自発的な取り組みを促進することが必要です。
- 他の改善活動との融合 5S活動を他の改善活動と融合させることで、より高い効果を生み出すことができます。例えば、カイゼン活動やリーン生産方式と5Sを組み合わせることで、現場の改善を加速させられます。
- ベストプラクティスの共有と水平展開 社内外の優良事例を共有し、自社の活動に取り入れることも重要です。他部門や他社の成功事例から学び、自社の状況に合わせて応用することで、5S活動の質を高められます。
以上のように、5S活動を正しく進め、継続的な改善と発展を図ることは、製造業の競争力強化に直結する重要な取り組みなのです。
まとめ:5S活動のデメリットが工場を追い詰める3つの理由
本ブログ記事では、5S活動のデメリットが工場を追い詰める3つの理由について詳しく解説してきました。
- 5S活動の本質的な目的の理解不足
- 現場の実情を無視したトップダウンの5S活動
- 5S活動の効果測定とフィードバックの欠如
これらの理由により、5S活動が形骸化し、現場の生産性や品質、従業員のモチベーションに悪影響を及ぼしてしまうのです。
しかし、5S活動は製造業の競争力強化には欠かせない取り組みです。正しい進め方を実践することで、生産性の向上、品質の向上、安全性の向上、従業員のモラルとモチベーションの向上など、様々な効果を期待できます。
そのためには、現場主導の5S活動の推進と定着、効果の最大化、成功事例からの学びが重要です。また、適切なツールの活用と効果的な手法の導入により、5S活動の質を高めることも可能です。
説明したとおり5Sは単なる整理整頓ではありません。工場の競争力を高め、従業員が誇りを持って働ける職場環境を作るための重要な活動なのです。一人一人が5Sの本質を理解し、自主的に取り組むことが求められます。
現状に満足せず、常に改善を心がける姿勢が、5S活動の成功と工場の発展につながります。みなさんの職場から、5S活動の改革を始めませんか?小さな一歩が、大きな変化を生み出します。
5Sの真の力を信じ、継続的な改善と発展に挑戦し続けましょう。みなさんの行動が、日本の製造業の未来を切り拓くのです。さあ、今すぐ5S活動の改善に取り組みましょう!
もし、確認したいことがあれば以下まで気軽にZOOMでの無料相談をお申込みいただければと思います。
滋賀県よろず支援拠点> https://www.shigaplaza.or.jp/yorozu/contact
※ 西本を指名すれば、全国どこからでも申込み可能です。
それでは今日はここまでです。今後とも宜しくお付き合い下さい☆
長文乱文を最後まで読んでくださりいつもありがとうございます♪
すべては御社の発展のために、すべてはあなたの笑顔のために