皆さんの職場では、不良品を減らしたり、作業をもっとスムーズにしたりするために、何か工夫をしていますでしょうか?
毎日同じ作業を繰り返していると、「あれ?なんかいつもと違うぞ?」「この作業、ちょっとムダが多い気がする…」なんて思うことがあると思います。実は、そんな「気づき」を活かして、問題を解決し、もっとムダなのない、品質の高める製品づくりを進めるスゴ技があります。
それが、QC七つ道具×層別です。
QC七つ道具は、データを分かりやすく整理・分析するための7つのツール。層別は、データをグループ分けして、それぞれの違いを見つけるテクニックです。
この二つを組み合わせることで、今まで見えなかった問題点を見つけ、改善につなげることができます。
そこで今回は、QC七つ道具と層別の基本、現場での具体的な活用方法、さらにはあなたの職場でのQC七つ道具×層別活用のためのポイントまで、わかりやすく解説していきます。
ぜひ今回も読み終えるまでのお時間、しばらくお付き合いくがさいませ。
QC七つ道具とは?
QC七つ道具というキーワードはよく聞くかとは思いますが、それがどんな道具なのか?全部すべて頭に浮かばないヒトもいらっしゃるかもしれません。そのため、品質管理の重要性から簡単に基礎知識をおさらいしてから本題にはいりましょう。
製造現場における品質管理の重要性
皆さんの職場では、毎日たくさんの製品を作っていると思います。
でもその製品の「品質」ってよく聞く言葉ですが、実際にはどんなことを指すのでしょうか?
簡単に言うと、「お客様に満足してもらえる価値」 のことです。我々はそれらを載せた製品を作っています。
例えると…
- 壊れにくい製品
- 性能が良い製品
- 安全な製品
- デザインが良い製品
などなど…
品質が良い製品を作ることで、お客様に喜んでもらうだけでなく、会社の評判も上がり、業績アップにもつながります。
品質管理は、まさに 「会社を支える柱」 と言っても過言ではありません!
QC七つ道具の概要をわかりやすく解説
では、そんな品質管理を進めるにはどうすれば良いのでしょうか?
そこで登場するのが 「QC七つ道具」 です!
QC七つ道具とは、品質管理のために開発された、7つの分析ツールのこと。
まるで、昔の武士が戦場で使う刀や弓矢のように、製造現場で働く私たちにとって、品質向上のための頼もしい武器となります。
QC七つ道具には、以下のようなものがあります。
グラフ: データを視覚的に分かりやすく表示するツール
チェックシート: データを効率的に集めるための表
パレート図: 問題点を重要度順に並べた棒グラフ
特性要因図: 問題の原因を魚の骨のように整理した図
散布図: 2つのデータの関係性を調べるグラフ
ヒストグラム: データの分布を棒グラフで表したもの
管理図: 工程の異常を監視するためのグラフ
これらのツールを使うことで、
- 問題点を発見すること
- 原因を分析すること
- 改善策を考えること
の3つの問題解決プロセスを効率的に進めることができるようになります。
そんなツールがあるなら、使わない手はありませんよね!

現場作業者とリーダーにとってのメリット
QC七つ道具は、問題を解決したい方々にとって、たくさんのメリットをもたらします。
作業者にとってのメリット
- 作業のムダを減らせる!
- ミスを減らして、品質向上!
- 作業がスムーズになって、残業削減!
- 自分の仕事に自信が持てる!
現場のリーダーにとってのメリット
- 部下の指導がしやすい!
- 問題解決がスムーズに!
- チーム全体のレベルアップ!
- より良い職場環境を作れる!
QC七つ道具は、難しい知識や経験がなくても、慣れれば誰でも簡単に使うことができます。
だからあなたもQC七つ道具をマスターして、ぜひ品質管理のプロを目指してもらいたいですね!
QC七つ道具×層別で何がわかる?
ではそのQC七つ道具と「層別」という手法を組み合わせることで、いったいなにがどう変わるのでしょうか?その説明の前にまず「層別」について改めて解説を進めてまいります。
層別とは?基本的な考え方と手順を解説
「層別」って漢字で表現すると、ちょっと難しそうに思うかもしれませんが、実はすごくシンプルな考え方なんです。
層別とは、データをある共通点に基づいて、いくつかのグループに分けること を言います。
例えば、
- みかんを「大きさ」で層別すると…
- 小さいみかん、中くらいのみかん、大きなみかん
- 工場で作られた製品を「製造日」で層別すると…
- 月曜日に作られた製品、火曜日に作られた製品、…
- ある製品の不良品を「不良の種類」で層別すると…
- キズがある不良品、寸法がおかしい不良品、色が違う不良品…
のように、色々な分け方ができます。
層別は、データを分析する上で、とても重要な役割を果たします。
それはデータ全体をただ漠然と見るのではなく、層別してグループ分けすることで、それぞれのグループの特徴や違いがハッキリと見えてくるからです。
層別の手順は以下の通りです。
- 層別する目的を決める: 何のために層別するのか?
- 層別する項目を選ぶ: どの項目でグループ分けするか?
- データを収集する: 各グループのデータを集める
- データを分析する: 各グループの特徴や違いを分析する
この手順を進めることで、ただ並べるだけではわからなかったことが、わかるようになるから凄くパワフルな方法なんです。え?どんなことかって?それではさらに説明を重ねてみたいと思います。
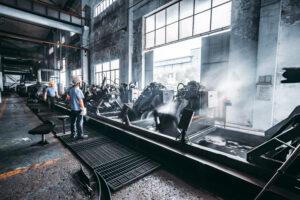
QC七つ道具と層別の組み合わせで生まれる相乗効果
QC七つ道具を単体で使っても、データを分析するための便利なツールです。ですが、層別と組み合わせることで、さらに強力なツールへと進化します。
層別によってデータをグループ分けすることで、QC七つ道具による分析結果がより深く、より具体的になるからです。
例えば、パレート図で不良品の種類を分析した結果、傷が多いことがわかったとします。
ここで、さらに「製造日」で層別してみると「月曜日に作られた製品に傷が多い」という新たな発見があるかもしれませんし、「機械」で層別してみると「機械Bで作られた製品に傷が多い」ということがわかったりします。そうなると、当てずっぽうで要因を探り当てるより、数段早く問題解決に結びつきますよね!
このように、QC七つ道具と層別を組み合わせることで、隠れた問題を発見し、より効果的な改善活動を行うことができるようになります。
隠れた問題を発見する具体的な事例
ではもう少し踏み込んで、いったいどのような具体的な事例があるのか、解説を進めていきましょう。
事例1:不良品の発生原因を特定
ある工場で、製品の不良品率が高いという問題が発生しました。
そこで、パレート図を作成して不良品の種類を分析した結果、寸法不良が最も多いことがわかりました。
さらに、「製造ライン」で層別して分析したところ、Aラインで製造された製品に寸法不良が多いことが判明しました。
なのでAラインの機械に異常がないか点検した結果、設定ミスが見つかり、それを修正することで不良品率を大幅に削減することができました。
事例2:作業時間のバラつきを改善
ある工程で、作業時間の長さにバラつきがあることが問題となっていました。
そこで、ヒストグラムで作業時間を分析した結果、作業時間が10分〜20分の間に集中しているものの、30分以上かかる作業者もいることがわかりました。
「作業者の勤務年数」で層別して分析した結果、ベテラン作業者は15分程度で作業を終えているのに対し、新人作業者は30分以上かかっていることが判明しました。
そこで今回は新人作業者への指導を強化することで、作業時間のバラつきを減らし、全体の作業効率を向上させることができました。
事例3:顧客満足度向上
ある会社で、顧客満足度アンケートを実施した結果、製品の使い方がわかりにくいという意見が多く寄せられました。
そこで、特性要因図を作成して原因を分析した結果、「説明書の内容」と「サポート体制」に問題があることがわかりました。
さらに、「顧客の年齢層」で層別して分析した結果、高齢の顧客からは説明書の内容がわかりにくいという意見が多く、若い顧客からはサポート体制が不十分という意見が多いことが判明しました。
そのため、高齢者向けにはよりわかりやすい説明書を作成し、若い顧客向けには、オンラインサポートを充実させることで、顧客満足度を向上させることができました。
こういうことに気づくのと、気づかないのとでは、まったく品質の改善スピードが変わってくるはずです。これを味方につけたい、というのが今回の主旨です。
QC七つ道具別 層別の活用方法
ではいよいよ、QC七つ道具と層別を組み合わせた、具体的な活用方法を見ていきましょう!
それぞれのツールと層別の組み合わせが、現場でどのように役立つのか、具体的な例を交えながら解説していきます。
グラフ×層別:視覚的な分析で理解を深める
グラフは、データを視覚的に表現することで、データの傾向や変化を捉えやすくするツールです。
層別と組み合わせることで、さらに深い分析が可能になります。
グラフ×層別の例

ある製品の不良品数を、製造日ごとに折れ線グラフで表したとします。
このグラフを、さらに「製造ライン」毎に層別してみると、特定のラインで不良品が多い日が集中していることが発見できるかもしれません。
このように、層別によって隠れたパターンを発見し、問題解決に役立てることができます。
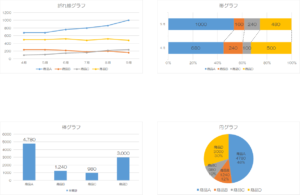
チェックシート×層別:データ収集の精度向上
チェックシートは、データを効率的に収集するためのツールです。
層別と組み合わせることで、データの偏りを防ぎ、より正確な分析を行うことができます。
チェックシート×層別の例:

ある工程の作業ミスを記録するチェックシートを作成するとします。
この際、作業者を層別して記録することで、特定の作業者にミスが集中しているかどうかを分析することができます。
もし特定の作業者にミスが集中している場合は、その作業者に対する教育やサポート体制を見直す必要があるかもしれません。
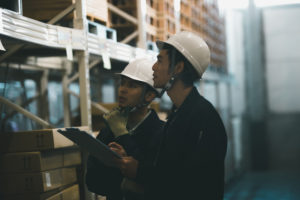
パレート図×層別:真の原因を突き止める
パレート図は、問題の発生頻度を大きい順に並べた棒グラフで、どの問題に優先的に取り組むべきかを判断するのに役立ちます。
層別と組み合わせることで、問題の真の原因を突き止めることができます。
パレート図×層別の例:

顧客からのクレームをパレート図で分析した結果、「製品の不具合」に関するクレームが最も多いことがわかったとします。
さらに、「製品の種類」で層別してみると、特定の製品に不具合が集中していることがわかるかもしれません。
この場合は、その製品の設計や製造工程に問題がある可能性が高いと考えられます。
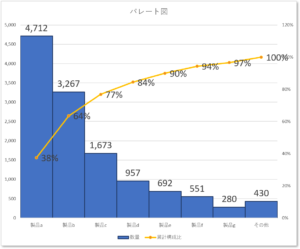
特性要因図×層別:複雑な問題を紐解く
特性要因図は、ある問題の原因を、「魚の骨」のような形で整理して、複雑な問題の要因を漏れなくダブリなく網羅して見える化するためのツールです。そのことにより特性に影響が大きい重要要因を絞り込むことができます。
層別と組み合わせることで、さらに特定の状況下における影響度の高い要因を特定することができます。
特性要因図×層別の例:

ある製品の傷が多く発生しているという問題があったとします。
この問題に対して、特性要因図を作成し、カテゴリに機械A、機械Bなどと機械別に層別して分析を行ったとします。
その結果、機械Aでは「材料の品質」と「作業環境」が、機械Bでは「機械の設定ミス」など、機械毎の特性にフォーカスした傷の発生要因を洗い出せるかもしません。
このように、特性要因図と層別を組み合わせることで、複雑な問題の中から、より具体的な状況における真の原因を特定し、効果的な対策を立てることができるようになります。
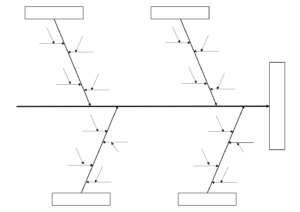
散布図×層別:相関関係を見抜く
散布図は、2つのデータの関係性を調べるためのツールです。
層別と組み合わせることで、隠れた相関関係を発見することができます。
散布図×層別の例:

製品の強度と温度の関係を散布図で表したとします。
さらに、「材料の種類」で層別してみると、特定の材料を使った製品では、温度と強度の間に強い相関関係があることがわかるかもしれません。
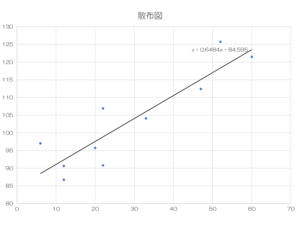
ヒストグラム×層別:データのばらつきを分析
ヒストグラムは、データの分布を視覚的に表すことで、データのばらつき具合を把握するためのツールです。
層別と組み合わせることで、異常値やばらつきの原因を特定することができます。
ヒストグラム×層別の例:

製品の重量をヒストグラムで表したとします。
さらに、「製造日」で層別してみると、特定の日に製造された製品の重量にばらつきが大きいことが発見できるかもしれません。
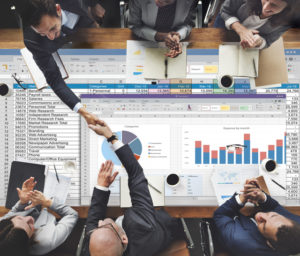
管理図×層別:工程の異常を早期発見
管理図は、工程が安定しているかどうかを監視するためのツールです。
層別と組み合わせることで、工程の異常を早期に発見することができます。
管理図×層別の例:

ある工程の温度を管理図で監視しているとします。
さらに、「作業者」で層別してみると、特定の作業者が担当する工程で温度が不安定になっていることが発見できるかもしれません。
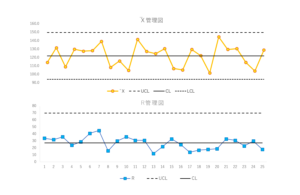
層別を効果的に活用するためのポイント
層別は、データを分析し、問題解決に役立てるための強力なツールですが、効果的に活用するためにはいくつかのポイントを押さえておく必要があります。
ここでは、層別を成功させるための3つのポイントを紹介します。
ポイント1:層別する項目の選び方
層別を行う際に最も重要なのは、「どの項目で層別するか」ということです。
層別する項目によって、分析結果が大きく変わってくるからです。
適切な項目を選ぶためには、以下の点に注意しましょう。
- 目的を明確にする: 何のために層別するのか?目的によって適切な項目は異なります。
- データの特性を理解する: データの種類や性質を理解し、それに合った項目を選びましょう。
- 関係がありそうな項目を選ぶ: 問題と関係がありそうな項目を選び、層別することで新たな発見が得られる可能性があります。
- 過去の経験や知識を活用する: 過去の経験や知識から、層別する項目のヒントが得られる場合があります。
- 複数項目での層別を試みる: 1つの項目だけでなく、複数の項目で層別を試みることで、より深い分析ができる場合があります。
ポイント2:データの収集方法と注意点
層別を行うためには、それぞれのグループに分けられるだけの十分な量のデータが必要です。
データ収集の際には、以下の点に注意しましょう。
- 正確なデータを集める: データの正確性は、分析結果の信頼性に直結します。
- 偏りのないデータを集める: 特定のグループに偏ったデータを集めてしまうと、分析結果が歪んでしまう可能性があります。
- 効率的な収集方法: チェックシートなどを活用し、効率的にデータ収集を行いましょう。
- データの記録方法: データを記録する際には、5W1H (いつ、どこで、誰が、何を、なぜ、どのように) を明確に記録しましょう。
ポイント3:分析結果の解釈と活用方法
層別とQC七つ道具を用いて分析した結果を、どのように解釈し、活用するかが重要です。
分析結果を解釈する際には、以下の点に注意しましょう。
- 各グループの特徴を把握する: 各グループの平均値、ばらつき、分布などを比較し、特徴を把握しましょう。
- グループ間の違いを分析する: グループ間の違いを分析することで、問題の原因や改善のヒントが見えてきます。
- グラフなどを活用して視覚化する: グラフなどを活用することで、分析結果をよりわかりやすく理解することができます。
分析結果を活かすには、以下の点に注意しましょう。
- 改善策を検討する: 分析結果に基づいて、具体的な改善策を検討しましょう。
- 改善策を実行する: 改善策を実行し、効果を検証しましょう。
- 効果がなければ再分析: 効果が見られない場合は、層別する項目を変えて再分析してみましょう。
- 継続的な改善: 層別とQC七つ道具を継続的に活用することで、品質向上を目指しましょう。
QC七つ道具×層別で実現できること
QC七つ道具と層別を組み合わせることで、現場の品質向上に大きく貢献することができることは、ご理解いただけてきたかと思います。
では具体的な改善事例を紹介しながら、あらためて品質向上に対するQC七つ道具×層別で実現できることをまずは事例から見ていきましょう。
現場の改善事例
今回は食品工場における問題解決を事例1、自動車部品工場における問題解決を事例2として用意しました。
事例1:食品工場における異物混入の削減
ある食品工場では、製品への異物混入が大きな問題となっていました。
そこで、QC七つ道具と層別を用いて、異物混入の原因を徹底的に分析しました。
まず、チェックシートを用いて異物混入の状況を記録し、「発生場所」「異物の種類」「発生時間帯」などで層別しました。
その結果、特定の製造ラインで、特定の時間帯に、髪の毛の混入が多いことが判明しました。
さらに、特性要因図を用いて原因を分析した結果、その時間帯に作業する従業員の帽子着用が不十分であることが原因として考えられました。
そこで、帽子の着用を徹底させ、定期的な点検を行うことで、異物混入を大幅に削減することに成功しました。
事例2:自動車部品工場における不良品の削減
ある自動車部品工場では、ある部品の寸法不良が問題となっていました。
そこで、ヒストグラムを用いて部品の寸法を測定し、「製造日」「製造ライン」「作業者」などで層別しました。
その結果、特定の製造ラインで、特定の作業者が担当した日に製造された部品に、寸法不良が多いことがわかりました。
さらに、散布図を用いて分析した結果、その作業者の作業時間と不良品発生率に相関関係があることが判明しました。
その作業者は、長時間作業を続けると集中力が低下し、ミスが増える傾向がありました。
そこで、作業時間を短縮し、休憩をこまめにとるように改善した結果、不良品発生率を大幅に削減することができました。
実現できること1:作業効率の向上
QC七つ道具×層別を用いることで、作業のムダをなくし、作業効率を向上させることができます。
例えば、作業時間を分析し、「作業者」「作業内容」「時間帯」などで層別することで、作業時間のバラつきや、非効率な作業手順を発見することができます。
これらの問題点を改善することで、作業時間を短縮し、生産性を向上させることができます。
実現できること2:品質向上とコスト削減
QC七つ道具×層別を用いることで、不良品を減らし、品質を向上させることができます。
不良品を減らすことは、顧客満足度向上だけでなく、材料費や人件費などのコスト削減にもつながります。
また、工程の異常を早期に発見し、適切な対策を講じることで、不良品の発生を未然に防ぐことができます。
実現できること3:チームワークの向上
QC七つ道具×層別を用いた品質管理活動は、チームで協力して行うことが重要です。
問題解決に向けて、チームで議論し、協力することで、チームワークが向上し、より良い職場環境を作ることができます。
また、全員が品質管理の意識を高め、積極的に改善活動に参加することで、さらなる品質向上につながります。
まとめ:QC七つ道具×層別の効果と実践方法
ここまで、QC七つ道具と層別の基本から、現場での活用方法、そして品質向上に繋がる効果まで、詳しく解説してきました。
「層別」って難しそう… 「QC七つ道具なんて、専門家が使えればいいんじゃないの?」
そう思っていた方もいるかもしれません。
でも、実際には、層別は 「データをグループ分けする」 という、とてもシンプルな考え方です。
そして、QC七つ道具も、少し練習すれば、誰でも簡単に使いこなせるツールです。
この二つを組み合わせることで、
- 今まで見えなかった問題点が発見できる!
- 問題の原因を特定し、効果的な対策を打てる!
- 作業効率がアップし、品質も向上する!
- コスト削減にも貢献できる!
- チームワークが向上し、働きがいのある職場になる!
など、たくさんの素晴らしい効果が期待できます。
「百聞は一見に如かず」ということわざがあるように、まずは一度、層別とQC七つ道具を使ってみませんか?
きっと、あなたの職場でも、驚くような発見や改善につながるはずです。
例えば、
- 毎日の生産量を記録しているなら、「曜日別」「作業者別」に層別して、違いがないか調べてみましょう。
- 不良品が多いなら、「不良の種類別」「発生時間帯別」に層別して、傾向を分析してみましょう。
- 作業時間にバラつきがあるなら、「作業者別」「作業内容別」に層別して、原因を探ってみましょう。
最初は、簡単なことからで構いません。
小さなことから始めて、少しずつ改善を重ねていくことで、大きな成果に繋がるはずです。
さあ、今日からあなたも、QC七つ道具×層別で、品質管理のプロを目指しましょう!