暗黙知を形式知へと変換する要素技術
IoTというバズワードがあるけれど
その実態ってよくわりませんよね
そこで業務改善手法であるIE手法を
話し言葉で解説するこのサイトが
製造業で展開されているIoT改善を
事例として紹介するシリーズを展開
今回は最後となる事例でありながら
もっともスタンダードな見える化を
進めた事例を紹介します
この会社はどのように導入を進めたか
どんなメリットを生み出したのか
早速、お話していきたいと思います
IoT改善事例⑳の企業概要
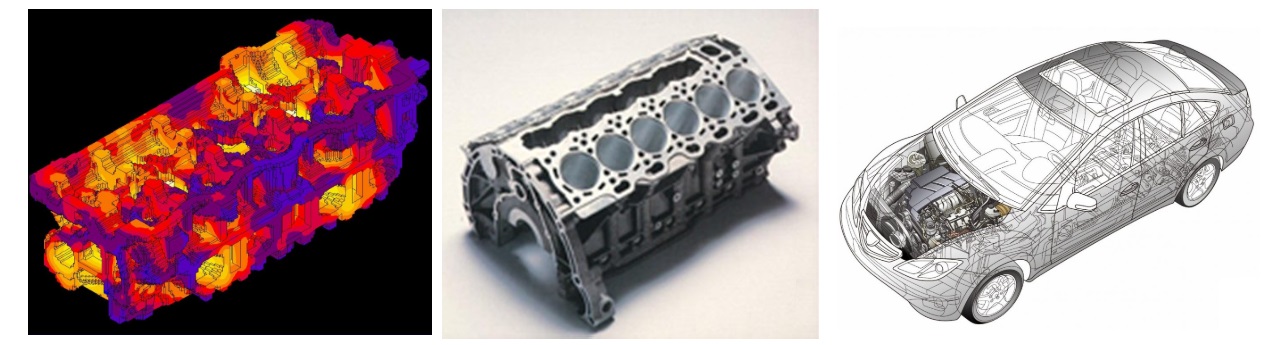
IoT改善事例⑳の改善企業の取り扱い商品イメージ
資本金:4000万円
従業員:108名
設立年:1934年(83年間)
事業概要:自動車エンジン、トランスミッション、鋳造金型設計製作、および受託解析
当社は創業から83年の老舗企業です
主に自動車アルミ部品の加工に用いる
金型を生産する製造業です
たとえばエンジンを構成する主要部品
シリンダーヘッド,ケースハウジング,
シリンダーブロック,バルブボディ等
エンジン・駆動系部品を生産する時の
金型をつくっています
ほとんどの受注は大手自動車メーカや
サプライヤーから直接注文が来ていて
自動車業界内での同金型のシェアは
国内最大規模を誇るほどです
また、当社の特徴は
金型設計時のデータ解析にも積極的で
3次元やCAMの組み合わせはもちろん
CADデータの制作・蓄積・再活用
さらにシミュレーションツールなど
ITツールの活用にも積極的に
取り組んできたところです
そんな当社が抱えていた課題は
職人気質な業界の壁でした
当社が抱えていた課題
当社では現場改善を進めることで
徹底的に効率的な金型製作職場を
実現することに注力してきました
その取り組みのひとつとしてこれまで
トヨタ生産方式の標準3票のひとつ
『標準作業組合せ表』を活用するなど
積極的に作業のムダの見える化を
進めてきたのです
ですが当社のメイン主事業である
金型製作の現場では一般的に
製造スキルが属人化する構造があり
個人の作業のムダを見つけたり
製造技術を伝承することが難しく
なかなか対処できてませんでした
それをIoT技術を応用することで
解決へと進むきっかけがあったのです
IoT改善の経緯
ある時当社の社長が
他の中小製造企業が自ら組み上げた
設備の稼働時間を見える化を実現する
IoTの仕組みを見学する機会が
あったそうな
その仕組みはさすが製造業のシステムで
使い勝手が良く、必要な機能だけの
簡単でシンプルな仕組みだったそうな
それを見た社長は
『その仕組みを活用できないか』と
各工程の作業時間に見える化を
検討しはじめたわけです
他社の良いところは素直に学ぶ
そして謙虚にマネをさせていただく
すべての道の鉄則ですよね
設備の稼動状況を見える化を実現するシンプルなIoTツール
まず社長が見学させてもらった
中小製造企業が開発したシステム
それは生産設備の種類にかかわらず
信号灯さえあれば簡単に設置できて
設備の稼動状況をデータとして
描く時できる仕組みでした
具体的には、生産設備の信号灯に
光センサを取り付けて
稼働中や停止中等の状況をデータ獲得
そして無線を通じて社内サーバで処理
結果、生産設備の稼動状況を
管理用PCで見える化するシステムです
なおRaspberry Piという安価なPCを
応用したシンプルな構成であるため
導入費用は機器の購入費用と
センサ設置などの工事費用のみで
規模の小さな企業でも導入できます
そこで当社では上記の仕組みをもって
管理者が設備の稼動状況を常に監視し
各工程の作業時間を整理するなどして
作業者に適切な指示を遅れるように
管理体制を整備することにしました
シンプルなIoTツール活用によるメリット
それでは改めて今回の改善事例として
シンプルなIoT導入によるメリットを
整理していきましょう
メリット2:少量多品種生産の現場把握に役立つ
メリット3:シンプルだから使える仕組み
それではこれらの成果・メリットに
もう少し詳しい解説を加えます
メリット1:簡単に稼動状況が分かる
このIoT導入の1つ目のメリットは
生産設備のメーカーや種類を問わず
信号灯さえあれば簡単に設置できて
設備の稼動状況を見える化できること
やはり生産状況が見えるということは
問題を察知しやすい環境をつくるので
工程改善に結びつきますよね
まずはこれが1つ目です
メリット2:少量多品種生産の現場把握に役立つ
2つ目のメリットは中小にあり勝ちな
少量多品種生産の現場の作業工程は
そのプロセスや制約条件が複雑であり
管理者がその状況を迅速かつ詳細に
把握するのが難しい一面があります
それがこの仕組みを活用することで
管理者が作業状況を把握できるため
適切な指示を打ち出すことが可能で
生産効率が飛躍的に向上します
そりゃ目をつぶって歩くのと
しっかり見て歩くのとでは
精度が格段に変わりますよね!
メリット3:シンプルだから使える仕組み
最後のメリットは中小製造業が実際に
開発・導入したツールであるために
必要な不可欠な機能だけに絞られてて
単純な仕組みなので取り扱い易いです
つまり必要なミニマム機能のみなので
使い勝手が良く、現場の中で有効に
理解・活用しやすいことです
複雑なシステムは理解する人が少なく
結局使われなくなります
わかりやすいことはいいことなんです
IoT改善事例⑳シンプルなIoTツールで設備の稼動状況を見える化
ものづくり企業発のIoTツールを活用し
生産設備の稼動状況を取得していく
取得データにより現場作業を可視化し
工程改善の際の気づきにつなげる
そんなIoT改善事例の紹介でした
皆さまの設備稼働率はいくらですか?
それはどんな時悪化して
どんな時に良いのでしょうか?
これがリアルタイムで確認できる
それもちょっとしたきっかけと
少しの費用負担で
あなたの職場ももうそろそろ
取り組まなければ間に合わなく
なってしまうかもしれません
ぜひ、お気軽にご相談を!
それでは今日はここまで
今後とも宜しくお付き合いください☆
長文・乱文を最後まで読んでくださり
いつもありがとうございます♪
すべては御社の発展のために
すべてはあなたの笑顔のために