現場で品質管理に携わる皆さんはもちろんQC7つ道具をご存知かと思います。「品質管理の基本」として知られるQC7つ道具は、データ分析や問題解決に欠かせない手法です。しかし、名前だけ聞いても具体的な使い方がわからない、という方も多いのではないでしょうか。
そこで今回は、QC7つ道具と新QC7つ道具について、初心者でも理解が進むよう、きるだけわかりやすく解説し、その覚え方や実際の活用方法まで詳しく紹介したいと思います。
そりゃ、QC7つ道具は現場の問題解決に役立つ強力なツールであるため、多くの製造現場で活躍しています。ぜひ改めて読み込んで、あなたの品質改善力を高めてくださいませ。
それでは今回も読み終えるまでのお時間、しばらくおつかいくださいませ。
【初心者向け】QC7つ道具・新QC7つ道具を分かりやすく解説!
それでは品質管理の現場で活用されるQC7つ道具と新QC7つ道具について、それぞれの目的や使い方、違いについて詳しく解説していくこととしましょう。
QC7つ道具・新QC7つ道具とは?
まず、QC7つ道具とは、品質管理に必要な基本的な手法のことです。具体的には、一般的なデータ分析ツールのグラフに始まり、チェックシート、パレート図、散布図、特性要因図、ヒストグラム、管理図の7つがあります。これらのツールを使うことで、データを視覚化し、たくさんのメンバー間で問題の原因を明らかにして共有することができるようになります。
一方、新QC7つ道具は、従来のQC7つ道具を補完するための手法で、主に言語データを扱います。親和図法、連関図法、系統図法、マトリックス図法、アローダイヤグラム法、PDPC法、マトリックスデータ解析法の7つがあり、複雑な問題の整理や対策の策定に役立ちます。
どちらも品質管理の強力なツールですが、扱うデータや目的が異なるため、使い分けが重要です。次のセクションでは、それぞれの道具を使う目的について詳しく見ていきましょう。
QC7つ道具・新QC7つ道具を使う目的
QC7つ道具と新QC7つ道具は、どちらも品質管理の現場で重要な役割を果たしますが、それぞれに異なる目的があります。QC7つ道具は、主に数値データを視覚化し、現状の把握や問題の原因分析に使用されます。例えば、パレート図を使えば、不良品の発生原因を一目で特定することができます。また、散布図を使うことで、二つの変数間の関係性を視覚的に確認することが可能です。
一方、新QC7つ道具は、言語データを整理し、複雑な問題の因果関係を明確にするために用いられます。親和図法を使えば、関係者の意見をまとめ、問題点を明確にすることができます。また、連関図法を使うことで、原因と結果の関係を論理的に整理し、問題の核心に迫ることができます。
このように、QC7つ道具と新QC7つ道具をうまく使い分けることで、品質改善の効果を最大限に引き出すことができる、というわけです。これは使わない手はないですよね。
QC7つ道具と新QC7つ道具の違い
以下に、QC7つ道具と新QC7つ道具の違いについて、それぞれのツールとその用途を表にまとめました。
【QC7つ道具の7つのツールと用途】
ツール | 用途 |
---|---|
グラフ | データを視覚的に表現する |
チェックシート | データの収集や確認作業を効率化する |
パレート図 | 重要な問題を特定する |
散布図 | 二つの変数の関係性を把握する |
特性要因図 | 問題の原因を洗い出す |
ヒストグラム | データの分布を視覚化する |
管理図 | プロセスの安定性を監視する |
【新QC7つ道具の7つのツールと用途】
ツール | 用途 |
---|---|
親和図法 | 問題点を明確にする |
連関図法 | 因果関係を整理する |
系統図法 | 目的達成の手段を整理する |
マトリックス図法 | 要素の関連性を分析する |
アローダイヤグラム法 | 計画を視覚的に整理する |
PDPC法 | リスクや問題の対策を整理する |
マトリックスデータ解析法 | 複雑なデータを分析する |
QC7つ道具と新QC7つ道具の違いは、扱うデータの種類と使用目的にあります。QC7つ道具は数値データを扱い、具体的な数値に基づいた分析を行います。例えば、ヒストグラムを使うことで、データの分布を視覚化し、異常値やばらつきを簡単に確認することができます。また、管理図を使えば、工程の安定性を継続的に監視し、異常が発生した場合にすぐに対応することができます。
新QC7つ道具は、言語データを扱うため、数値では捉えにくい複雑な問題や人間関係の整理に役立ちます。例えば、親和図法を使うことで、関係者全員の意見をまとめ、問題の本質を浮き彫りにすることができます。さらに、系統図法を使えば、目的達成のための具体的な手段を系統的に整理することができたります。
このように、QC7つ道具と新QC7つ道具はそれぞれの強みを持っており、現場の状況に応じて適切に使い分けることが重要ですが、それにはどれがどのような特徴を持っているのか理解することが必要であり、やはり使ってみないことには実感はわかないですよね。
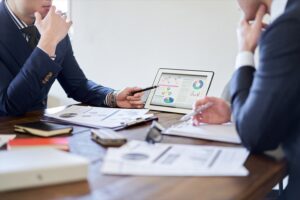
【基礎】品質改善の基本!データ分析の前に知っておきたい「層別」
そして、これらデータ分析を行う前に、層別の重要性を理解することが品質改善の基本です。ここでは、層別の必要性や具体的な方法について、初心者でも理解いただけるようわかりやすく解説したいと思いますので、ぜひお付き合いください。
層別とは?なぜ層別が必要なの?
層別とは、データを特定の基準で分類・分割することを指します。例えば、製品の不良率を分析する際に、製造ラインごとにデータを分けることが層別の一例です。層別が必要な理由は、データを分類することで、全体では見えにくかった傾向や問題点が見えてくるからです。
具体的に、全体のデータだけでは特定の問題の原因が分からないことがあります。しかし、層別を行うことで、例えば「どの製造ラインで不良品が多いのか」や「ある特定の時間帯にだけ問題が集中している」といった細かな情報が得られます。これにより、問題の原因を特定しやすくなり、効果的な改善策を講じることができる、というわけです。
次に、層別の具体的な進め方についての5つのステップを解説します。
【簡単】層別の方法をステップで解説
層別の方法はシンプルですが、効果的なデータ分析のために重要です。以下のステップで簡単に層別を行うことができます。
まず、何を明らかにしたいのかをはっきりさせます。例えば、「特定の製造ラインの不良品率を分析する」といった具体的な目的を設定します。
次に、データをどの基準で分類するかを決めます。製造ライン、時間帯、シフト、原材料の種類など、目的に応じた基準を選びます。
分類基準に基づいてデータを集めます。この際、データの正確性と一貫性を保つことが重要です。
集めたデータを選んだ基準に従って分類します。エクセルや専用の分析ソフトを使用すると便利です。
分類されたデータを分析し、傾向や問題点を明らかにします。例えば、特定の製造ラインで不良品率が高い場合、その原因をさらに深掘りして調査します。
このように、層別はデータ分析の基礎であり、問題解決への第一歩となります。次に、層別を行う際の注意点について見ていきましょう。
【注意】層別をするときのポイント
層別を行う際には、いくつかの注意点があります。これらを押さえておくことで、より効果的な分析が可能になります。
注意点1:分類する基準は慎重に選ぶこと
まず、分類基準の選定は慎重に行う必要があります。適切な基準を選ばなければ、正確な分析結果を得ることができません。例えば、製造ラインごとの不良品率を分析する際に、ラインを正しく識別しなければ、データが意味を持たなくなります。
注意点2:データの正確性と一貫性を保つこと
次に、データの正確性と一貫性を保つことが重要です。データの収集時に誤りがあれば、分析結果も正しくなくなります。データを収集する際には、標準化された手順を守り、全てのデータが同じ基準で記録されていることを確認しましょう。
注意点3:データを過信しすぎないこと
また、層別したデータの結果を過信しすぎないことも大切です。データが示す傾向や問題点を深く掘り下げ、他の要因との関連性を検討することが必要です。単一のデータだけで結論を出すのではなく、他のデータや情報と照らし合わせることで、より正確な分析が可能になります。
以上のポイントを踏まえて、層別を行うことで、品質改善の効果を最大限に引き出すことができます。
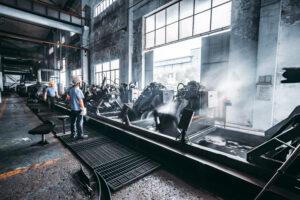
いろんなグラフを使いこなそう!
品質管理やデータ分析の現場では、データを視覚的に表現するためにさまざまな種類のグラフを使用します。ここでは、各種グラフの特徴と使い方について詳しく解説します。
棒グラフ
棒グラフは、データの比較を視覚的にわかりやすく示すための基本的なグラフです。縦軸に数値を、横軸にカテゴリを配置し、各カテゴリの値を棒の長さで表現します。
棒グラフの大きな特徴は、異なるデータセットを比較するのに適している点です。例えば、各月の売上や各製造ラインの不良品数など、カテゴリごとのデータを視覚的に比較できます。棒の高さや長さを一目で確認できるため、どのカテゴリが最も高いか、どれが低いかがすぐにわかります。これにより、特定の問題点を迅速に特定し、改善策を講じることが可能です。
また、棒グラフはシンプルで視覚的に理解しやすいため、現場のミーティングや報告書にもよく使われます。データの見やすさと伝わりやすさを重視する際に、棒グラフは非常に有効なツールです。
折れ線グラフ
折れ線グラフは、時系列データの変化を視覚的に示すのに適しています。横軸に時間(年、月、日など)を取り、縦軸に数値を配置し、データポイントを線でつなぎます。
折れ線グラフの最大の利点は、データの傾向やパターンを視覚的に把握できることです。例えば、月ごとの売上推移や製品の不良率の変化など、時間の経過に伴うデータの動きを一目で確認できます。データが増加しているのか、減少しているのか、または一定の範囲内で変動しているのかを視覚的に捉えることができるため、今後の予測や対策を考える際に非常に役立ちます。
また、複数のデータセットを同じグラフにプロットすることで、異なる要素の相関関係や比較も簡単に行えます。例えば、売上と広告費の関係を一つの折れ線グラフで示すことで、両者の関連性を確認することができます。
円グラフ
円グラフは、全体に対する各部分の割合を視覚的に示すのに適しています。円全体を100%とし、各部分をセクター(扇形)で表現します。
円グラフの強みは、割合や比率を直感的に理解できる点です。例えば、製品別の売上構成やコストの内訳を示す場合、円グラフを使うと各項目が全体の中でどれくらいの割合を占めているかを一目で把握できます。特に、データの構成比率を視覚的に表現したい場合に有効です。
ただし、円グラフは項目数が多いと見づらくなるため、主要な項目だけを表示するか、データを適切にまとめる工夫が必要です。また、数値の差が小さい場合には、棒グラフや他のグラフの方が適している場合もあります。
帯グラフ
帯グラフは、棒グラフの一種で、特に割合や構成を示す際に使用されます。縦軸または横軸にデータを配置し、各カテゴリを色分けして表示します。
帯グラフの特徴は、データの積み上げや比率を視覚的に表現できる点です。例えば、プロジェクトの進捗状況を示す場合や、売上の内訳を示す場合に有効です。各項目が全体の中でどのくらいの割合を占めているかを一目で把握できるため、構成比を理解するのに適しています。
また、帯グラフは棒グラフと同様に視覚的にわかりやすく、データの比較が容易です。特に、複数のデータセットを並べて比較する場合に有効です。
その他のグラフ
その他のグラフには、レーダーチャートやヒートマップなどがあります。これらは特定の用途に応じて使用され、データの多角的な分析に役立ちます。
レーダーチャートは、複数のデータを一つのグラフで視覚的に比較するのに適しており、各軸にデータを配置し、全体のバランスを確認できます。一方、ヒートマップはデータの濃淡を色で表現し、データの分布や頻度を視覚的に把握するのに役立ちます。
これらのグラフを使いこなすことで、データ分析の幅が広がり、より深い洞察を得ることができます。次のセクションでは、具体的なグラフの作成方法や活用例について詳しく解説していきます。
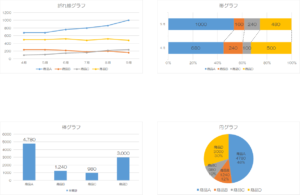
チェックシートで抜け漏れを防ごう!
品質管理の現場では、データの記録や作業の確認を効率的に行うためにチェックシートが非常に役立ちます。ここでは、チェックシートの基本から種類、そして具体的な作り方と使い方について詳しく解説します。
チェックシートとは
チェックシートとは、データを整理して記録するための用紙や表のことです。特定の項目について、データの収集や作業の確認を行う際に使用されます。チェックシートを使うことで、データの抜け漏れを防ぎ、正確な記録を残すことができます。
チェックシートの基本的な構造は、項目名とチェック欄で構成されており、簡単にデータを記録できるようになっています。例えば、製品の検査項目や設備の点検項目などを列挙し、それぞれの項目が完了したかどうかをチェックすることで、作業の進捗や結果を明確に管理できます。これにより、重要な作業の見落としを防ぎ、品質管理の精度を高めることができます。
次に、チェックシートの種類について見ていきましょう。
チェックシートの種類
チェックシートには主に二つの種類があります。それは「点検用チェックシート」と「記録用チェックシート」です。それぞれの特徴と用途について詳しく見ていきましょう。
点検用チェックシートは、特定の作業や点検項目が確実に実施されたかどうかを確認するために使用されます。例えば、機械設備の点検項目をリストアップし、各項目が点検されたかどうかをチェックボックスで確認します。これにより、点検漏れや確認漏れを防ぎ、設備の安全性を確保することができます。
一方、記録用チェックシートは、データの収集や記録を目的としています。例えば、製品の不良数や作業時間を記録する際に使用されます。各項目について日付や数量を記入し、データを体系的に整理することで、後からの分析や報告に役立てることができます。
このように、用途に応じて適切なチェックシートを選ぶことが重要です。次に、チェックシートの具体的な作り方と使い方について説明します。
チェックシートの作り方、使い方
チェックシートを効果的に活用するためには、適切な作り方と使い方を理解することが重要です。以下の4つのステップに従って、チェックシートを作成してみましょう。
まず、チェックシートを作成する目的を明確にします。例えば、製品検査のため、設備点検のため、データ収集のためなど、具体的な目的を設定します。
次に、チェックするべき項目をリストアップします。目的に応じて、必要な項目を漏れなく書き出します。例えば、製品検査の場合は、寸法、色、機能などのチェック項目を設定します。
リストアップした項目を基に、チェックシートのフォーマットを作成します。項目名とチェック欄を適切に配置し、データを記入しやすい形式にします。Excelや専用のソフトウェアを使用すると簡単に作成できます。
作成したチェックシートを現場で使用します。データを記入する際には、正確性と一貫性を保つことが重要です。チェック項目が全て完了したかどうかを確認し、必要に応じて改善点を見つけ出します。
チェックシートは、データの抜け漏れを防ぎ、作業の正確性を高めるための有効なツールです。適切に作成し、活用することで、品質管理の効果を最大限に引き出すことができます。次のセクションでは、パレート図について詳しく解説します。
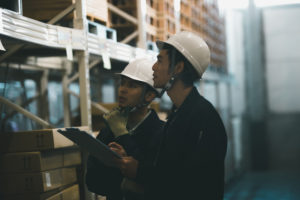
パレート図で重要な問題を特定!
パレート図は、品質管理において重要な問題を特定するための強力なツールです。ここでは、パレート図の基本から作り方、使い方について詳しく解説します。
パレート図とは
パレート図とは、問題の種類ごとにその発生頻度や影響度を視覚的に示すグラフです。イタリアの経済学者ヴィルフレド・パレートが発見した「パレートの法則」(80:20の法則)に基づいています。この法則は、「全体の80%の結果は、20%の原因によって引き起こされる」という考え方です。
パレート図は、縦軸に発生件数や影響度、横軸に問題の種類を配置し、棒グラフで示します。通常、重要度の高い順に左から右に並べ、累積比率も折れ線グラフで示します。これにより、どの問題が全体に大きな影響を与えているのかを一目で確認することができます。
次に、パレート図の具体的な作り方について説明します。
パレート図の作り方
パレート図を作成するのは簡単で、以下のステップに従って進めます。
まず、分析したい問題のデータを収集します。例えば、不良品の種類とその発生件数などを集めます。
次に、収集したデータを問題の種類ごとに分類します。全ての問題をリストアップし、各問題の発生件数や影響度を整理します。
各問題の発生件数や影響度を降順に並べ替えます。重要度の高い問題を左から順に配置します。
各問題の累積比率を計算し、累積パーセントを求めます。これにより、全体に対する各問題の影響度を明確に示すことができます。
最後に、パレート図を作成します。縦軸に発生件数や影響度、横軸に問題の種類を設定し、棒グラフを描きます。さらに、累積比率を折れ線グラフで示します。
これでパレート図が完成です。次に、パレート図の使い方について説明します。
パレート図の使い方
パレート図は、重要な問題を特定し、優先順位をつけるために使用します。以下のように活用することで、効果的に問題解決を進めることができます。
まず、パレート図を作成したら、最も重要な問題を特定します。累積比率の80%に達するまでの問題を優先的に解決することで、効率的に品質改善が可能です。例えば、製造工程における不良品の原因を分析した結果、パレート図で特定の2つの原因が全体の80%を占めていることがわかれば、その2つの問題に焦点を当てて改善策を講じることが重要です。
次に、特定した問題について詳細な分析を行います。問題の根本原因を探り、具体的な対策を検討します。パレート図で特定した問題は、他のQC7つ道具(特性要因図やヒストグラムなど)を使ってさらに深掘りすることができます。
また、パレート図を定期的に更新し、改善の進捗を確認することも重要です。問題が解決されたかどうか、次に取り組むべき問題は何かを継続的にチェックします。これにより、品質改善活動が継続的に行われ、現場の品質向上につながります。
パレート図を活用することで、効率的に重要な問題を特定し、優先順位をつけて対策を講じることができます。次のセクションでは、関係性を視覚化できる散布図について詳しくお話ししていきましょう。
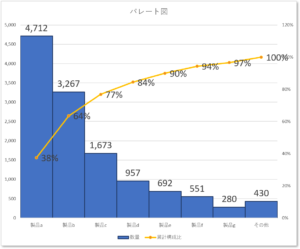
散布図でデータの関係性を視覚化!
散布図は、二つのデータの関係性を視覚的に把握するためのツールです。ここでは、散布図の基本から作り方、見方、使い方について詳しく解説します。
散布図とは
散布図とは、二つの変数の関係性を視覚的に示すグラフです。横軸に一つの変数、縦軸にもう一つの変数を取って、各データポイントを点で示します。このグラフを使うことで、二つの変数間にどのような関係があるかを一目で確認することができます。
散布図の大きな利点は、データの分布や傾向を直感的に把握できる点です。例えば、気温とアイスクリームの売上の関係を散布図で示すと、気温が上がるにつれて売上も増える傾向があることがわかります。これにより、相関関係の有無や強さを判断することができます。
次に、散布図の具体的な作り方について説明します。
散布図の作り方
散布図を作成するのは簡単で、以下のステップに従って進めます。
まず、分析したい二つの変数のデータを収集します。例えば、気温とアイスクリームの売上データなど。
収集したデータを整理し、対応するデータポイントをペアにします。エクセルなどの表計算ソフトを使うと便利です。
散布図を作成するために、横軸に一つの変数、縦軸にもう一つの変数を設定します。各データポイントをプロットし、グラフを描きます。
散布図を見て、データポイントがどのように分布しているかを確認します。点が一直線に近い形で並んでいれば、強い相関関係があることを示します。
これで散布図が完成です。次に、散布図の見方について説明します。
散布図の見方
散布図を見る際には、以下のポイントに注意します。
ポイント1:相関関係の方向
散布図のデータポイントが右上がりであれば、正の相関関係があります。つまり、一つの変数が増えるともう一つの変数も増える関係です。逆に、右下がりの場合は負の相関関係があり、一つの変数が増えるともう一つの変数が減る関係です。
ポイント2:相関の強さ
データポイントが一直線に近い形で並んでいる場合、強い相関関係があります。点がばらついている場合は、相関関係が弱いか、ほとんどないことを示します。
ポイント3:外れ値の確認
散布図を見て、他のデータポイントから大きく離れた点(外れ値)がないか確認します。外れ値はデータの異常値や特異な事例を示すことがあり、分析結果に大きな影響を与える可能性があります。
これらのポイントを押さえることで、散布図から得られる情報を正しく理解できます。次に、散布図の具体的な使い方について説明します。
散布図の使い方
散布図は、二つの変数間の関係を明確にするために使用されます。以下のような場面で活用できます。
場面1:品質と生産条件との関係の調査
まず、品質管理の現場では、製品の品質と製造条件との関係を調査する際に使用されます。例えば、製造温度と製品の硬度の関係を散布図で示すことで、適切な温度条件を見つけることができます。また、営業やマーケティングの分野では、広告費と売上の関係を散布図で分析し、効果的な広告戦略を立てることができます。
場面2:2つのデータの因果関係を見つける
さらに、散布図は科学研究やデータ分析の分野でも広く利用されており、変数間の因果関係や傾向を探るための基本的なツールです。例えば、ある薬剤の投与量と効果の関係を散布図で示すことで、最適な投与量を見つけることができます。
このように、散布図はさまざまな分野で活用でき、データの関係性を視覚的に把握するための強力なツールです。次に、散布図を作成する際のポイントについて説明します。
【注意】散布図を作成する際のポイント
散布図を作成する際には、いくつかのポイントに注意することが重要です。これらのポイントを押さえておくことで、より正確で有用な散布図を作成することができます。
ポイント1:データの正確性の確保
まず、データの収集には正確性が求められます。データの誤りや不正確な記録は、散布図の信頼性を損なう原因となります。データを収集する際には、標準化された手順を守り、全てのデータが一貫した基準で記録されていることを確認しましょう。
ポイント2:軸のスケールを適切に設定
次に、適切なスケールを設定することが重要です。散布図の軸のスケールが不適切であると、データの傾向や相関関係を正しく判断できなくなります。データの範囲に応じて、軸のスケールを適切に調整しましょう。
ポイント3:外れ値に注意して分析する
また、外れ値の影響に注意する必要があります。外れ値はデータの異常値や特異な事例を示すことがあり、分析結果に大きな影響を与える可能性があります。外れ値が存在する場合は、その原因を調査し、適切な処理を行いましょう。
これらのポイントを押さえて散布図を作成することで、データの関係性を正確に把握し、効果的な分析が可能になります。次のセクションでは、特性要因図について詳しく解説します。
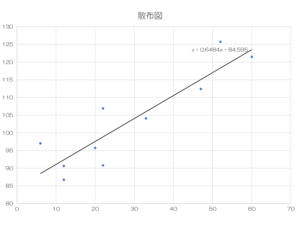
特性要因図で問題の原因を究明!
特性要因図は、問題の原因を系統的に洗い出すための効果的なツールです。ここでは、特性要因図の基本から作り方、使い方について詳しく解説します。
特性要因図とは
特性要因図とは、問題の原因とその影響を視覚的に整理するための図です。別名「魚の骨図」や「イシカワ図」とも呼ばれ、問題の特性(結果)とその要因(原因)を魚の骨のように並べて表現します。この図を使うことで、複数の要因がどのように特性に影響を与えているかを一目で把握することができます。
特性要因図の主な目的は、問題の原因を系統的に分析し、対策を立てるための基礎情報を得ることです。例えば、製品の不良原因を探る際に、特性要因図を使って材料、人、方法、機械などの要因を細かく分類し、具体的な原因を特定します。これにより、問題解決のための具体的なアクションプランを立てることができます。
次に、特性要因図の具体的な作り方について説明します。
特性要因図の作り方
特性要因図を作成するには、以下の4つのステップに従います。
まず、解決したい問題を明確に定義します。例えば、「製品の不良率が高い」といった具体的な問題を設定します。
次に、問題に影響を与えている主な要因を特定します。一般的には「4M」(人、機械、方法、材料)に分類されますが、状況に応じて「5M1E」(環境、測定)なども考慮します。
各主な要因をさらに細分化し、具体的なサブ要因を洗い出します。例えば、「人」の要因を「教育不足」、「疲労」、「ミス」といった具体的な項目に分けます。
中心に問題(特性)を書き、その左右に主な要因を骨のように並べて描きます。各主な要因から枝分かれする形でサブ要因を書き加え、図を完成させます。
このようにして作成した特性要因図を使って、問題の原因を詳細に分析します。次に、特性要因図の使い方について説明します。
特性要因図の使い方
特性要因図は、問題の原因を系統的に整理し、具体的な改善策を立てるために使用します。以下のように活用することで、効果的な問題解決が可能になります。
使い方1:各要因別に対策を検討する
まず、特性要因図を作成したら、各要因を一つずつ検討します。例えば、「製品の不良率が高い」原因として「人」の要因に「教育不足」が挙げられた場合、具体的な教育プログラムの見直しやトレーニングの強化を検討します。また、「機械」の要因に「定期点検不足」が挙げられた場合、点検スケジュールの見直しやメンテナンスの強化を行います。
使い方2:さらなる問題の深堀りを行う
次に、特性要因図をチームで共有し、各メンバーの意見や知識を反映させることで、より多角的な視点から問題の原因を洗い出します。これにより、見落としがちな要因や新たな改善策を発見することができます。特に、現場の作業者からの意見は、実際の作業に即した具体的な原因を特定するのに役立ちます。
使い方3:特性要因図を繰返し実施する
さらに、特性要因図を定期的に見直し、改善の効果を確認します。問題が解決されたかどうかを評価し、必要に応じて新たな要因を特定し、再度対策を講じます。これにより、継続的な品質改善が実現します。
特性要因図は、問題の原因を系統的に整理し、具体的な改善策を立てるための強力なツールです。次のセクションでは、ヒストグラムについて詳しく解説します。
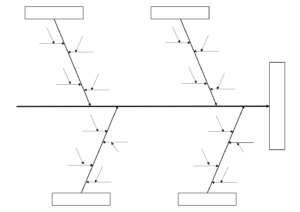
ヒストグラムでデータの分布を把握!
ヒストグラムは、データの分布を視覚的に理解するための基本的なツールです。ここでは、ヒストグラムの基本から作り方、見方、そして応用的な使い方について詳しく解説します。
ヒストグラムとは
ヒストグラムとは、データの分布を棒グラフで示したもので、各棒の高さがデータの頻度を表します。データを一定の範囲ごとに区切り、その範囲に入るデータの数を数えます。これにより、データのばらつきや集中度を一目で確認することができます。
ヒストグラムの主な目的は、データの全体的な分布パターンを把握することです。例えば、製品の寸法測定結果をヒストグラムにすると、どの範囲にデータが集中しているか、ばらつきがあるかを視覚的に確認できます。これにより、工程の安定性や製品の品質を評価することができます。
次に、ヒストグラムに使用される用語について詳しく見ていきましょう。
ヒストグラムに用いられる用語を知ろう
ヒストグラムを理解するためには、いくつかの基本的な用語を知っておく必要があります。
用語 | 説明 |
---|---|
区間(ビン) | データを分類するための範囲。ヒストグラムでは、データをいくつかの区間に分け、それぞれの区間に含まれるデータの数を棒の高さで示します。 |
頻度 | 各区間に含まれるデータの数。ヒストグラムの棒の高さが頻度を表します。 |
階級値 | 各区間の中心値。この値は、各区間の代表値として使用されます。 |
度数分布 | データの分布を区間ごとに示した表。ヒストグラムは、この度数分布を視覚的に表現したものです。 |
これらの用語を理解することで、ヒストグラムを正しく作成し、解釈することができます。次に、ヒストグラムの具体的な作り方について説明します。
ヒストグラムの作り方
ヒストグラムを作成するには、以下のステップに従います。
まず、分析したいデータを収集します。例えば、製品の寸法や重量などの測定データを集めます。
収集したデータを整理し、範囲を確認します。最大値と最小値を特定し、全体の範囲を把握します。
データの範囲をいくつかの区間に分けます。通常、区間数はデータの量に応じて決定します。適切な区間数を設定することで、データの分布を正確に示すことができます。
各区間に含まれるデータの数(頻度)を数えます。これを度数分布表としてまとめます。
縦軸に頻度、横軸に区間を取り、各区間の頻度を棒グラフとして描きます。
これでヒストグラムが完成します。次に、ヒストグラムの見方と使い方について説明します。
ヒストグラムの見方・使い方
ヒストグラムの見方と使い方を理解することで、データの分布を正確に把握し、分析に役立てることができます。
ヒストグラムの見方
まず、ヒストグラムを見る際には、データの分布パターンに注目します。例えば、棒が左右対称に並んでいる場合は、データが正規分布していることを示します。一方、棒が一方に偏っている場合は、偏りがあることを示します。このように、データの形状や分布を確認することで、工程の安定性や異常の有無を判断することができます。
ヒストグラムの使い方1:工程のばらつきを評価
ヒストグラムを使って工程のばらつきを評価します。例えば、製品の寸法が一定の範囲内に収まっているかどうかを確認し、ばらつきが大きい場合は工程の見直しが必要です。また、ヒストグラムを定期的に作成し、データの分布がどのように変化しているかを監視することで、工程の改善効果を確認することもできます。
ヒストグラムの使い方2:他のQC7つ道具と組み合わせる
さらに、ヒストグラムを他のQC7つ道具と組み合わせて使用することで、より深い分析が可能です。例えば、特性要因図を使って問題の原因を特定し、その結果をヒストグラムで確認することで、問題解決の効果を視覚的に評価することができます。
【応用】度数分布表から平均値、標準偏差を求める方法
ヒストグラムの応用として、度数分布表から平均値や標準偏差を求める方法があります。これにより、データの中心傾向やばらつきを定量的に評価することができます。
まず、平均値を求めるためには、各区間の階級値にその区間の頻度を掛けた値を合計し、全データの数で割ります。これにより、データの平均値が算出されます。
次に、標準偏差を求めるためには、各データポイントの値と平均値との差を二乗し、その結果を合計します。その合計をデータの数で割り、平方根を取ることで標準偏差が得られます。標準偏差は、データのばらつきの程度を示す指標であり、ばらつきが大きいほど標準偏差も大きくなります。
このように、度数分布表から平均値や標準偏差を求めることで、データの特徴をより詳細に理解し、工程の改善に役立てることができます。次のセクションでは、管理図について詳しく解説します。
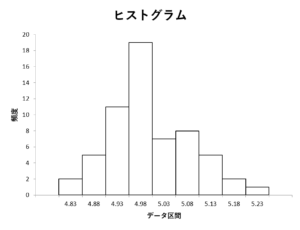
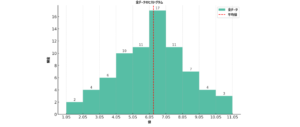
管理図で工程の異常を検知!
管理図は、工程の安定性を監視し、異常を早期に検知するための重要なツールです。ここでは、管理図の基本から種類、作り方、そしてプロの技について詳しく解説します。
管理図とは
管理図とは、工程のデータを時系列で記録し、工程が安定しているかどうかを判断するためのグラフです。縦軸にデータの値、横軸に時間や順序を取ってプロットし、中央線(平均値)と上限・下限管理線(通常の範囲)を引いて表示します。この図を使うことで、データが通常の範囲内にあるか、異常が発生しているかを一目で確認できます。
管理図の主な目的は、工程の安定性を維持し、異常が発生した場合にすぐに対処することです。例えば、製品の寸法や不良品の数などを管理図にプロットすることで、工程が安定しているかどうかを継続的に監視できます。これにより、問題が大きくなる前に迅速に対応できるため、品質管理において非常に有効です。
次に、管理図に使用される用語について詳しく見ていきましょう。
管理図に用いる用語
管理図を理解するためには、いくつかの基本的な用語を知っておく必要があります。
用語 | 説明 |
---|---|
中央線(CL) | データの平均値を示す線。通常の範囲の中心を示します。 |
上限管理線(UCL) | データの上限を示す線。通常の範囲の上限を超えるデータは異常と見なされます。 |
下限管理線(LCL) | データの下限を示す線。通常の範囲の下限を下回るデータは異常と見なされます。 |
サブグループ | データを収集するための小さなグループ。例えば、一日の生産データを複数のサブグループに分けて管理します。 |
点プロット | 各データポイントをプロットする点。これにより、データの変動を視覚的に確認できます。 |
これらの用語を理解することで、管理図を正しく作成し、解釈することができます。次に、管理図の種類について説明します。
管理図の種類
管理図にはいくつかの種類があり、それぞれ異なる目的で使用されます。ここでは、代表的な管理図について紹介します。
Xバー・R管理図
連続データを扱う際に使用される管理図です。Xバーはサブグループの平均値を示し、Rは範囲(最大値と最小値の差)を示します。工程の平均とばらつきを同時に監視することができます。
P管理図
不良品率を監視するための管理図です。各サブグループの不良品率をプロットし、工程の不良率が管理範囲内にあるかを確認します。
C管理図
不良品の数を監視するための管理図です。各サブグループの不良品数をプロットし、工程の不良品数が管理範囲内にあるかを確認します。
X管理図
個々のデータポイントを監視するための管理図です。データの平均値と管理線をプロットし、個別のデータポイントが管理範囲内にあるかを確認します。
これらの管理図を適切に選択し、使用することで、工程の安定性を効果的に監視することができます。次に、計量値の管理図の作り方について説明します。
計量値の管理図の作り方
計量値の管理図を作成するには、以下のステップに従います。
まず、工程から計量データを収集します。例えば、製品の寸法や重量などの測定データを集めます。
収集したデータをサブグループに分けます。通常、一つのサブグループには同じタイミングで収集された複数のデータポイントを含めます。
各サブグループの平均値(Xバー)と範囲(R)を計算します。平均値はサブグループ内のデータの平均を示し、範囲は最大値と最小値の差を示します。
中央線(CL)を全サブグループの平均値の平均として設定します。上限管理線(UCL)と下限管理線(LCL)は、通常、平均値に一定の標準偏差を加減することで設定します。
縦軸に計量値、横軸に時間や順序を取り、各サブグループのデータポイントをプロットします。管理線も同時に描きます。
これで計量値の管理図が完成です。次に、管理図の点の並び方のクセの見方について説明します。
【プロ技】管理図の点の並び方のクセの見方
管理図の点の並び方にはいくつかのパターンがあり、それぞれ異なる工程の状態を示しています。以下のポイントに注意して点の並び方を確認しましょう。
- 連続した点のパターン: 点が連続して上昇または下降している場合、工程に一貫した変動がある可能性があります。これは、システム的な原因による変動を示していることが多いです。
- 中心線からの逸脱: 点が頻繁に中心線から大きく逸脱している場合、工程に特殊原因が存在する可能性があります。これは、突然の異常や問題が発生していることを示します。
- ランダムなパターン: 点がランダムに分布している場合、工程が安定していることを示します。ただし、特定のパターンが見られないことを確認することが重要です。
- 点の集中: 点が特定の範囲に集中している場合、その範囲内での変動が多いことを示します。これは、特定の条件下での工程のばらつきを示していることが多いです。
これらのパターンを見極めることで、工程の状態を正確に把握し、必要な対策を講じることができます。管理図を活用して、工程の安定性を維持し、品質を向上させましょう。次のセクションでは、連関図法について詳しく解説します。
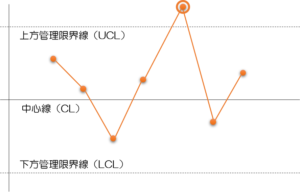
連関図法で因果関係をスッキリ整理!
そして次は新QC7つ道具のツールたちのご紹介です。新QC7つ道具は、従来のQC7つ道具を補完するために開発された手法で、特に言語データの整理や問題解決に役立ちます。ここでは、連関図法、系統図法、マトリックス図法、その他の新QC7つ道具について解説を進めます。
まずは連関図法から。連関図法は、複雑な問題の因果関係を論理的に整理するための強力なツールと成り得ます。ここでは、連関図法の基本から作り方、使い方についてお話を進めましょう。
連関図法とは
連関図法とは、問題の原因と結果を視覚的に整理するための図です。主に、複雑に絡み合った問題の要因を明確にするために使用されます。連関図法は、因果関係を矢印でつなぎ、各要因がどのように影響を及ぼしているかを示します。この図を使うことで、問題の根本原因を特定しやすくなります。
連関図法の目的は、問題を引き起こしている要因を体系的に整理し、具体的な解決策を見つけることです。例えば、生産工程で発生する不良品の原因を連関図法で整理すると、どの要因がどのように影響を及ぼしているかが明確になります。これにより、適切な対策を講じることが可能となります。
次に、連関図の具体的な作り方について説明します。
連関図の作り方
連関図を作成するには、以下のステップに従います。
まず、解決したい問題を明確にします。例えば、「不良品の発生率が高い」といった具体的な問題を設定します。
次に、問題に関連する主要な要因を洗い出します。一般的には「4M」(人、機械、方法、材料)に分類しますが、必要に応じて他の要因も考慮します。
各主要な要因についてさらに詳細なサブ要因を特定します。例えば、「人」の要因に対して「教育不足」や「疲労」といった具体的な項目を挙げます。
因果関係を矢印で示し、各要因がどのように影響し合っているかを図にします。主要な要因からサブ要因への矢印を引き、論理的に関係を示します。
このようにして連関図を作成し、問題の因果関係を明確にします。次に、連関図の具体的な使い方について説明します。
連関図の使い方
連関図は、問題の原因を詳細に分析し、効果的な対策を講じるために使用します。以下のように活用することで、問題解決に役立てることができます。
使い方1:連関図で各要因の影響度を評価する
まず、連関図を作成したら、各要因の影響度を評価します。重要な要因には、重点的に対策を講じる必要があります。例えば、不良品の発生率を減少させるために、「教育不足」が大きな要因であると特定された場合、従業員の教育プログラムを強化します。また、「機械のメンテナンス不足」が原因の場合は、定期的なメンテナンススケジュールを見直すことが必要です。
使い方2:連関図をチームで共有する
次に、連関図をチームで共有し、各メンバーの意見や知識を反映させます。これにより、多角的な視点から問題の原因を洗い出し、見落としがちな要因や新たな改善策を発見することができます。特に、現場の作業者からの意見は、実際の作業に即した具体的な原因を特定するのに役立ちます。
使い方3:連関図を定期的に見直しする
さらに、連関図を定期的に見直し、改善の効果を確認します。問題が解決されたかどうかを評価し、必要に応じて新たな要因を特定し、再度対策を講じます。これにより、継続的な品質改善が実現します。
連関図は、複雑な問題の因果関係を明確にし、具体的な改善策を立てるための強力なツールです。次のセクションでは、系統図法について詳しく解説します。
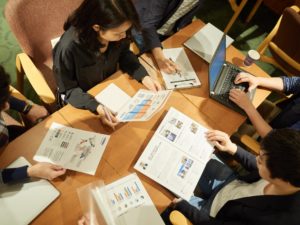
系統図法で問題を構造的に把握!
系統図法は、目標を達成するための手段を系統的に整理し、問題を構造的に把握するためのツールです。ここでは、系統図法の基本から作り方、使い方について詳しく解説します。
系統図法とは
系統図法とは、問題を解決するための手段や行動をツリー状に整理する方法です。系統的に整理することで、目標達成に必要な具体的なステップを明確にすることができます。例えば、新しい製品の開発プロジェクトにおいて、各工程の手順を詳細に示すために使用されます。
系統図法の主な目的は、複雑なプロジェクトや問題を分解し、具体的な行動計画を立てることです。これにより、各ステップの関係性や順序が明確になり、効率的にプロジェクトを進行することができます。また、全体像を視覚的に把握することで、抜け漏れのない計画を立てることができます。
次に、系統図の具体的な作り方について説明します。
系統図の作り方
系統図を作成するには、以下のステップに従います。
まず、達成したい目標を明確に定義します。例えば、「製品開発プロジェクトの成功」といった具体的な目標を設定します。
次に、目標を達成するための主要な手段や行動を洗い出します。これらの手段は、目標を実現するために必要な大きなステップとなります。
各主要な手段について、さらに具体的なサブ手段を特定します。例えば、「市場調査」という主要な手段に対して、「競合分析」、「顧客インタビュー」といった具体的なサブ手段を挙げます。
中心に目標を置き、その下に主要な手段をツリー状に並べて描きます。各主要な手段からさらにサブ手段を枝分かれさせ、図を完成させます。
このようにして作成した系統図を使って、目標達成のための具体的な計画を立てます。次に、系統図の具体的な使い方について説明します。
系統図の使い方
系統図は、目標達成のための具体的な行動計画を立てるために使用します。以下のように活用することで、効率的な問題解決やプロジェクト管理が可能になります。
使い方1:手段と行動の関係性を確認する
まず、系統図を作成したら、各手段や行動の関係性を確認します。例えば、新製品開発プロジェクトにおいて、「市場調査」が「製品設計」にどのように影響するかを視覚的に把握します。これにより、各ステップの優先順位を決定し、効果的なリソース配分が可能となります。
使い方2:系統図をチームで共有する
次に、系統図をチームで共有し、各メンバーの役割を明確にします。チーム全体で目標と計画を共有することで、一体感を持ってプロジェクトに取り組むことができます。また、系統図を用いて定期的に進捗状況を確認し、必要に応じて計画を修正することで、プロジェクトの成功率を高めることができます。
使い方3:問題解決のための検討ツールとして活用する
さらに、系統図は問題解決のための検討ツールとしても活用できます。例えば、製造工程での不具合が発生した場合、系統図を使って原因を分解し、具体的な対策を策定します。これにより、問題の根本原因を明確にし、効果的な改善策を講じることができます。
系統図法は、複雑な問題やプロジェクトを構造的に整理し、具体的な行動計画を立てるための強力なツールです。これを活用することで、目標達成に向けた効率的な進行が可能になります。次のセクションでは、マトリックス図法について詳しく解説します。
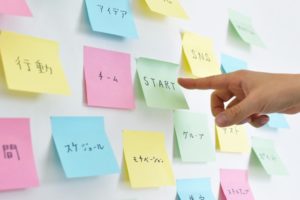
マトリックス図法で複数の要素を分析!
マトリックス図法は、複数の要素を整理し、それらの関係性や重要性を分析するためのツールです。ここでは、マトリックス図法の基本から方策の評価と役割分担、テーマ選定について詳しく解説します。
マトリックス図法とは
マトリックス図法とは、行と列に要素を配置し、それらの交点に関係性や重要度を示す図です。マトリックス図を用いることで、複雑な要素の組み合わせを整理し、全体の関係性を視覚的に把握することができます。例えば、新製品の開発プロジェクトで、各部門の役割やリソース配分を整理する際に使用されます。
マトリックス図法の主な目的は、要素間の関連性を明確にし、効率的な意思決定を支援することです。これにより、プロジェクトの進行がスムーズになり、各要素がどのように相互作用しているかを一目で理解することができます。
次に、マトリックス図による方策の評価と役割分担について説明します。
マトリックス図による方策の評価と役割分担
マトリックス図は、各要素の関連性を評価し、適切な役割分担を決定するために使用します。以下のステップで進めます。
まず、評価したい要素をリストアップします。例えば、新製品開発に関わる部門やタスクを洗い出します。
リストアップした要素を行と列に配置します。例えば、行に部門名、列にタスクを配置します。
各交点に関係性や重要度を記入します。例えば、「高」、「中」、「低」などの評価を行います。また、具体的な数値や記号を用いて詳細に示すこともできます。
関係性の評価に基づいて、各部門の役割分担を決定します。例えば、重要度が高いタスクについては、リソースを集中させるなどの対応を行います。
これにより、プロジェクトの各要素がどのように関連し合っているかを明確にし、効率的な役割分担を実現します。次に、マトリックス図によるテーマ選定について説明します。
マトリックス図によるテーマ選定
マトリックス図は、複数のテーマを評価し、優先順位をつけるためにも使用されます。以下のステップで進めます。
まず、評価したいテーマをリストアップします。例えば、プロジェクトの課題や改善点などを洗い出します。
各テーマを評価する基準を設定します。例えば、「重要性」、「緊急性」、「実現可能性」などの基準を設けます。
各テーマを行に、評価基準を列に配置し、マトリックス図を作成します。各交点に評価結果を記入します。
マトリックス図の評価結果に基づいて、優先順位をつけます。例えば、総合評価が高いテーマを優先的に取り組む対象として選定します。
これにより、複数のテーマを効率的に評価し、効果的な問題解決や改善活動を進めることができます。マトリックス図法を活用することで、複雑な要素を整理し、最適な意思決定を支援することが可能です。次のセクションでは、その他の新QC7つ道具について詳しく解説します。
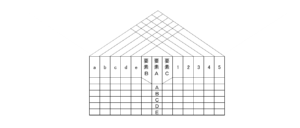
その他の新QC7つ道具
その他の新QC7つ道具として、親和図法、アローダイヤグラム法、PDPC法、マトリックスデータ解析法の4つがあります。これらについても簡単に解説をしておきましょう。
親和図法
親和図法は、複雑な情報を整理し、関連性のある要素をグループ化するための手法です。この方法を使うことで、多くの情報を視覚的に整理し、全体像を把握しやすくなります。
親和図法の主な目的は、情報を整理して問題の本質を明確にすることです。例えば、チームでブレインストーミングを行った後、多くのアイデアを親和図法を使ってグループ化します。各アイデアをカードに書き出し、類似したものをまとめていきます。この過程で、共通のテーマや問題点が浮かび上がり、どこに注力すべきかが明確になります。
親和図法は、特に多くの意見や情報が混在する場面で有効です。チーム全体でアイデアを共有し、視覚的に整理することで、次のステップに進むための基盤を作ることができます。
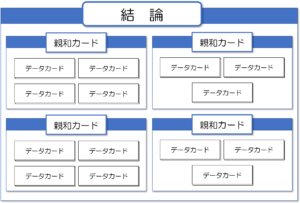
アローダイヤグラム法
アローダイヤグラム法は、プロジェクトの計画や管理を行う際に使用される手法で、タスクの順序と依存関係を視覚的に示します。この方法を使うことで、プロジェクトの全体像と各タスクの関係性を把握しやすくなります。
アローダイヤグラム法の主な目的は、プロジェクトのスケジュールを効率的に管理し、重要なタスクの順序を明確にすることです。例えば、新製品の開発プロジェクトにおいて、各タスクを矢印でつなぎ、どのタスクが他のタスクに依存しているかを示します。これにより、クリティカルパス(最も時間がかかるタスクの連鎖)を特定し、遅延を防ぐための対策を講じることができます。
アローダイヤグラム法は、プロジェクト管理において非常に有効であり、効率的なスケジュール管理とリソース配分を実現します。
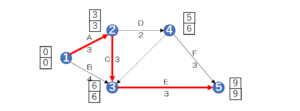
PDPC法
PDPC法(Process Decision Program Chart)は、計画の潜在的な問題を予測し、対策を立てるための手法です。この方法を使うことで、計画の実行中に発生する可能性のある問題を事前に把握し、対応策を準備することができます。
PDPC法の主な目的は、計画のリスクを最小限に抑え、成功率を高めることです。例えば、新しいシステムの導入計画において、各ステップごとに考えられる問題を洗い出し、それぞれの問題に対する解決策を示します。この過程で、計画の弱点を事前に補強し、スムーズな実行を可能にします。
PDPC法は、特に複雑なプロジェクトやリスクが高い計画において有効であり、事前に問題を予測して対策を講じることで、計画の成功率を大幅に向上させます。
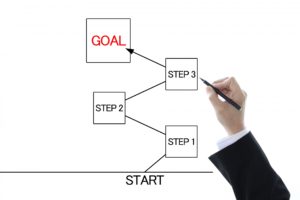
マトリックスデータ解析法
マトリックスデータ解析法は、複数の要因が相互にどのように影響し合うかを分析する手法です。この方法を使うことで、データの相関関係を明確にし、効果的な対策を立てることができます。
マトリックスデータ解析法の主な目的は、データの中に潜むパターンや関係性を見つけ出し、意思決定に役立てることです。例えば、製品の品質に影響を与える複数の要因を分析し、どの要因が最も重要であるかを特定します。これにより、最も効果的な改善策を見つけ出し、品質向上に繋げることができます。
マトリックスデータ解析法は、データ分析の基本であり、複雑な問題を解決するための強力なツールです。これを活用することで、データに基づいた効果的な意思決定が可能になります。
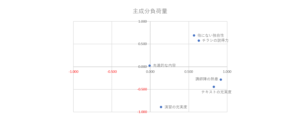
まとめ:QC7つ道具・QC7つ道具とは?わかりやすく解説
品質管理の現場で成果を上げるためには、適切なツールを使いこなすことが重要です。QC7つ道具と新QC7つ道具は、そのために欠かせない強力なツールです。これらの道具を使えば、データの整理、問題の原因分析、工程の安定化など、あらゆる品質管理の課題に対応することができるようになります。
まずは、基本のQC7つ道具から始めてみることをオススメします。パレート図を使えば、どの問題が最も重要かを簡単に特定できますし、特性要因図で問題の根本原因を洗い出しして具体的な改善策を見つけ出すことができます。そしてヒストグラムを使えば、データの分布が一目でわかり、工程のばらつきを可視化できるとともに、散布図で二つの変数の関係性を視覚化して相関関係を明確にできます。さらにチェックシートでデータの収集と確認作業を効率化し、管理図で工程の異常を早期に検知して、グラフを使ってデータを視覚的に表現することができたなら、もう現場の品質状況は手に取るように、だれでもわかるようになるはずです。おわかりですよね。
そして新QC7つ道具も有用です。親和図法で情報を整理し、問題の本質を明らかにします。アローダイヤグラム法でプロジェクトのスケジュールを管理し、効率的な進行を実現します。PDPC法を使えば、計画の潜在的な問題を事前に予測し、対応策を準備することができます。マトリックスデータ解析法で複数の要素を分析し、最も効果的な改善策を見つけ出すことが可能になれば、我が社の品質管理は高いレベルと言えるでしょう。
どうでしょうか?今すぐQC7つ道具を使いこなしてみませんか?データを収集し、適切なツールを選んで問題を解決することで、現場の品質を大幅に向上させることができます。つまり品質管理の改善は、この情報を目にしているあなたの手の中にあるというわけです。
ぜひQC7つ道具を使いこなして、現場の課題に立ち向かいましょう。これらの道具を使うことで、あなたの仕事がより効率的で成果の上がることを実感できるはずです。今日から早速、QC7つ道具を活用して、現場の品質改善に取り組んでみてください。
もし、確認したいことがあれば以下まで気軽にZOOMでの無料相談をお申込みいただければと思います。
滋賀県よろず支援拠点> https://www.shigaplaza.or.jp/yorozu/contact
※ 西本を指名すれば、全国どこからでも申込み可能です。
それでは今日はここまでです。今後とも宜しくお付き合い下さい☆
長文乱文を最後まで読んでくださりいつもありがとうございます♪
すべては御社の発展のために、すべてはあなたの笑顔のために