製造業の現場で働く我々にとって、品質は本当に大切なものですよね。お客様からの信頼を得るのも、会社が成長していくのも、やはり品質がしっかりしていることが大前提です。
前回は品質管理の基本的な考え方として、「後工程には不良品を流さない」を詳しく解説しました。「後工程はお客様」という意識を持って、自分の工程で責任をもって品質を作り込む。これは、私たち製造業に携わる人間にとって、すごく大切なことです 。

でも、「後工程に流さない」ことに加えてあと2つ、大切にしなければならないことがあります。そのうちの1つが、今回のテーマである「前工程に知らせる」ということなんです。
「前工程に知らせる」って、どういうこと?
簡単に言うと、自分の工程や、もっと後の工程で不良が見つかった時に、「この不良、もしかしたら前の工程に原因があるかも?」と思ったら、その情報を前の工程にきちんと伝える、ということです 。
「え?ただそれだけ?」って思いましたか?
でも、これって、不良をなくしていくために、すごく重要なことなんです。
そのため今回は、「前工程に知らせる」って、具体的にどういうことなのか、なんで、それがそんなに大切なのか、実際にどうやればいいのか、について、わかりやすく解説していきます。
今回も読み終えるまでのお時間、しばらくお付き合いくださいませ。
なぜ「前工程に知らせる」が重要なのか?
さて、それでは、なぜ「前工程に知らせる」ことがそんなに重要になってくるのでしょうか?まずは品質管理の第一原則である「後工程に不良を流さない」から振り返ってまいりましょう。
品質管理の第一原則「後工程に不良を流さない」
品質管理の第一原則として、「後工程に不良を流さない」という考え方を前回説明しました。これは、自分の工程で不良を発見したら、そこで食い止めて、次の工程に不良品を送らない、という基本的なルールです。
でも、これって、当たり前のことのように聞こえますが、実は奥が深いんです。
もし、前の工程から流れてきた不良を、自分の工程で発見して、そこで食い止めたとします。これは、「後工程に流さない」という原則を守った、ということになりますよね。
でも、ちょっと考えてみて欲しいのですが、その不良、いったいどこから来たんでしょう?
もしかしたら、もっと前の工程で、同じような不良がたくさん発生しているかもしれません。それをそのままにしておくと、結局、検査や手直しに時間や手間がかかって、ムダが、被害が、どんどん多くなってしまいます 。
それに、不良の原因が前の工程にある場合、それを前の工程に伝えて、原因をしっかり解決しない限り、同じ条件が揃えば、また同じ不良が何度も出てきてしまう可能性があります 。
だから、「後工程に流さない」という考え方はとても大切なんですが、それだけでは、品質を根本的に改善することは難しいんです。
「前工程に知らせる」の定義と重要性
そこで出てくるのが、今回のテーマである「前工程に知らせる」という考え方です。
「前工程に知らせる」というのは、自分の工程や、もっと後の工程で不良が見つかった時に、その不良の原因が前の工程にあるかもしれません、なのでその不良発生の情報を前の工程に伝えることです 。
これは、ただ単に「不良がありました」と伝えるだけではありません。
「いつ、どこで、どんな不良が発生したのか」
「もしかしたら、この工程のここが原因かもしれない」
というように、できるだけ具体的に、正確に伝えることが大切です 。
なぜ、そんなことをする必要があるのでしょうか?
それは、「前工程に知らせる」ことが、不良の根本的な原因を解決し、同じような不良が二度と発生しないようにするために、とても重要なカギとなるからです 。
さて、それは具体的にどのようなことなのでしょうか?できるだけわかりやすく解説していきましょう。
「前工程に知らせる」とは?中小製造業のための分かりやすい解説
ここでは、「前工程に知らせる」という考え方について、もう少し詳しく見ていきましょう。「前工程に知らせる」って、一体どういうことなんでしょうか?
「前工程に知らせる」原則の定義
「前工程に知らせる」というのは、ものづくりの工程で、自分の工程や、自分の工程よりも後の工程で不良が見つかった時に、「この不良、もしかしたら自分よりも前の工程が原因かもしれない」との可能性を捉え、その情報を前の工程に伝えることです 。
でも、ただ単に「不良がありました」と伝えるだけではありません。
- 「いつ、どこで、どんな不良が発生したのか」
- 「不良の具体的な状況はどうだったのか」
- 「もしかしたら、この工程のこの部分が原因かもしれない」
というように、できるだけ具体的に、正確に伝えることが大切です 。
そして、この情報を伝えることで、前の工程の人たちに、
- 「何が問題だったのか」
- 「どうすれば同じような不良を二度と出さないようにできるのか」
ということを考えてもらい、改善につなげてもらう、という大事な目的があります 。
つまり、「前工程に知らせる」というのは、単なる情報伝達ではなく、前の工程の人たちと一緒に品質を良くしていくための、積極的なコミュニケーション活動なんです 。
「後工程はお客様」意識だけでは不十分な理由
以前、品質管理の基本的な考え方として、「後工程はお客様」という考え方を解説しました。もちろん「自分の工程はお客様に製品を届ける最後の工程だ」という意識を持つことは、品質を作り込む上でとても大切です 。
でも、「後工程はお客様」という意識だけでは、やはり十分とは言えないんです。
なぜなら、「後工程はお客様」という考え方だけだと、どうしても「自分の工程で不良を出さないようにしよう」という意識が中心になってしまうからです 。
もちろん、自分の工程で不良を出さないようにすることはとても大切です。でも、それだけでは、不良が繰り返し発生してしまうことを防ぐことはできません 。
不良の原因が前の工程にある場合、それを前の工程に伝えて、原因を解決しない限り、同じような不良が何度も出てきてしまう可能性があります 。
それに、不良を後工程で発見して、手直ししたり、廃棄したりするのには、時間もお金もかかります 。
そのため、できるだけ早い段階で不良の原因を特定して、根本的な対策をすることで、ムダなコストを減らすことがとても大切な考え方になります。
だから、「後工程はお客様」という意識に加えて、「前工程に知らせる」という考え方も持つことで、不良の発生を未然に防ぎ、品質をさらに向上させることができるのです 。
中小製造業における「前工程に知らせる」の意義
中小製造業にとって、「前工程に知らせる」ということは、特に重要な意味を持ちます。
中小製造業では、大企業と比べて、
- 人が少ない
- 時間がない
- お金もあまりない
というように、色々な面で制約があることが多いです 。
だからこそ、「前工程に知らせる」という考え方を実践して、
- 不良の発生を未然に防ぎ、手直しや検査にかかるムダな時間やコストを減らす
- 品質を向上させることで、お客様からの信頼を得て、仕事をもっともらえるようにする
- 工程の流れをスムーズにして、もっと効率よく製品を作れるようにする
といった効果を得ることが、会社の成長につながるために非常に大切なのです 。
また、「前工程に知らせる」ことを通して、
- 部門間のコミュニケーションが活発になる
- みんなで協力して問題を解決するチームワークが生まれる
- 従業員の皆さんの問題解決能力が向上する
といった、品質以外の面でも、良い影響がたくさんあります 。
このように、「前工程に知らせる」ということは、中小製造業にとって、品質を向上させるだけでなく、会社全体の力を高めるための、とても重要な考え方なのです。
「前工程に知らせる」ことで生まれる5つのメリット
不良が発生するのには、必ず原因があります。その原因が、設計にあるのか、材料にあるのか、それとも製造工程にあるのか。原因を特定しなければ、対策を立てようがありません。
「前工程に知らせる」ということは、その原因を特定するための、最初の第一歩なのです。
そして、「前工程に知らせる」ことによって、具体的にどんな良いことがあるのでしょうか?
「前工程に知らせる」ことで生まれる、5つのメリットをご紹介してみましょう。
メリット1:不良コストの削減:手戻り、再加工、廃棄コストの減少
不良が発生すると、それを手直ししたり、もう一度作り直したり、最悪の場合は廃棄したりしなければなりません。これらの作業には、時間も手間もお金もかかります。
でも、「前工程に知らせる」ことを実践して、不良の原因を根本から解決することができれば、これらのムダなコストを大幅に減らすことができます。
特に、工程が進めば進むほど、不良の手直しや廃棄にかかるコストは大きくなります。だから、できるだけ早い段階で原因を特定し、対策を講じることが大切なのです。
メリット2:検査コストの削減:不良率低下による検査工程の効率化
不良が頻繁に発生する場合、それを発見するために、何度も検査をしなければなりません。検査をする人が必要ですし、検査をするための設備も必要になります。これらにも、当然コストがかかります。
でも、「前工程に知らせる」ことを実践して、不良の発生率を下げることができれば、検査の回数を減らしたり、検査の工程を簡単にしたりすることができます。
それによって、検査にかかる人員や設備のコストを減らすことができるのです。
メリット3:品質向上と顧客満足度向上:クレーム減少、信頼獲得
不良が少ない、品質の良い製品を安定して作ることができるようになれば、お客様からのクレームや返品も減ります。
そして、「この会社は、いつも品質の良い製品を作ってくれる」と、お客様からの信頼を得ることができます。
お客様からの信頼は、会社の評判を高め、新たな仕事につながる可能性も秘めています。
つまり、品質向上は、会社の成長にもつながる、とても重要な要素なのです。
メリット4:生産性向上:ライン停止減少、スムーズな工程
不良が発生すると、生産ラインを止めたり、作業を中断したりして、原因を調べたり、対策を考えたりしなければならない場合があります。
これは、生産性の低下に繋がります。
でも、「前工程に知らせる」ことを実践して、不良の発生を減らすことができれば、ラインを止めたり、作業を中断したりする回数を減らすことができます。
その結果、生産性が向上し、より多くの製品を、より効率よく作ることができるようになるのです。
メリット5:設計品質向上:製造現場からのフィードバック活用
「前工程に知らせる」ということは、設計部門にとっても、良い影響があります。
製造現場から「この設計だと、こういう不良が発生しやすい」というようなフィードバックを設計部門に伝えることで、設計の段階から不良が発生しにくい製品を設計することができるようになります。
つまり、「前工程に知らせる」ということは、より良い製品を作るための、設計部門と製造現場の間の、重要なコミュニケーションツールにもなるのです。
このように、「前工程に知らせる」ということは、コスト削減、品質向上、生産性向上など、様々な面で会社に大きなメリットをもたらします。
特に、人が少なく、時間もお金も限られている中小製造業にとって、「前工程に知らせる」ことは、これらの問題を解決し、会社を成長させていくための、非常に重要な考え方なのです。
中小製造業が「前工程に知らせる」を実践する上での「よくある悩み」と解決策
さて、「前工程に知らせる」ことが大切だということは分かったけど、「うちは中小企業だから、なかなか難しいんだよな…」と思っている方もいるかもしれません。
確かに、中小製造業では、品質管理について、大企業とは少し違った悩みがあることが多いです。
でも、心配しないでください!
ここでは、中小製造業でよくある悩みと、それに対する解決策を、具体的にお話していきます。
中小製造業が抱える品質管理の課題を具体的に提示
中小製造業では、品質管理に関して、以下のような課題を抱えているケースがよくあります。
リソース不足:人材不足、設備・ツールの限界、情報システムの未整備
- 人材不足: 品質管理の専門の担当者を置く余裕がなかったり、一人の人がたくさんの仕事を掛け持ちしていたりして、不良の原因をじっくり分析したり、改善策を考えたりする時間がない、という悩みです 。
- 設備・ツールの限界: 最新の検査機器や、情報を共有するためのシステムを導入するお金がなくて、手作業で検査をしたり、紙で情報をやり取りしたりしているので、時間がかかったり、ミスが起こりやすかったりする、という悩みです.
- 情報システムの未整備: 各部門でバラバラに情報を管理していて、必要な時に必要な情報がすぐに手に入らない、という悩みです 。
組織文化とコミュニケーションの壁:部門間の壁、犯人探しの文化、経営層の理解不足
- 部門間の壁: 設計部門、製造部門、検査部門など、各部門間の連携が悪くて、情報がスムーズに伝わらない、という悩みです 。
- 「犯人探し」の文化: 不良が発生した時に、原因を追究するよりも、「誰がやったんだ!」と責任を追及するような雰囲気があって、現場の人がミスを報告しにくく、問題を隠してしまう、という悩みです 。
- 経営層の理解不足: 経営層が品質管理の重要性を十分に理解していなくて、「品質管理なんて、お金がかかるだけでムダだ」と思っているため、必要な人員や設備を確保してもらえない、という悩みです 。
標準化と教育の不足:作業手順の不統一、品質教育の不足
- 作業手順の不統一: 作業の手順がきちんと決まっていなかったり、決まっていても守られていなかったりして、人によってやり方が違うため、不良の原因を特定しにくい、という悩みです 。
- 品質教育の不足: 従業員に対して、品質管理の基本的な考え方や、不良を発見した時の報告の仕方などについて、十分な教育が行われていない、という悩みです 。
これらの課題は、一つ一つが独立しているわけではなく、お互いに複雑に絡み合っていることが多いです。
でも、これらの課題を解決しない限り、「前工程に知らせる」をうまく実践することはできません。
課題克服のための解決策
そこで、これらの課題を克服するための、現実的な解決策をいくつかご紹介します。
- できることから少しずつ始める: 最初から完璧を目指すのではなく、「まずは、不良を見つけたら、すぐに作業を止めて、リーダーに報告する」というように、簡単なルールを決めて、それを徹底することから始めましょう。
- 身近なもので工夫する: 高価なシステムを導入しなくても、エクセルやワードなど、今あるツールを工夫したり、ホワイトボードや掲示板などを活用したりすることで、情報を共有したり、「見える化」をしたりすることは可能です。
- コミュニケーションを活発にする: 朝礼や終礼などの機会を利用して、積極的に情報交換をしたり、部門間の交流を深めたりするように心がけましょう。
- 「犯人探し」ではなく「原因究明」: 不良が発生した時は、「誰が悪い」ではなく、「なぜ起きたのか」を徹底的に追及し、再発防止策を考えることに重点を置きましょう。
- 経営層を巻き込む: 品質管理の重要性を経営層に理解してもらうために、具体的なデータを示したり、改善事例を紹介したりして、粘り強く働きかけましょう。
- 学び続ける姿勢: 品質管理に関する研修に参加したり、本を読んだりして、常に新しい知識や技術を学ぶように心がけましょう。
これらの解決策は、どれもすぐに効果が出るものではありません。
でも、諦めずに、根気強く取り組んでいくことで、必ず成果は出ます。
大切なのは、「できない理由」を探すのではなく、「どうすればできるか」を考え、できることから一歩ずつ、着実に改善を進めていくことです。
はい、承知いたしました。
「前工程に知らせる」ための具体的な実践ステップと現場で使えるヒント
ここでは、「前工程に知らせる」を具体的にどのように進めていけばいいのか、現場で使えるヒントも交えながら、わかりやすく解説していきます。
ステップ1:「止める・呼ぶ・待つ」の徹底:不良の拡大を防ぐ基本動作を解説
作業中に「あれ?なんか変だな」と思ったら、まず、機械やラインを「止める」。
そして、すぐにリーダーや上司を「呼ぶ」。「ちょっと見てもらえますか?」と、ためらわずに声をかけてください。
そして、リーダーや上司から指示があるまで、勝手に触ったりせずに「待つ」。
これが、不良品をそれ以上作らないために、そして、問題を大きくしないために、一番大切な基本動作です.
「こんなことでラインを止めたら、みんなに迷惑がかかるんじゃないか…」
そう思う人もいるかもしれません。
でも、不良をそのままにして作り続けてしまう方が、もっと大きな迷惑になります。
だから、少しでも「おかしいな」と思ったら、勇気をもって「止める・呼ぶ・待つ」を徹底してください。
そして、管理者の皆さんは、作業者の皆さんが、ためらわずに報告できるように、普段から
「何かあったら、すぐに言ってください」
「みんなで協力して解決しましょう」
というように、声をかけて、安心できる雰囲気を作ることが大切です.
ステップ2:シンプルな情報伝達の仕組みづくり
不良を発見した時に、その情報を関係者に伝えるための、シンプルな仕組みを作りましょう。
報告フォーマットの標準化:5W1Hを意識したテンプレート作成
誰が報告しても、必要な情報が漏れなく、分かりやすく伝わるように、報告のフォーマット(テンプレート)を決めましょう.
報告フォーマットには、
- いつ (When): いつ発生したのか
- どこで (Where): どの工程で発生したのか
- だれが (Who): だれが発見したのか
- なにを (What): どんな不良なのか
- なぜ (Why): なぜ発生したと考えられるのか
- どのように (How): どのように対処したのか
といった、5W1Hを意識した項目を入れておくと、情報が整理されて、伝わりやすくなります。
エクセルやワードなどで、簡単なテンプレートを作っておけば十分です.
大切なのは、現場の誰もが、簡単に使えることです.
最初から完璧なものを作るのではなく、実際に使ってみて、改善していく、という考え方でOKです.
コミュニケーション手段の確立:迅速かつ確実な伝達方法
不良を発見したら、できるだけ早く、関係者に情報が伝わるように、誰に、いつまでに、どのように報告するか、というルールを決めましょう.
- 迅速性: 口頭で直接伝える、電話する、チャットツールを使う、メールするなど、状況に応じて、一番早く確実に伝わる方法で報告します.
- 確実性: 誰に(担当者、リーダー、関連部署)、いつまでに報告するかを明確にします。
- 記録: 重要な情報は、後で確認できるように、報告書やツール上に記録しておくと良いでしょう。
ステップ3:不良の「見える化」で早期発見と意識向上
不良の発生状況や、改善の状況などを、みんなが見えるようにすることも、非常に効果的です。
- 現品票・不良タグ: 不良品に、不良の内容や発生した工程などを書いた紙(現品票)やタグをつけて、関係者がすぐに見える場所に置きます。
- 管理ボード: 不良の種類ごとに、発生件数をグラフなどにして、掲示板などに貼り出します.
- アンドン: 生産ラインで異常が発生した時に、ランプや音で知らせる仕組みです.
- デジタルツール: 品質管理システムや、現場帳票ツールなどを使って、データを自動的に集計したり、グラフ化したりすることもできます.
「見える化」をすることで、問題が早く見つかるようになったり、みんなの意識が高まったり、改善活動がスムーズに進んだり、といった効果が期待できます.
ステップ4:原因分析と対策で不良の再発防止
不良が発生した原因を分析し、二度と同じような不良が発生しないように対策を立てることも、非常に重要です。
原因分析の手法としては、
- なぜなぜ分析: 「なぜ?」を5回繰り返して、根本的な原因を追究する手法
- 4M分析: 人 (Man)、機械 (Machine)、材料 (Material)、方法 (Method) の4つの視点から原因を分析する手法
- 特性要因図: 魚の骨のような図を使って、原因を整理する手法
など、様々なものがあります。
これらの手法を使って、不良の原因を特定し、具体的な対策を立て、それを実行することで、不良の再発を防止することができます。
ステップ5:デジタルツールの活用で効率化と精度向上
最近では、
- 現場帳票ツール: 紙の帳票をタブレットなどで電子化するツール
- コミュニケーションツール: チャットツールなど
- 品質管理システム (QMS): 不良の情報や、改善の記録などを一元管理するシステム
など、品質管理に役立つ様々なデジタルツールが登場しています。
これらのツールを導入することで、
- 記録作業の効率化
- 情報のリアルタイム共有
- データ分析の迅速化
などが可能になり、品質管理のレベルをさらに向上させることができます。
これらのステップやヒントを参考に、皆さんの現場に合った「前工程に知らせる」の仕組みを作ってみてください。
大切なのは、最初から完璧を目指すのではなく、できることから少しずつ始めて、継続的に改善していくことです。
事例紹介:中小製造業における「前工程に知らせる」成功事例と学び
ここでは、「前工程に知らせる」を実践することで、実際に品質改善に成功した中小製造業の事例と、大企業の品質管理原則から学べる点を紹介します。
中小製造業における「前工程に知らせる」の実践事例
中小製造業が「前工程に知らせる」を実践し、品質向上や生産性向上につなげた事例は、多くの中小企業にとって参考になります。
事例1:Kintone導入による不良削減(金属加工業・100人規模)
- 課題: 月間38件程度の不良が発生していた 。
- 取り組み: 品質不良情報を記録・共有するためにKintoneを導入。特に「個人別の不良品発生件数」を見える化。現場作業者が入力しやすいように入力項目を工夫し、現場に大型モニターを設置してデータを共有。月1回の成果報告会を実施 。
- 効果: 導入から8ヶ月後、従業員が自律的にPDCAを回すようになり、月間不良発生件数が最大5件に激減し、効果が持続 。
この事例から、デジタルツールを活用して情報を「見える化」し、現場の従業員が主体的に改善活動に取り組むことで、大きな成果が得られることが分かります。
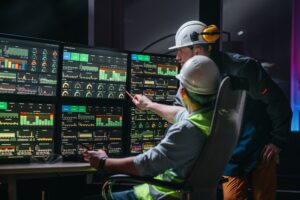
事例2:QC工程表の活用による品質改善(中小企業全般)
- 取り組み: QC工程表を作成・運用し、各工程での管理項目や基準を明確化。現場からのフィードバックを積極的に取り入れ、定期的に見直し、継続的に改善 。
- 効果: 製品品質の一貫性が保たれ、問題の早期発見と迅速な対応が可能になる 。QC工程表が、工程間の共通言語となり、フィードバックの基準となる 。
QC工程表は、各工程の品質基準を明確にし、工程間のコミュニケーションを円滑にするための有効なツールです。
事例3:デジタルツール導入による効率化・品質向上(中小企業事例)
- 取り組み: クラウド型作業管理システム、IoT技術、現場帳票ツール、データ共有基盤などを導入 。
- 効果: 紙ベースの管理からの脱却によるペーパーレス化、工数削減、リアルタイムでの情報共有、データに基づいた異常検知や原因分析の迅速化、作業ミスの削減、品質向上、納期遵守率の向上など 。
これらの事例から、デジタルツールは、情報共有を効率化し、品質向上に大きく貢献することがわかります。
事例4:コミュニケーションツールによる連携強化(ガス栓メーカー、筆記具メーカー)
- 取り組み: 拠点間が離れている課題に対し、テレビ会議システムや電子黒板を導入(サンコー 、三菱鉛筆 )。
- 効果: 物理的な距離や部門間の壁を越えたリアルタイムなコミュニケーションを実現し、情報共有や意思決定のスピードを向上 。
コミュニケーションツールは、迅速な情報伝達を可能にし、部門間の連携を強化します。
これらの事例から、中小企業においても、デジタルツールをうまく活用し、現場の従業員を巻き込みながら、情報を見える化し、フィードバックループを構築することが品質改善の鍵であることがわかります 。
大企業の品質管理原則から学ぶべき点を解説
大企業の品質管理手法は、中小企業がそのまま導入することは難しいかもしれませんが、その根底にある原則や考え方は非常に参考になります 。
トヨタ生産方式(TPS)の「自工程完結」「アンドン」「なぜなぜ分析」
- 自工程完結: 各工程が責任を持って品質を作り込み、不良を後工程に流さないという考え方 。前工程からのインプット品質が保証され、自工程で異常があればすぐに検知・対応する仕組みが必要です 。
- アンドン: 異常発生を即座に知らせる「見える化」の代表例 。中小企業でも、簡易的なランプやボードで同様の仕組みを構築できます 。
- なぜなぜ分析: 問題の根本原因を追求する手法 。フィードバックされた情報をもとに、この分析を行うことが再発防止に繋がります 。
トヨタ生産方式は、品質を作り込むための基本的な考え方や、問題を解決するための有効な手法を提供してくれます。

OEMにおける構造化されたフィードバックプロセスとデータ連携
- 構造化されたプロセス: 大手OEMでは、製造現場(あるいは市場)からの不良データを収集し、分析、設計・エンジニアリングチームへフィードバックし、是正処置、検証という一連のプロセスが体系的に構築されています 。
- データ連携: MES(製造実行システム)やPLM(製品ライフサイクル管理)システムを活用し、設計から製造、市場までのデータを連携させ、トレーサビリティを確保し、精度の高いフィードバックを実現しています 。
OEMの事例は、フィードバックプロセスを体系化し、データを活用することの重要性を示しています。
AIによる品質予測
- 先進事例: 生産プロセスデータをAIで解析し、最終品質を予測。予測に基づき、リアルタイムで前工程の設備条件を自動制御し、品質のばらつきを抑える取り組みも始まっている 。
- 将来性: これは、単純な事後フィードバックを超えた、予測に基づいたプロアクティブな品質管理であり、将来的には中小企業にも応用可能な技術となる可能性があります 。
AIによる品質予測は、今後の品質管理のあり方を示唆する先進的な事例です。
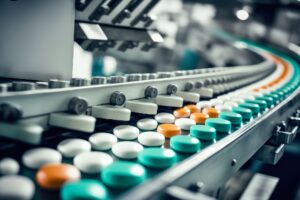
大企業の事例は、中小企業にとって、品質管理の目指すべき方向性や、原則の重要性を再認識する機会となります 。
事例から読み取れる成功要因
これまでに紹介した中小企業や大企業の事例から、「前工程に知らせる」仕組みを効果的に構築・運用するための共通の成功要因が見えてきます。
はい、承知いたしました。成功要因のうち、特に重要な5つについて、わかりやすく解説します。
成功要因①:明確な目標設定
品質改善に取り組む上で、最初にとても大切なのが、「何のためにやるのか?」という目標をはっきりと定めることです.
たとえば、「不良率を〇〇%減らす」「手直しにかかる時間を半分にする」といった具体的な目標を決めます。
目標を定めることで、関係者の意識が統一され、「みんなで達成しよう!」という気持ちが生まれます.
目標が曖昧だと、途中で何をやっているのか分からなくなってしまい、改善活動も長続きしません。
だからこそ、できるだけ具体的な目標を、関係者みんなで話し合って決めることが大切なんです。
成功要因②:現場の巻き込み
品質改善は、机の上だけで考えるのではなく、実際に作業をしている現場の人たちの意見を聞きながら進めることがとても大切です.
現場の人たちは、作業の問題点や改善点について、一番よく知っています。
現場の人たちが「自分たちの意見が反映されている」と感じられれば、改善活動にも積極的に参加してくれます.
逆に、現場を無視して進めてしまうと、「どうせ言ってもムダだ」と思われて、協力してもらえなくなってしまいます。
だから、現場の人たちとよく話し合い、一緒に改善を進めていくことが、成功のためには欠かせません。
成功要因③:適切なツールの活用
品質管理を効率的に、そして効果的に行うためには、適切なツールを使うことも重要です.
たとえば、不良の発生状況を記録したり、データを分析したりするためのツール、関係者間で情報を共有するためのツールなど、様々なものがあります。
最近では、スマホやタブレットで使える便利なツールもたくさんあります。
ただし、高価なツールを導入すれば良いというわけではありません。
自社の規模や状況に合わせて、本当に必要なツールを選ぶことが大切です.
成功要因④:強力なフィードバックループ
「フィードバックループ」とは、簡単に言うと、「情報を伝えて、それに対する反応を受け取り、さらに改善につなげる」という一連の流れのことです.
品質改善においては、
- 後工程から前工程へ不良の情報を伝える
- 前工程で原因を調べて対策を立てる
- 対策が効果があったかどうかを確認する
という流れを、何度も繰り返すことが大切です。
このループをしっかり回すことで、不良が減り、品質がどんどん良くなっていきます。
成功要因⑤:継続的改善
品質改善は、一度やって終わりではありません。常に「もっと良くできるはずだ」という意識を持って、改善を続けることが大切です.
社会やお客様のニーズは常に変化しています。
それに対応するためにも、品質管理の仕組みや方法を、定期的に見直す必要があります。
小さな改善を積み重ねていくことで、大きな成果につながります。
これらの5つの要因を意識して、品質改善に取り組んでみてください。
「前工程に知らせる」と連携することで相乗効果を生む8つの品質管理手法
「前工程に知らせる」という考え方は、それ単独で存在するのではなく、他の品質管理手法と連携することで、より大きな力を発揮します.
ここでは、特に「前工程に知らせる」と組み合わせることで相乗効果が生まれる、代表的な8つの品質管理手法を紹介します.
なぜなぜ分析:根本原因の追求
「なぜ?」を繰り返して、問題の根本的な原因を突き止める手法です.
前工程からのフィードバックは、「なぜ?」を始めるきっかけとなります.
より具体的なフィードバックがあれば、分析がスムーズに進み、より深い原因までたどり着けます.

ポカヨケ:ヒューマンエラー防止
人間のうっかりミス(ポカ)を防ぐための仕組みを作る手法です.
前工程からのフィードバックで、どんなミスが起こりやすいのかを把握し、効果的なポカヨケを導入することができます.
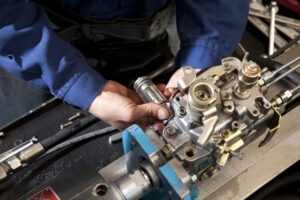
QCサークル:現場主体の改善活動
現場のメンバーが集まって、品質改善などのテーマについて話し合い、解決策を実行する活動です.
後工程からのフィードバックは、QCサークルで議論するテーマとなり、改善につなげるための貴重な情報源となります.
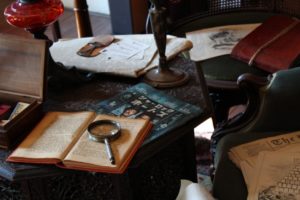
トレーサビリティ:原因特定の迅速化
製品の製造過程を追跡できる仕組みです.
不良が発生した場合に、トレーサビリティの仕組みがあれば、原因となったロットや材料などを特定しやすくなり、前工程へのフィードバックも的確に行えます.
工程内検査/自主検査:不良の早期発見
各工程で行う品質チェックです.
前工程から受け取ったものが不良であれば、それを発見し、すぐに前工程にフィードバックすることが重要です.
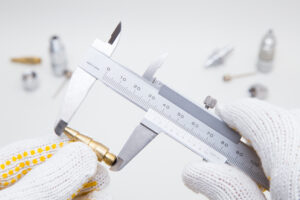
4M分析:原因の多角的分析
人(Man)、機械(Machine)、材料(Material)、方法(Method)の4つの視点から原因を分析する手法です.
前工程からのフィードバックを受けて、4Mのどの要素に問題があったのかを分析することで、より効果的な対策を立てることができます.
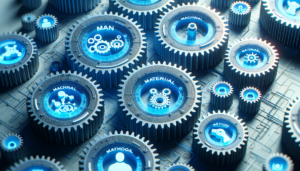
PDCAサイクル:継続的な改善
Plan(計画)→ Do(実行)→ Check(評価)→ Act(改善)のサイクルを回して、継続的に改善していく手法です.
前工程からのフィードバックは、Check(評価)の段階で、改善の効果を評価するために活用されます.
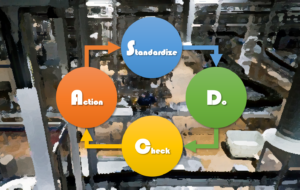
標準化:作業手順の明確化
作業の手順や検査の基準などを明確に定めることです.
標準から外れた作業が行われたことが原因で不良が発生した場合、その情報を前工程にフィードバックし、標準を見直す必要があります.
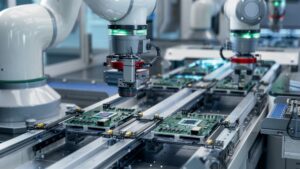
これらの手法と「前工程に知らせる」を連携させることで、品質管理のレベルをさらに向上させることができます.
はい、承知いたしました。
まとめ:中小製造業の持続的な成長を支える「前工程に知らせる」
ここまで、「前工程に知らせる」という考え方について、様々な角度から解説してきました.
改めて強調したいのは、「前工程に知らせる」ことは、決して大企業だけのものではなく、中小製造業にとっても、非常に重要な意味を持つということです.
確かに、中小製造業では、
- 人が足りない
- 時間がない
- お金もない
といった課題を抱えている場合が多いかもしれません.
しかし、だからこそ、「前工程に知らせる」を実践することで、
- 不良の発生を未然に防ぎ、手直しや検査にかかるムダなコストを減らす
- 品質を向上させることで、お客様からの信頼を得て、もっと仕事をしてもらえるようにする
- 工程の流れをスムーズにして、もっと効率よく製品を作れるようにする
といった効果を得ることが、会社の成長につながるために非常に大切なのです.
「前工程に知らせる」というと、なんだか難しそうに聞こえるかもしれませんが、決してそんなことはありません.
大切なのは、完璧な仕組みを最初から作ろうとするのではなく、できることから少しずつ始めることです.
たとえば、
- 不良を見つけたら、すぐに作業を止めて、リーダーに報告する
- 不良の内容を、簡単な紙に書いて、前の工程の人に渡す
- 朝礼などで、不良の情報を共有する
といった、簡単なことからでも十分です.
そして、これらの活動を続ける中で、
- もっとこうした方が分かりやすいな
- もっとこうすれば効率が良くなるな
というように、改善を加えていけば良いのです.
「前工程に知らせる」は、単なるルールではありません.
それは、
- みんなで協力して、より良い製品を作ろう
- みんなで知恵を出し合って、もっと働きやすい職場にしよう
という、私たち一人ひとりの意識を変える力を持っています.
今回の内容で、少しでも「前工程に知らせる」に興味を持っていただけたなら、ぜひ、できることから始めてみてください.
この記事を最後まで読んだあなた自身の小さな一歩が、会社を大きく成長させる力となるはずです.