IE手法の7つ道具の動作分析(作業分析)
その代表手法のライン作業分析について
いくつかの記事で詳しく解説をしました
7つ道具は『見える化』ツールです
そのため分析を進めてムダを探り出し
最後は関係者で改善案を考えます
そう、ライン作業分析の場合は
最後の最後に作業を寄せてあげて
編成効率の向上を図ります
実はその時の重要な改善ポイントが
いくつか存在するのです!
今回はそのポイントを紹介します
ライン作業分析のおさらい
ライン作業分析についてはこれまで
4つの記事で詳しく解説をしてきました
ライン作業分析の概要は以下の記事
[getpost id=”2445″]
その中核のピッチダイアグラムはこちら
[getpost id=”394″]
そしてラインバランス改善手法の記事
[getpost id=”2451″]
さらに押さえておくべき重要ポイントも
[getpost id=”622″]
もちろんこの分析手法は本当に有名で
多くの現場で使われています
要するにそれほど効果が出やすい手法
だということです
ライン作業分析の最終段階:作業分担の見直しポイント
ライン作業分析を進めていって
ピッチダイアグラムをつくっている過程で
たくさん改善案を思いつくものです
まずは単位作業そのものを最適化して
稼働時間や良品率を上げて編成効率を向上
そうすればいよいよ作業を寄せて上げて
作業を担当する要員数を減らせます
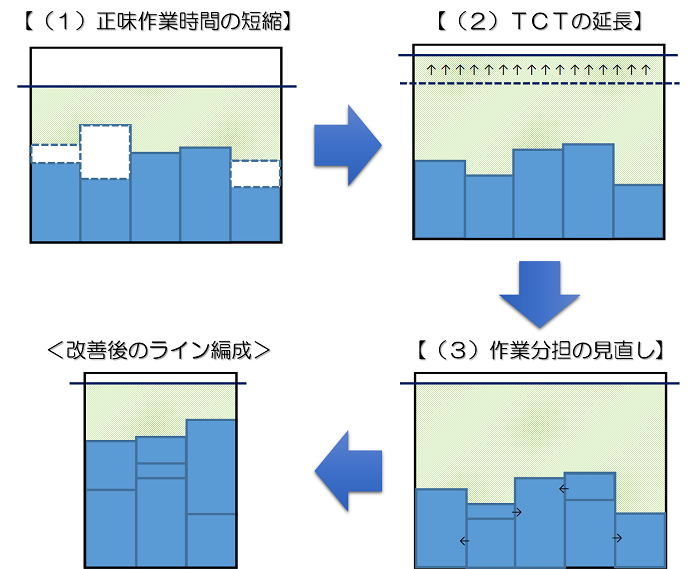
IE手法7つ道具④動作分析(作業分析)ピッチダイアグラム作成後の改善手法-ライン作業分析編2より
要するに作業分担の取り崩しをすることで
見直しを図るわけです
その時に留意して欲しいポイントを
下記に述べますので気をつけてください
改善ポイント1:積上げた作業時間はTCTを超えない
TCT、つまり目標サイクルタイムを
超えてしまった工程が存在すると
ネック工程となって全体を圧迫します
つまり時間内で必要生産量を
確保できない状態になってしまうため
最悪は残業対応となって本末転倒です
そのためこのルールはまず
守るように見直しを進めてください
改善ポイント2:作業の分担単位をちゃんと考慮する
ワークユニット、つまり
単位作業は要素作業で構成され
要素作業は動作で構成されるという部分
例えば
『ペンを持ってくる』が要素作業の場合
『手を伸ばす』『つかむ』『持ってくる』
の3つの動作の組み合わせとなります
これを動作単位まで分割対象とすると
もう物理的におかしいですよね
Aさんが手を伸ばして
Bさんがつかんで
Cさんが持ってくる
なんてことは現実的に無理なわけです
そのため要素作業より細かい作業での
分割は考えないでおこうというものです
改善ポイント3:連合作業の分割
同一作業を2人以上で協力して行う作業は
できるだけ1人作業が可能となるように
作業分割を検討しましょう
ここはできるなら、という解釈でOKです
改善ポイント4:性質の異なる作業は分ける
重量作業と微細作業
熟練作業と単純作業 など
性質の異なる作業は分割が望ましいです
逆に言えば、よく似た作業は一緒が最適
ま、作業がやりやすくする方針です
理由は、作業者のリズムの違いや
治工具の合理的な配置の都合
さらには熟練者の有効活用面など
改善ポイント5:ライン外の作業の検討
ラインバランスを考えると
ラインの外で予め段取り作業をしておいて
複数個一括しての処理がベターな場合は
積極的に検討をしていきましょう
例えば、100個単位の梱包作業の場合
梱包箱を供給をしている間に小さなロスを
繰り返しているなら
もう予め梱包箱を準備しておいて
ライン作業中のロスをなくすなどを
考えたりしてくださいということです
ライン作業分析の重要改善ポイント!まとめ
改善案はまずは多ければ多いほどいいです
ひとつ思い付いて、これでいいやと
1案で決め打ちをするのではなくて
できるだけ多くのアイデアをリスト化して
それを比較検討して評価したうえで
最適案を選択することを鉄則として下さい
まずは量を生み出し
そこから質を生み出す
この2ステップは鉄板です
ぜひその進め方の大きな有効性も知って
改善できる組織へ成長していただきたい
そう思います
それでは今回はここまでです
今後とも宜しくお付き合いください☆
長文・乱文を最後まで読んでくださり
いつもありがとうございます♪
すべては御社の発展のために
すべてはあなたの笑顔のために