製造現場に携わるメンバーをまとめながら、品質目標を達成するのって、本当に大変です。
「いろいろ対処しているが、いまだ不良品が減らない理由がわからない…」 「ベテランと新人で仕上がりに差があることはあるけど…」 「おおよその原因はわかっているんだけど、どう改善すればいいか…」
こんな悩み、抱えていませんか?
実は、これらの悩みを解決するヒントは、「事実に基づく管理」 という考え方にあります。
「事実に基づく管理」って何かというと、カンや経験だけに頼るんじゃなくて、現場で集めたデータを使って、問題の本当の原因を突き止め、改善していく方法のこと。
「データを集める」って聞くと、難しそうに感じるかもしれません。
そこで今回は
- 「事実に基づく管理」を簡単に理解する方法
- 現場ですぐに使えるデータ収集のコツ
- データを分析して、問題解決に繋げるテクニック
などを、わかりやすく解説していきます。
ぜひ皆さまの職場の品質管理レベル向上のきっかけとして 今回も読み終えるまでのお時間、しばらくお付き合いくださいませ。
事実に基づく管理とは?
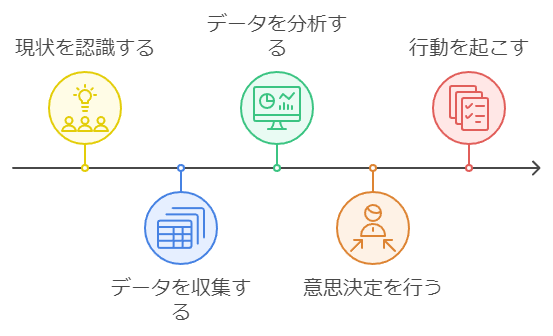
品質管理の基礎知識のキーワードとして、この「事実に基づく管理」という言葉が出てきます。でもこれってわかっているようでわからない状態のまま話を進めると、途中で理解不能になるかもしれませんので、この段階でしっかり押さえておきたいと思います。
事実に基づく管理の真意
「事実に基づく管理」を簡単に言うと、
「現場で起こっていることを、ちゃんとデータで把握して、より良い職場を作ろう!」
っていう考え方のことなんです。
具体的に言えば、
- 「この機械、最近よく止まるなぁ…」と感じたら、停止回数を記録してみる。
- 「新人のAさん、不良品が多いみたいだ…」と思ったら、Aさんの不良品率をデータ化してみる。
- 「どうやらある設備を使った時だけ、精度が変わるっぽい…」との噂を聞いたら、実際に製品を計測してリスト化してみる。
こうやって、だれかの**「感覚」** を鵜呑みにすることでなく、誰もが同じ認識を持てるよう 「数字」 に置き換えることで、問題点がハッキリ見えて共有できるものです。
「事実に基づく管理」を実践するための3つの条件
「事実に基づく管理」を成功させるには、次の3つの条件が大切です。
条件1:現場をよく観察する
まずは、自分の目で現場をよく観察することから始めましょう。
- どんな作業をしているのか?
- どんな問題が起こっているのか?
- どこを改善すれば、もっと良くなるのか?
五感をフル活用して、現場をしっかり見ることが重要です。
条件2:データを正しく集める
現場を観察したら、次はデータを集めましょう。
- 不良品の数は?
- 作業にかかる時間は?
- 機械の温度は?
データを集める時は、
- 「何を」「いつ」「どこで」「誰が」「どのように」 集めたのか
- なぜそのデータを集めるのか
を明確にしておくと、後から分析しやすくなります。
条件3:データに基づいて行動する
集めたデータを分析したら、次は行動!
- 不良品が多い原因がわかったら、対策を立てる。
- 作業効率が悪い工程を見つけたら、改善する。
データは、ただ集めるだけじゃ意味がありません。
分析結果に基づいて行動することで、初めて「事実に基づく管理」が活きてくるんです。
どうですか?
「事実に基づく管理」って、意外とシンプルだと思いませんか?
では次の章では、なぜ製造現場でデータを取る必要があるのか?について、さらに詳しく解説していきましょう。
製造現場がデータを取る3つの目的
さきほど説明したように「事実に基づく管理」を実践するには、データの存在が不可欠です。
では、製造現場ではどんな目的を意識しながらデータを取ればいいのでしょうか?大きく分けて、次の3つの目的があります。
目的1:管理のため
これは、工場の現状を把握し、安定した品質を維持するためのデータです。
「うちの工場、毎日どれくらい不良品が出てるんだろう?」 「この機械、平均どれくらいの時間で製品を作れるんだろう?」
といった疑問を解決するために、
- 不良率
- 生産時間
- 機械の稼働率
などを定期的に記録します。
これらのデータを記録することで、
- 問題が発生した時に、すぐに気づくことができる
- 早期に対策を打つことができる
- トラブルを未然に防ぐことができる
といったメリットがあります。
目的2:改善・進化のため
現状維持に満足せず、さらに品質や効率を向上させたい!
そんな時に役立つのが、改善・進化のためのデータです。
例えば、
- 「作業手順を変えたら、もっと効率が上がるんじゃないか?」
- 「材料を変えたら、品質が向上するんじゃないか?」
といった仮説を検証するために、
- 作業時間
- 不良品の種類
- 材料の特性
などのデータを収集・分析します。
目的3:検査のため
製品が規格や基準を満たしているかを確認するためのデータです。
- 製品のできあがった状態を検査
- 材料の品質をチェック
などを行い、合格かどうかを判断します。
検査のためのデータは、お客様に安心して製品を届けるために、とても重要です。
では、実際にどんな種類のデータを取ればいいのでしょうか?
製造業がとるべきデータの種類
製造現場で集めるデータには、どんな種類があるのでしょうか?
大きく分けて、次の3つの種類があります。
①数値データ(計量値)
計量値って何かというと、「測って得られるデータ」 のこと。
例えば、
- 製品の長さ(mm)
- 重さ(kg)
- 温度(℃)
- 時間(秒)
- 電流(A)
などが挙げられます。
これらのデータは、数字で表されるので、分析しやすいのが特徴です。
例えば、「ある製品の長さが、平均100mm、標準偏差2mm」といったデータがあれば、
- ほとんどの製品の長さは、98mm~102mmの範囲に収まっている
- 102mmを超える製品は、不良品として扱われる
といったことがわかります。
②数値データ(計数値)
計数値は、「数えて得られるデータ」 のことです。
例えば、
- 1日の不良品の数(個)
- 機械の停止回数(回)
- 作業者の人数(人)
- 月間の事故件数(件)
などが挙げられます。
これらのデータも、数字で表されるので、分析しやすいのが特徴です。
例えば、「ある工程の1日の不良品数が、平均5個」といったデータがあれば、
- 工程の改善によって、不良品数を3個に減らすことができた!
- 新しい機械を導入したら、不良品数が8個に増えてしまった…
といった変化を把握することができます。
③言語データ
言語データは、「言葉で表されるデータ」 のことです。
例えば、
- 作業者の意見や感想
- お客様からのクレーム内容
- 製品に対する評価(「使いやすい」「壊れやすい」など)
などが挙げられます。
言語データは、数値データのように計算することはできませんが、
- 問題の原因を探るヒント
- 改善のアイデア
などを得られる貴重な情報源となります。
例えば、「この製品は使いにくい」というお客様の声が多ければ、
- なぜ使いにくいのか?
- どうすれば使いやすくなるのか?
といった点を、さらに詳しく調査する必要があるでしょう。
このように、製造現場で集めるデータには、様々な種類があります。
それぞれのデータの特徴を理解して、適切な方法で収集・分析することが、「事実に基づく管理」の第一歩です。
データを収集する時の3つの注意点
データを集めることは、「事実に基づく管理」の第一歩ですが、闇雲に集めればいいってものではありません。
より正確で、役に立つデータを集めるために、以下の3つの注意点を押さえておきましょう。
注意点①:適切な特性値を選ぶ
「特性値」って聞き慣れない言葉かもしれませんが、簡単に言うと 「何を測るか」 ということです。
例えば、
- 製品の品質を調べたいなら、長さ、重さ、強度 などを測る
- 機械の調子を調べたいなら、温度、振動、稼働時間 などを測る
といった具合です。
目的によって、測るべき特性値は異なります。
適切な特性値を選ばないと、
- 必要な情報が得られない
- 分析がうまくいかない
といったことになりかねません。
注意点②: 5W1Hを明確にしておく
データを集める時は、「いつ」「どこで」「誰が」「何を」「なぜ」「どのように」 集めたのかを、きちんと記録しておくことが重要です。
例えば、
- いつ:2024年10月20日
- どこで:A工場の第1ライン
- 誰が:C班の作業者
- 何を:製品の重量
- なぜ:重量のバラつきが品質に影響している可能性があるため
- どのように:デジタルスケールを使用して測定
といった感じです。
5W1Hを明確にしておくことで、
- データの信頼性が高まる
- 後から分析する際に役立つ
といったメリットがあります。
注意点③:区分してデータをとる
データを区分して集めることで、より詳細な分析が可能になります。
例えば、不良品が発生した場合、
- 機械別
- 作業者別
- 時間帯別
- 材料別
などに分けてデータを収集することで、不良品発生の真の原因に迫りやすくなります。
このように、データを区分して集めることを 「層別」 といい、「事実に基づく管理」において非常に重要なテクニックです。
これらの注意点を意識することで、より質の高いデータを集め、効果的に分析を進めることができます。
データとバラツキ
同じ製品を、同じように作っているつもりでも、完成した製品には必ずバラツキが生じます。
例えば、同じ長さの棒を100本作っても、1本1本を精密に測ってみると、微妙に長さが違っていたりしますよね?
このバラツキは、一体なぜ生まれるのでしょうか?
5M1Eで生まれるバラツキ
製造現場におけるバラツキの原因は、大きく分けて以下の6つに分類されます。
要因 | 内容 |
---|---|
人 (Man) | 作業者の経験、スキル、体調、集中力などによってバラツキが生じる。 |
設備 (Machine) | 機械の精度、経年劣化、調整のズレなどによってバラツキが生じる。 |
材料 (Material) | 材料の品質、ロットの違い、保管状態などによってバラツキが生じる。 |
方法 (Method) | 作業手順、作業環境、作業標準の遵守状況などによってバラツキが生じる。 |
測定 (Measurement) | 測定器の精度、測定方法、測定者の熟練度などによってバラツキが生じる。 |
環境 (Environment) | 温度、湿度、照明、騒音など、周囲の環境によってバラツキが生じる。 |
製造現場におけるバラツキの原因は、作業者に関わる「人」、設備や工場環境の状態に関わる「設備」、材料やアイテムの質に関わる「材料」、作業方法ややり方に関わる「方法」、測定方法に関わる「測定」、周囲の環境に関わる「環境」の6つに大きく分けられ、これらを5M1Eと呼びます。 これらの要因が複雑に絡み合って、製品のバラツキを生み出しているんです。
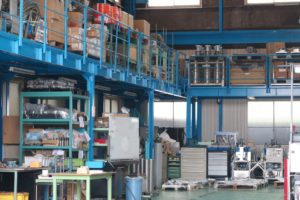
偶然原因によるバラツキ=避けられないバラツキ
どんなに注意深く作業しても、どうしても避けられないバラツキがあります。
例えば、
- 機械のわずかな振動
- 材料の微細な違い
- 測定時のわずかな誤差
などは、完全に無くすことは難しいですよね?
このような、避けられない原因によって生じるバラツキ を 「偶然原因によるバラツキ」 といいます。
異常原因によるバラツキ=避けられるバラツキ
一方、注意すれば避けられるバラツキもあります。
例えば、
- 機械の故障
- 作業者のミス
- 作業手順の間違い
- 材料の不良
などは、きちんと管理すれば防ぐことができますよね?
このような、原因を取り除くことで避けられるバラツキ を 「異常原因によるバラツキ」 といいます。
「事実に基づく管理」では、この 「異常原因によるバラツキ」 を見つけ出し、対策を立てることが重要になります。
バラツキの原因を突き止めるためには、データ分析が欠かせません。
次は、データ分析の際に注意すべき「誤差」について解説していきます。
データとその誤差
さて、データを集めて分析する際に、気をつけないといけないことがあります。
それは、「誤差」の存在です。
誤差って聞くと、「ミス」みたいなイメージを持つかもしれませんが、そうじゃないんです。
どんなに注意深くデータを集めても、どうしても避けられない誤差ってのが存在するんですね。
サンプリング誤差
例えば、不良品率を調べたいとします。
全部の製品を検査できれば正確な不良品率がわかりますが、時間もコストもかかってしまいますよね?
そこで、一部の製品だけを抜き取って検査することが多いと思います。
これを サンプリング=抜取検査 といいます。
でも、抜き取った製品がたまたま良品ばかりだったら、実際の不良品率よりも低く出てしまいますよね?
逆に、たまたま不良品ばかりだったら、高く出てしまいます。
このように、サンプルの選び方によって生じる誤差を サンプリング誤差 といいます。
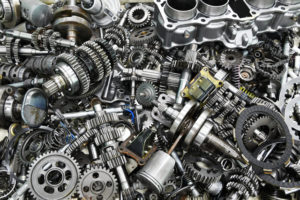
測定誤差
製品の長さを測る時、ノギスを使いますよね?
でも、ノギスの目盛りを「ちょっと甘く」読んでしまったり、「厳しめに」読んでしまったりすることがあるかもしれません。
同じ人でも、毎回ピッタリ同じように測るのは難しいですよね?
また、ノギス自体にも、わずかな誤差があるかもしれません。
このように、測定方法や測定器によって生じる誤差を 測定誤差 といいます。
誤差を理解してデータを扱う
これらの誤差を完全に無くすことは難しいですが、誤差があることを知っておくことが重要です。
「集めたデータには、多少の誤差が含まれているんだな」
ということを意識することで、データ分析の結果をより正確に解釈することができます。
例えば、
- 「不良品率が少し上がったけど、これは誤差の範囲かもしれないな」
- 「この測定値は、少し低く出ている可能性があるな」
といった具合です。
誤差を理解した上でデータを分析することで、より的確な判断を下し、効果的な対策を立てることができるようになります。
まとめ:データ収集・分析で進める製造現場の品質改善
さあ、ここまで「事実に基づく管理」について、一緒に考えてきました。
「データを集めるのって大変そうだな…」 「分析なんて難しそうで自分にできるのかな…」
そう不安視した方もいるかもしれません。
でも、実はこのデータ収集・分析は、決して難しいものではありません。
大切なのは、
- 「現場をよく観察する」
- 「データを正しく集める」
- 「データに基づいて行動する」
という3つのステップを踏むこと。
そして、
- 「どんな目的でデータを取るのか?」
- 「どんな種類のデータが良さそうなのか?」
- 「データには誤差がある」
ということを意識することです。
これらのポイントを押さえれば、誰でも簡単に「事実に基づく管理」を実践できます。
「事実に基づく管理」は、
- 不良品を減らす
- 品質を安定させる
- 作業効率を上げる
- チーム全体のスキルアップ
- 品質目標の達成
など、様々な効果をもたらします。
まさに、製造現場にとって、必須の考え方と行動と言えるでしょう。
なので、ぜひあなたも今日から「事実に基づく管理」を始めてください!
まずは、小さなことから
- 現場をじっくり観察して、気になるポイントを見つける
- 簡単なデータを集めて、並べたり整理したりしてみる
- 分析結果に基づいて、小さな行動を起こしてみる
この小さな一歩が、大きな変化を生み出す第一歩になります。