皆さんの工場では、在庫の山、どうなってますか?
「うちはスペースがないから、通路にも積み上げてるよ」
「部品が足りなくなるとラインが止まるから、どうしても多めに抱えちゃうんだよな」
正直、ないと困る気がするし、ありすぎても問題あるでしょうし、適正在庫の判断をどうやる?なんて考えると、なかなか悩ましい問題ですよね。
もちろん、在庫があることは安心感につながりますよね。「これでしばらくは大丈夫!」って。
でも…ちょっと一旦、立ち止まって考えてみてください。
その安心感、実は大きな落とし穴が待ち構えている可能性があります。
今回とりあげるのは世界一の自動車メーカー、トヨタ自動車。
トヨタの工場は、とにかく整理整頓が行き届いていて、無駄なものが一切ない、まさに理想の工場という感じです。
しかし、かつては通路にまで在庫が積み上げられ、 在庫管理に苦労していた時代があったんです。
え?それってホント?どんな風に悩んでいたのか、気になりますよね。
そこで今回は、そんなトヨタが過去の失敗から学び、 こだわりにこだわっている在庫の考え方、そして今日からあなたの現場で実践できる改善のヒントを、わかりやすく解説していきます。
今回も読み終えるまでのお時間、しばらくお付き合いくださいませ。
なぜトヨタは「在庫ゼロ」を目指したのか?:倒産寸前の危機からの脱却
誰もが知るトヨタ自動車。 世界一の自動車メーカーであるトヨタが、実は「在庫ゼロ」を目指していることは、意外と知られていません。
「え?あのトヨタが在庫ゼロ?まさか!」
そう思われた方もいるかもしれませんね。
確かに、在庫は「安心感」や「余裕」をもたらすもの。 「少し多めに持っておけば、いざという時も安心」 そう考えるのは自然なことです。
しかし、トヨタは「在庫は悪」と考えました。
なぜでしょうか?
倒産寸前の危機
実は、トヨタはかつて倒産寸前まで追い込まれたことがあったのです。
売上高は右肩上がりなのに、収益がまったく上がらず、むしろ赤字が膨らんでいきました。
この危機的な状況を脱するために、トヨタは徹底的に社内を調査しました。
すると、赤字の原因が「在庫」にあることに気づいたのです。
在庫が生み出す4つの問題点
- 場所の問題: 部品がたくさんあれば、当然保管場所が必要になります。数万点もある部品すべての在庫場所を確保するのは大変な負荷を生み出しているはずです。
- お金の問題: 在庫は購入費用がかかります。たくさん在庫を抱えれば、その分お金もかかります。
- 管理の問題: 在庫が増えれば、管理コストも膨らみます。誰が、何を、どれだけ持っているのか、把握するだけでも一苦労です。
- 品質の問題: 在庫が長期間倉庫に置かれたままになると、品質が劣化する可能性があります。また、売れ残った商品は処分しなければならず、費用がかかります。
ムダの根源
トヨタは、赤字になる問題点の根源にあるのは「在庫」そのものであると考えました。
つまり、在庫さえなければ、多くの問題が解決すると考えたのです。
そこで、トヨタは「トヨタ生産方式」という独自のシステムを開発し、徹底的にムダを排除し、効率的な生産を目指すようになった、というわけです。
ではその「トヨタ生産方式」とはどのようなものなのでしょうか?さらに説明を進めていきましょう。
トヨタ生産方式とは?:ムダを徹底的に排除する独自のシステム
トヨタ生産方式とは、ムダを徹底的に排除し、効率的な生産を目指すトヨタ独自のシステムです。
その中心にあるのが、「ジャストインタイム」という考え方です。
ジャストインタイム:必要なものを、必要な時に、必要なだけ作る
ジャストインタイムとは、「必要なものを、必要な時に、必要なだけ作る」という考え方です。
つまり、「停滞する在庫をゼロ化する」ということです。
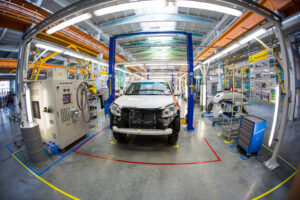
なぜジャストインタイムが重要なのか?
ジャストインタイムは、在庫を極限まで減らすために重要な考え方です。
在庫は、保管場所や管理コストがかかるだけでなく、品質劣化や売れ残りのリスクも抱えてしまいます。
そこでトヨタは「ジャストインタイムを追求すること」で、これらのムダを排除し、効率的な生産を実現しようとしたわけです。
トヨタ生産方式のその他の要素
トヨタ生産方式は、ジャストインタイムだけでなく、「自働化」や「かんばん方式」、「多能工化」など、様々な要素で構成されています。
- 自働化: 不良品が出たらラインを自動で停止させることで、品質管理を徹底する
- かんばん方式: かんばんを使って、必要なものを、必要な時に、必要なだけ供給する
- 多能工化:誰かが1つの仕事だけを担当するのでなく、誰もが多くの仕事をこなせるようにして、生産の柔軟性を高めてものの停滞をなくす
これらの要素が組み合わさることで、トヨタ生産方式は世界トップレベルの効率性を実現しています。
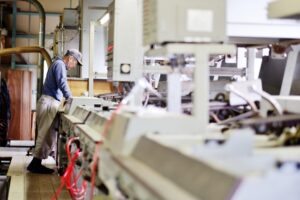
トヨタの挑戦:在庫ゼロへの道のり
トヨタは、ジャストインタイムを実現するために、様々な困難を乗り越えてきました。
部品の調達先の協力を得たり、生産ラインの改善を行ったり、従業員の意識改革を行ったり。
その過程は、まさに「常識を覆した挑戦」と言えるでしょう。
あのトヨタ自動車が倒産寸前まで追い込まれた:売上増と赤字増の奇妙な現象
トヨタ自動車は、高度成長期に売上高が右肩上がりに伸びていました。 しかし、その一方で、赤字も同じように膨らんでいったのです。
「売れているのに、なぜ赤字が増えるんだ?」
経営陣は頭を抱えました。 やはり当時のトヨタの経営陣も、売上が増えれば利益も増えるはずだと考えていました。 しかし、実際にはそのとおりにならず、なぜか当時はその常識が通用しませんでした。
そして、とうとう銀行口座にはお金がなくなっていき、倒産寸前まで追い込まれたのです。
あのトヨタでさえ、そんな時期があったのは驚きですよね。
そこで、トヨタは徹底的に社内を調査しました。 そして、その原因が「在庫」にあることを突き止めたのです!
調査で判明した在庫の甚大な悪影響
当時のトヨタは、「売れるものはどんどん作っておこう」という考え方でした。 そのため、「売れるものをどんどん作る」ようにと、売れる見込みのある製品を大量に生産し、完成品や仕掛品、さらには関連するすべての部品を倉庫に保管していました。
しかし、この過剰な在庫が、様々な問題を引き起こしていたんです。
在庫がもたらす4つの悪影響
- 保管スペース問題: 製品や部品の在庫を保管するための広大なスペースが必要になります。 倉庫の維持費や管理費もかさみます。
- 資金繰り悪化: 在庫はお金そのものです。 売れる前に在庫を抱えすぎると、その分の部品や材料を買うためのお金が必要になり、どんどんとお金がなくなって資金繰りが悪化し、経営を圧迫します。
- 管理コスト増大: 在庫が増えれば、管理コストも増大します。 在庫を置く倉庫代、在庫を出し入れするフォークリフトの人件費や車両費、たくさんの在庫を把握したり管理するシステム費用やその保守費などに、在庫が存在する分それだけ多くの人手と費用がかかります。
- 品質劣化・売れ残りリスク: 在庫が長期間倉庫に置かれたままになると、品質が劣化する可能性があります。 また、売れ残った商品は処分しなければならず、損失を招きます。
常識の逆転:在庫は「宝」ではなく「負債」
トヨタは、これらの問題点から、「在庫は宝ではなく負債である」という結論に至りました。
売れる見込みで大量に作った在庫も、売れなければただの不良在庫です。 保管スペースを圧迫するだけでなく、品質が劣化すれば価値は下がり、最悪の場合は廃棄処分となります。
つまり、在庫は多ければ多いほど安心というわけではなかった、ということに気づいたのです。
トヨタが恐れたのは「在庫」による生まれる膨大なムダ
今回は、トヨタが倒産寸前まで追い込まれた原因が「在庫」にあったことを解説しました。
売上高が伸びても利益が出ない、むしろ赤字が増えるという状況は、当時のトヨタにとって深刻な危機でした。
トヨタは、在庫がもたらす様々な問題点に気づき、「在庫は宝ではなく負債である」いう考え方を確立しました。
この危機感が、後のトヨタ生産方式へとつながっていくのです。
トヨタ流「ムダ取り」の極意:現場から生まれた改善の哲学
トヨタは、過剰な在庫がもたらす様々な問題点を認識し、「ムダ取り」という考え方を徹底することで、在庫を減らしてきました。
ムダ取りとは?:価値を生まないものを排除する
ムダ取りとは、「価値を生まないもの」を徹底的に排除するという考え方です。
トヨタは、製造現場におけるあらゆるムダを徹底的に洗い出し、排除することで、必要なものだけを、必要な時に、必要なだけ作れるようにしました。

ムダの種類:7つのムダ
トヨタは、現場におけるムダを以下の7種類に分類しました。
- 動作のムダ: 移動距離や作業動作の無駄を減らす
- 待ちのムダ: 材料や部品の到着を待つ、機械の停止を待つなどの待ち時間を減らす
- 不良品のムダ: 不良品の発生を減らし、手直しや廃棄のコストを削減する
- 過剰生産のムダ: 必要以上のものを作りすぎない
- 運搬のムダ: 材料や部品の運搬距離や回数を減らす
- 在庫のムダ: 必要以上の在庫を持たない
- 加工のムダ: 不要な加工や工程を省く
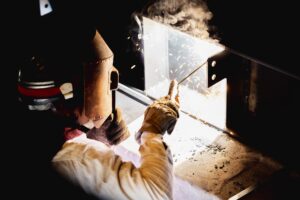
ムダ取りの3つの極意
トヨタは、これらのムダを徹底的に排除するために、以下の3つの極意を実践しました。
極意1:現状の把握
まずは、現状を徹底的に把握することから始めました。
現場を歩き回り、どこにムダが潜んでいるのか、何が問題なのかを徹底的に観察しました。
極意2:改善の繰り返し
ムダを見つけたら、すぐに改善に取り組みました。
改善策を実行し、効果を検証し、さらに改善を加える。
このPDCAサイクルを繰り返すことで、ムダを徹底的に減らしていきました。
極意3:全員参加
ムダ取りは、一部の担当者だけでなく、現場の全員が参加して行われました。
現場の一人ひとりが問題意識を持ち、改善提案を行うことで、より効果的なムダ取りが進みました。
ムダ取りは「カイゼン」
トヨタのムダ取りは、「カイゼン」と呼ばれています。
カイゼンとは、「日々、少しずつ、改善を重ねる」という意味です。
トヨタは、カイゼンを繰り返すことで、世界トップレベルの効率的な生産体制を構築しました。
ではそんなムダ取りによって、どんなよいことが生まれていったのか?在庫ゼロがもたらす絶大なるメリットについて解説します。
在庫ゼロがもたらす絶大なる5つのメリット:トヨタが手にした成功の果実
トヨタは、「ムダ取り」を徹底することで、在庫を極限まで減らすことに成功しました。 そして、在庫ゼロ(に近い状態)を実現することで、様々な絶大なメリットを手に入れました。
メリット1:コスト削減:利益を生み出す源泉
在庫をゼロにすることの最大のメリットは、コスト削減です。
- 保管スペース削減: 在庫を保管するための広大な倉庫が不要になります。
- 管理コスト削減: 在庫管理に必要な人件費やシステム費用を削減できます。
- 品質劣化防止: 在庫が長期滞留することによる品質劣化を防ぎ、廃棄コストを削減できます。
これらのコスト削減は、利益を直接的に押し上げる要因となります。
メリット2:リードタイム短縮:顧客満足度向上
在庫が少ないほど、注文から納品までの時間(リードタイム)を短縮できます。
リードタイムが短縮されれば、顧客への迅速な納品が可能となり、顧客満足度が向上します。
メリット3:品質向上:不良品発生リスクの低減
在庫が少ないほど、不良品が発生するリスクを減らすことができます。
なぜなら、在庫が多いほど、不良品が混ざってしまう可能性が高まるからです。
また、製造工程の改善も進みやすくなり、品質向上につながります。
メリット4:資金繰り改善:経営安定化
在庫はお金そのものです。 在庫を抱えすぎると、資金繰りが悪化し、経営を圧迫する可能性があります。
在庫を減らすことで、資金繰りが改善され、経営が安定します。
メリット5:柔軟性向上:変化への対応力
在庫が少ないほど、市場の変化や顧客のニーズに柔軟に対応できます。
例えば、新しい製品を開発する場合、既存の在庫を処分する必要がありません。
また、生産計画の変更も容易になり、変化への対応力が高まります。
在庫ゼロはゴールではなくスタート
トヨタは、在庫ゼロを達成することで、コスト削減、リードタイム短縮、品質向上、資金繰り改善、柔軟性向上など、様々なメリットを手に入れました。
しかし、在庫ゼロはゴールではありません。 トヨタは、常に改善を続け、より効率的な生産体制を目指す大切さに気付き、そして今も改善を継続している企業文化を持つことになったのです。
なるほど、それで世界で名をとどろかせるまで強い会社になったのですね。納得です。
では実際にトヨタが在庫ゼロを達成するために、どのような困難を乗り越えてきたのか、その改善物語に迫ります。
トヨタの改善物語:常識を覆した挑戦 – 困難を乗り越え、世界を変えた
トヨタが「在庫ゼロ」を目指す道のりは、決して平坦ではありませんでした。 そこには、数々の困難が待ち受けていました。
生産ラインの改善:ムダを徹底的に排除
トヨタは、生産ラインの徹底的な改善を行いました。
動作のムダ、待ちのムダ、不良品のムダなど、あらゆるムダを排除することで、効率的な生産ラインを構築しました。
しかし最初はこの対応は高い技術を持つ職人たちには理解されず、まったくと言っていいほど進めることができなかったといいます。しかし狙ってる方向性を根気よく説明し、徐々に効果が表れるまでには相当時間がかかったと言われています。
この改善活動は、カイゼンと呼ばれ、トヨタの企業文化として根付いています。
従業員の意識改革:全員参加の改善活動
このカイゼンを根付かせるため、トヨタは従業員の意識改革にも取り組みました。
在庫削減は、一部の担当者だけでなく、現場の全員が問題意識を持ち、改善提案を行うことで、より効果的に進みます。
トヨタは、従業員一人ひとりの意識改革を促し、全員参加の改善活動を推進しました。
部品調達先の協力:サプライヤーとの信頼関係構築
そしてもっとも苦労したのはジャストインタイムの導入でした。
トヨタは、このジャストインタイムを実現するために、部品の調達先の協力が不可欠です。
しかしどう考えても「必要な時に、必要なだけの部品を納入してもらう」スタイルは、一方的にトヨタにだけメリットを追求しているように見えます。
しかし実際にムダを徹底的に排除するためには、サプライヤーの工場商流のすべてにおいて「必要な時に、必要なだけの部品を納入」してもらわないと意味がありません。そのためサプライヤーとの強固な信頼関係を築き、こちらも根気よく説明していく必要がありました。
トヨタは、サプライヤーとの緊密なコミュニケーションを図り、相互理解を深めることで、この課題を克服しました。
常識との戦い:前例のない挑戦
トヨタの在庫ゼロへの挑戦は、まさに「常識との戦い」でした。
当時、「在庫は多い方が安心」という考え方が一般的でした。
トヨタのやり方は、前例のない挑戦であり、周囲からは 懐疑的な目で見られていました。
しかし、トヨタは諦めませんでした。「必ずできる」という強い信念を持ち、改善を続けたのです。
すごい執念ですよね。
世界への影響:製造業のスタンダード
トヨタの改善活動は、世界中の製造業に大きな影響を与えました。
トヨタ生産方式は、「リーン生産方式」として世界中で採用され、製造業のスタンダードとなりました。
トヨタの改善物語は、多くの製造業に勇気と希望を与えました。
そしてこのトヨタ生産方式はアメリカで「ザ・ゴール」という書籍であらゆる事業モデルのお手本とされ、日本語訳を作るな、と号令が出たほどなんだとか。
現在ではもう日本語訳も解禁になっていますので、ものづくり企業に関係しているなら一度は読んでみることをオススメします。
トヨタの挑戦はまだまだ続く
今回は、トヨタが在庫ゼロを達成するために、どのような困難を乗り越えてきたのか、その改善物語を紹介しました。
トヨタは、部品調達先の協力、生産ラインの改善、従業員の意識改革、そして常識との戦いを乗り越え、世界トップレベルの効率的な生産体制を構築しました。
しかし、トヨタの挑戦はまだ終わっていません。 常に改善を続け、より効率的な生産体制を目指そうと努力しています。
ではそんなトヨタの「在庫ゼロ」の考え方を、中小製造業の現場でどのように活用できるのでしょうか、具体的なヒントをお届けしましょう。
我々、中小製造業が今日から取り組むべきこと:小さな一歩が未来を変える
トヨタの「在庫ゼロ」の考え方は、決して大企業だけの特別なものではありません。 中小製造業の現場でも、今日からできることはたくさんあります。
取り組むべきこと1:まず、身の回りのムダを見つける
トヨタの「ムダ取り」は、小さなことから始まりました。 まずは、自分の周りのムダに目を向けてみましょう。
- 工具を探すムダ: 工具の置き場所を決め、整理整頓を徹底する
- 移動のムダ: よく使うものを手の届く範囲に置く
- 待ちのムダ: 材料や部品が届くまでの待ち時間を有効活用する
- 書類作成のムダ: 不要な書類や手続きを省く
これらのムダを一つずつ改善していくことで、時間や労力を節約することができます。
取り組むべきこと2:5S活動を徹底する
5S活動とは、整理・整頓・清掃・清潔・習慣(しつけ)の頭文字をとったものです。
5S活動を徹底することで、ムダを減らし、安全で働きやすい職場を作ることができます。
- 整理: 不要なものを処分する
- 整頓: 必要なものを使いやすい場所に置く
- 清掃: 汚れを落とし、きれいな状態を保つ
- 清潔: 不要なものが生まれない、乱れない、汚れないための未然防止策を考える
- 習慣(しつけ): 清潔で決めた未然防止策を徹底する
5S活動は、改善の基本であり、すべての活動の土台となります。
取り組むべきこと3:チームで取り組む
ムダ取りは、個人で抱え込むのではなく、チームで取り組むことが重要です。
現場の一人ひとりが問題意識を持ち、チームで協力して改善策を検討することで、より効果的なムダ取りが進みます。
- チームで目標設定: チーム全体で達成すべき目標を設定することで、共通認識を持つ
- 情報共有: ムダに関する情報を共有し、改善策を検討する
- 役割分担: それぞれの得意分野を活かし、役割分担して改善活動を進める
- 進捗確認: 定期的に進捗状況を確認し、改善点を見つける
チームで取り組むことで、個人のアイデアだけでは思いつかない斬新な改善策が生まれることもあります。
小さな一歩が大きな成果を生む
トヨタの「在庫ゼロ」は、一朝一夕に達成されたものではありません。 日々の積み重ねによって、少しずつ改善を重ねてきた結果です。
私たち中小製造業も、焦らず、諦めずに、小さなことから始めましょう。 小さな一歩が、大きな成果を生み出すことを信じていきましょう。
我々、中小製造業が今日から、できること
今回は、中小製造業が今日から取り組むべきこととして、ムダを見つける、5S活動を徹底する、チームで取り組む、という3つのポイントを紹介しました。
これらの活動は、決して難しいことではありません。 少しの意識改革と行動によって、誰でも実践することができます。
ぜひ、今日からできることを始め、より効率的で、働きやすい現場を作っていきましょう。
まとめ:トヨタが「在庫ゼロ」を目指した本当の理由
トヨタが「在庫ゼロ」を目指した本当の理由、それは「生き残るため」でした。 売上高が右肩上がりでも、利益が出なければ会社は倒産します。 トヨタは、在庫がもたらす様々な問題点に気づき、ムダを徹底的に排除することで、危機を脱しました。
そして、その過程で得た教訓は、どんな規模の製造業にも当てはまる普遍的なものです。
「うちの会社は小さいから、トヨタのようにはできない」 「ウチは職人の技が大事だから、効率化なんて…」
そんな風に思われた方もいるかもしれません。
でも、本当にそうでしょうか?
トヨタの「ムダ取り」は、決して特別なことではありません。 どんな現場でも、どんな製品を作っていても、必ずムダは存在します。
大切なのは、「ムダに気づくこと」、そして「改善を続けること」です。
この記事を読んだあなたは、もう「ムダ」の存在に気づいてしまったはずです。 あとは、行動あるのみです。
まずは、身の回りの小さなムダから見つけてみましょう。 そして、チームで協力して、少しずつ改善を重ねていきましょう。
改善活動は、決して楽ではありません。 時には、壁にぶつかることもあるでしょう。
しかし、諦めずに続けることで、必ず成果は現れます。
トヨタがそうだったように、あなたの現場も、必ず変わります。
この記事が、あなたの現場が変わるきっかけとなることを願っています。
さあ、今日から、あなたも「ムダ取り」を始めましょう!