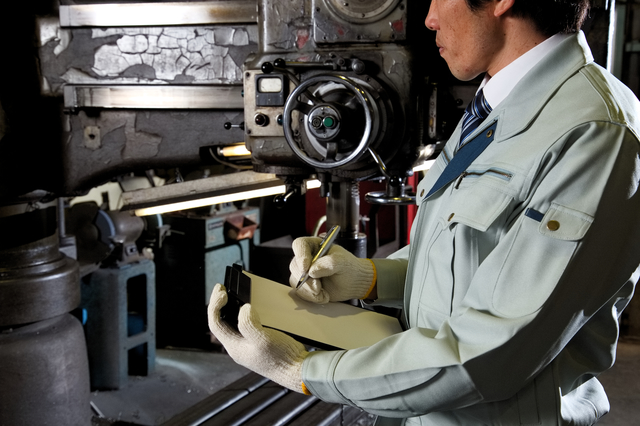
「あれ?また同じミスしちゃったよ…」



「この間も同じこと言われたのに、なんで忘れちゃうんだろう…」
現場ではこんな葛藤が生まれ勝ちですよね。
毎日、たくさんの製品を作る製造現場。
誰だってちゃんとしたいし、注意しているはずなのに、生まれてしまうミス。
一つ一つの作業は単純に見えても、ちょっとした気の緩みや思い込みで、起ってしまうミスってなかなか減りませんよね。
「注意一秒、ケガ一生」なんて言いますが、品質だって同じです。たった一つのミスが、大きなクレームや損害につながることも…。
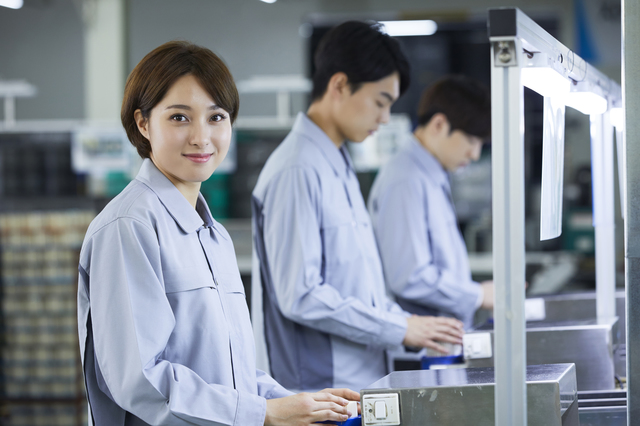
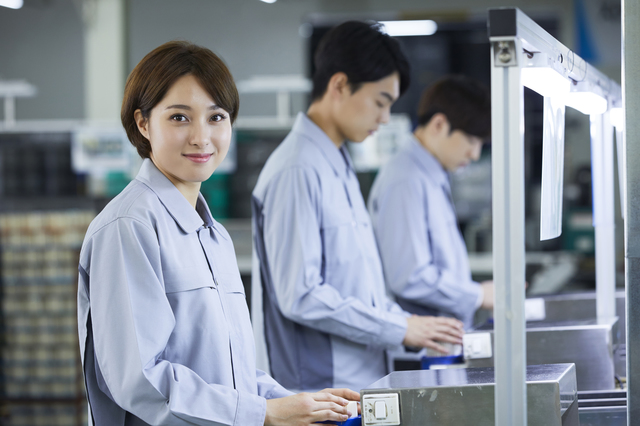
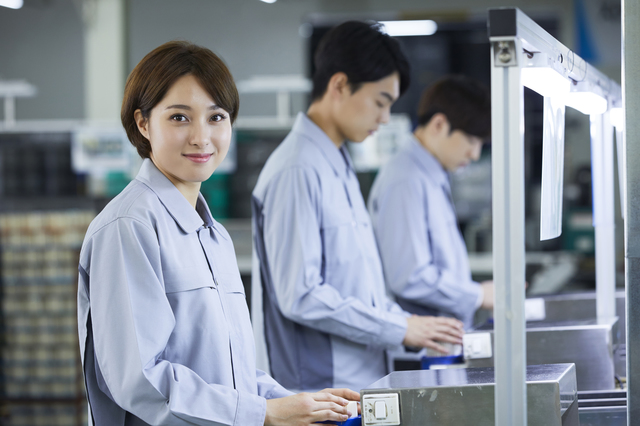
「分かっちゃいるけど、なかなかミスが減らないんです!」
多くのそんな現場の声は実際に多いものです。
そんな皆さんにぜひ知ってほしいのが、今回ご紹介する「品質管理チェックリスト」です!
「え?チェックリスト?そんなの、もうやってるよ!」
そう思った方もいるかもしれません。でも、ちょっと待ってください!
皆さんが使っているチェックリスト、本当に現場で役立っていますか?
- 項目が多すぎて、チェックするのが面倒…
- 専門用語ばかりで、新人さんには分かりにくい…
- 作っただけで、全然見直していない…
もし、こんな状態なら、せっかくのチェックリストが宝の持ち腐れになっているかもしれません。
今回のブログでは、現場で本当に役立つ「品質管理チェックリスト」の作り方と、その効果について、分かりやすく解説していきます。
難しい専門知識は一切不要!今日からすぐに使える、簡単なテンプレートもプレゼントしちゃいますね
では今回も読み終えるまでのお時間、しばらくお付き合いいただけますと幸いです。
なぜ現場に「品質管理チェックリスト」が必要なのか?
「よし、今日も一日頑張るぞ!」
朝礼で気合いを入れても、いざ作業が始まると、どうしてもミスは起きてしまうもの。
「あれ?この部品、どっち向きにつけるんだっけ…?」
「このネジ、何回締めればいいんだっけ…?」
ベテランだって、新人だって、人間ですから、うっかり忘れてしまったり、勘違いしてしまうこと、ありますよね。
でも、製造現場では、その「うっかり」が、大きな問題につながることがあります。
品質管理チェックリストの重要性
考えてみてください。
もし、たった一つのネジの締め忘れが原因で、製品が壊れてしまったら?
もし、ほんの少しの寸法違いで、製品が使い物にならなくなってしまったら?
お客様からの信頼を失うだけでなく、場合によっては、大きな損害賠償を請求されることだってありえます。
「たった一つ」のミスが、会社の信用を大きく傷つけてしまうかもしれないんです。
だからこそ、「品質管理チェックリスト」が重要になってくるんです。
チェックリストは、いわば「ミスの防止装置」。
作業のポイントを一つ一つ確認することで、「うっかり」や「勘違い」を未然に防いでくれるんです。
チェックリストでミスを防ぐ効果とは?
「でも、チェックリストって、面倒くさいんだよな…」
そう思う気持ち、よく分かります。
でも、考えてみてください。
ミスをして、後で慌ててやり直したり、お客様に謝ったりする方が、よっぽど面倒くさくないですか?
チェックリストがあれば、
- 「あれ、何だっけ?」がなくなる!
- 作業手順が明確になるので、迷う時間が減り、作業効率がアップします。
- 「うっかりミス」が激減!
- 重要なポイントを見落とすことがなくなり、品質が安定します。
- 新人さんも安心!
- ベテランの知識や経験がチェックリストに詰まっているので、誰でも同じレベルの作業ができるようになります。
つまり、チェックリストは、現場の皆さんを「ミス」から守り、安心して仕事に取り組めるようにしてくれる、心強い味方なんです!
品質管理チェックリストとは?基本的な役割と活用法
「品質管理チェックリスト」って、言葉だけ聞くと難しそうに感じるかもしれません。
でも、実は、皆さんが普段から使っている「レシピ」や「旅行の持ち物リスト」と、基本的な考え方は同じなんです。
品質管理におけるチェックリストの位置付け
たとえば料理のレシピには、材料や手順、火加減などが細かく書かれていますよね。
これを見ながら作れば、誰でもある程度のレベルの料理を作ることができます。
また、旅行の持ち物リストがあれば「あれ、歯ブラシ持ってきたっけ…?」なんて出発前に慌てることもありません。
品質管理チェックリストも、これらと同じ。
製品を作るための「レシピ」であり、「忘れ物防止リスト」なんです。
品質管理の世界では、チェックリストは、製品の品質を一定に保つための「道しるべ」のような存在です。
作業の抜け漏れを防ぎ、品質のバラツキをなくす。
これが、チェックリストの基本的な役割です。
現場での具体的な活用例
では、実際に、製造現場では、どのようにチェックリストを活用すれば良いのでしょうか?
例えば、こんな場面で役立ちます。
- 機械の始業点検
- 「油量は十分か?」「異音はしないか?」など、機械を安全に動かすための確認項目をリスト化。毎朝、チェックすることで、機械の故障を未然に防ぎます。
- 部品の取り付け作業
- 「ネジの種類は正しいか?」「締め付けトルクは適切か?」など、取り付け作業の注意点をリスト化。一つ一つ確認することで、取り付けミスをなくします。
- 製品の最終検査
- 「寸法は合っているか?」「傷や汚れはないか?」など、出荷前の最終確認項目をリスト化。不良品の流出を防ぎます。
これらのチェックリストは、作業の前に確認するだけでなく、作業中や作業後にも活用できます。
「あれ?これ、ちゃんとやったっけ…?」
と不安になった時、チェックリストを見返せば、すぐに確認できます。
つまり、チェックリストは、現場の皆さんの「記憶」をサポートし、安心して作業を進めるための、強力なツールなんです!
品質管理チェックリストを作成する5つのポイント
「よし、それならば、うちの現場もチェックリストを作ってみよう!」
そう思ったら、早速取り掛かりたいところですが、ただやみくもに項目を並べるだけでは、本当に役立つチェックリストは作れません。
ここでは、現場で「使える」チェックリストを作るための、5つの大切なポイントをお伝えします。
① 現場作業を具体的に洗い出す
まずは、現場の作業を「見える化」することから始めましょう。
「製品Aを作る」という作業を、
- 「材料を準備する」
- 「機械にセットする」
- 「加工する」
- 「検査する」
- 「梱包する」
…というように、細かく分解していきます。
この時、ベテランの作業をよく観察したり、直接話を聞いたりするのがポイントです。
「この作業、いつもどこでつまずく?」
「特に注意していることは何?」
こういった質問をすることで、隠れた注意点やコツが見えてくるはずです。
② 作業手順を標準化する
作業を洗い出したら、次は、その手順を「標準化」します。
「標準化」なんて言うと難しそうですが、要は「誰がやっても同じ結果になるように、作業のやり方を決める」ということです。
例えば、「ネジを締める」という作業一つとっても、
- 「どのネジを、どの順番で締めるのか?」
- 「どれくらいの力で締めるのか?」
といったことを、具体的に決めておく必要があります。
こうすることで、作業のバラツキをなくし、品質を安定させることができます。
③ 項目はシンプルかつ明確にする
チェックリストの項目は、できるだけシンプルに、そして明確にしましょう。
例えば、「ネジをしっかり締める」ではなく、
「ネジAを、トルクレンチで5N・mの力で締める」
というように、具体的な数値や道具を指定すると、誰が見ても分かりやすいですよね。
また、一つの項目に複数の作業を含めないことも大切です。
「部品Aと部品Bを取り付け、ネジで固定する」
ではなく、
- 「部品Aを取り付ける」
- 「部品Bを取り付ける」
- 「ネジで固定する」
と分けた方が、チェック漏れを防ぐことができます。
④ 誰でも理解できる表現にする
チェックリストは、ベテランだけでなく、新人さんや、時には外国人スタッフが見ることもあります。
だからこそ、専門用語や難しい言葉は避け、誰でも理解できる表現を心がけましょう。
例えば、「カシメる」ではなく、「つぶして固定する」と言い換えるなど、現場で普段使っている言葉を使うのがおすすめです。
必要であれば、写真やイラストを添えるのも良いでしょう。
⑤ 継続的に見直し・改善を行う
チェックリストは、一度作って終わりではありません。
実際に使ってみて、
「この項目、分かりにくいな…」
「この作業、順番を変えた方が効率的だな…」
と感じたら、どんどん修正していきましょう。
また、新しい設備を導入したり、作業手順が変わったりした時も、必ずチェックリストを見直すようにしてください。
チェックリストは、現場の「成長」に合わせて、常に進化させていくことが大切です。
【現場ですぐ使える!】品質管理チェックリストの簡単テンプレート例
「理屈は分かったけど、やっぱりチェックリストを作るのって面倒だな…」
そんな皆さんのために、今回は、現場ですぐに使える、簡単な品質管理チェックリストのテンプレートの例をご用意しました!
すぐに活用できる品質チェックリストのテンプレート例
今回紹介する品質管理チェックリストのテンプレートは、こんな感じです。
作業項目 | 確認内容 | チェック欄 | 備考 |
---|---|---|---|
材料の準備 | 材料A、材料B、材料Cが揃っているか? | □ | 不足の場合は、○○さんに連絡 |
機械の始業点検 | 油量は十分か? | □ | 規定値:○○~○○ |
部品Aの取り付け | ネジの種類は正しいか? | □ | 使用ネジ:M5×10mm |
部品Aの取り付け | 締め付けトルクは適切か? | □ | 規定トルク:5N・m |
製品の最終検査 | 寸法は合っているか? | □ | 許容誤差:±0.5mm |
製品の最終検査 | 傷や汚れはないか? | □ | 目視で確認 |
これはあくまで一例ですが、皆さんの現場に合わせて、自由にカスタマイズしてください。
テンプレートの具体的な使い方とカスタマイズ方法を解説
このテンプレートの使い方は、とっても簡単です!
- エクセル上で作表する: まずは、上記の例を参考にしてExcel上で作表してみてください。
- 作業項目の入力: 「作業項目」の列に、皆さんの現場の作業内容を、順番に入力していきます。
- 確認内容の入力: 「確認内容」の列には、各作業でチェックするべきポイントを、具体的に記入します。(例:「ネジの締め忘れはないか?」、「寸法は規定値内か?」など)
- チェック欄の活用: 実際に作業をしながら、確認内容をチェックし、問題がなければ「チェック欄」に✓を入れます。
- 備考欄の活用: 「備考」欄には、注意点や、イレギュラーな場合の対応などをメモしておくと便利です。
カスタマイズのポイント
- 項目の追加・削除: 皆さんの現場に合わせて、項目を自由に追加・削除してください。
- 項目の並べ替え: 作業の流れに合わせて、項目の順番を並べ替えてください。
- 色の変更: 見やすいように、セルの色を変えてもOKです。
- 写真やイラストの追加: 必要に応じて、写真やイラストを追加すると、より分かりやすくなります。
このテンプレートを、ぜひ皆さんの現場で活用して、「ミスゼロ」の現場を実現してください!
品質管理チェックリスト導入で現場が変わった成功事例
「本当にチェックリストで、そんなに変わるの…?」
そう思っている方もいるかもしれませんね。
ここでは、実際に品質管理チェックリストを導入して、現場が劇的に変わった!という、中小製造業の成功事例を3つご紹介します。
中小製造業の現場での実践事例紹介①
A社(金属加工業):ベテランの勘に頼らない、新人でも安心の現場へ!
A社では、長年、ベテランの経験と勘に頼って、製品の品質を維持してきました。
しかし、ベテランの退職や、新人さんの増加により、品質のバラツキが目立つようになってきたんです。
そこで、A社は、思い切って品質管理チェックリストを導入!
各工程の作業手順を細かく洗い出し、チェックリストにまとめました。
すると…
- 新人さんでも、ベテランと同じレベルの作業ができるようになった!
- 作業の抜け漏れがなくなり、不良品の数が大幅に減少!
- ベテランは、新人さんの教育にかける時間が減り、より高度な作業に集中できるようになった!
まさに、一石三鳥の効果があったそうです。
中小製造業の現場での実践事例紹介②
B社(食品加工業):パートさんのミスを減らし、食品ロスを大幅削減!
B社では、パートさんが多く働いていますが、どうしても作業のミスが減らず、材料のロスが多いのが悩みでした。
そこで、B社は、パートさんでも分かりやすいように、写真やイラストをたくさん使ったチェックリストを作成。
各作業のポイントを、目で見て確認できるようにしたんです。
その結果…
- パートさんの作業ミスが激減!
- 材料のロスが大幅に減り、コスト削減に成功!
- パートさんの自信にもつながり、職場全体の雰囲気が明るくなった!
チェックリストが、パートさんの「心強い相棒」になったんですね。
中小製造業の現場での実践事例紹介③
C社(電子部品製造業):クレームゼロ!お客様からの信頼度が大幅アップ!
C社は、以前から品質管理には力を入れていましたが、それでも月に数件のクレームが発生していました。
原因を調べてみると、多くが「ヒューマンエラー」、つまり人為的なミスだったんです。
そこで、C社は、チェックリストを徹底的に見直し、より厳格なチェック体制を構築。
特に、検査工程のチェックリストを充実させ、不良品の流出を徹底的に防ぐようにしました。
すると…
- なんと、クレームがゼロに!
- お客様からの信頼度が大幅にアップし、新規の受注も増加!
- 社員の品質意識が高まり、現場全体のレベルアップにつながった!
チェックリストが、C社の「品質の番人」になったんですね。
チェックリスト活用前後での品質改善効果
これらの事例からも分かるように、品質管理チェックリストは、
- 不良品の削減
- 作業ミスの防止
- 作業効率の向上
- コスト削減
- 顧客満足度の向上
- 従業員教育の効率化
など、様々な効果をもたらします。
「うちの現場も、きっと変われる!」
そう感じていただけたのではないでしょうか?
チェックリスト運用時によくある問題と解決策
「よし、チェックリストを作ったぞ!これで完璧!」
…と、思っても、実際に運用してみると、いろいろな問題が出てくることがあります。
ここでは、チェックリスト運用時によくある問題と、その解決策について、一緒に考えていきましょう。
チェック漏れが起きる原因とその対策
「ちゃんとチェックしたはずなのに、後で見たら漏れがあった…」
チェックリスト運用で一番多いのが、この「チェック漏れ」です。
なぜ、チェック漏れが起きてしまうのでしょうか?
主な原因としては、
- チェックリストが形骸化している
- いつも同じ作業だから、と確認を怠ってしまう。
- チェック項目が多すぎる、または分かりにくい
- 面倒になって、適当にチェックしてしまう。
- 時間がない、忙しい
- 急いでいると、ついチェックを飛ばしてしまう。
などが考えられます。
これらの問題を解決するためには、
- 定期的な見直し
- チェックリストが形骸化しないように、定期的に内容を見直しましょう。
- 項目の整理・簡潔化
- 本当に必要な項目だけに絞り、分かりやすい表現にしましょう。
- チェックしやすい環境づくり
- チェックリストを現場の目立つ場所に掲示したり、作業の合間にチェックする時間を設けたりするなど、チェックしやすい環境を整えましょう。
- ダブルチェックの導入
- 重要な工程では、複数人でチェックする体制を作るのも有効です。
現場スタッフのモチベーションを維持する方法
「チェックリストは面倒くさい」「やらされ仕事」
現場スタッフから、こんな声が聞こえてくることもあります。
チェックリストを効果的に運用するためには、現場スタッフのモチベーションを維持することが、とても大切です。
そのためには、
- 目的を共有する
- 「なぜチェックリストが必要なのか?」「チェックリストを使うことで、どんな良いことがあるのか?」を、しっかりと伝えましょう。
- 意見を聞く
- 現場スタッフから、チェックリストに関する意見や提案を積極的に聞き、改善に取り入れましょう。
- フィードバックを行う
- チェックリストの運用状況を定期的にフィードバックし、良い点は褒め、改善点は一緒に考えましょう。
- ゲーム感覚を取り入れる
- チェックリストの達成度に応じて、ちょっとしたご褒美を用意するなど、ゲーム感覚を取り入れるのも効果的です。
- 感謝の気持ちを伝える
- 「いつもチェックしてくれてありがとう」と、感謝の気持ちを言葉で伝えることも大切です。
チェックリストは、やらされるものではなく、自分たちの仕事を楽にし、品質を高めるための「道具」です。
現場スタッフが、そう思えるように、積極的にコミュニケーションを取りながら、一緒にチェックリストを育てていきましょう。
まとめ:品質管理チェックリストで「ミスゼロ」の現場を実現しよう!
ここまで、品質管理チェックリストの作り方から、運用時の注意点、そして現場での成功事例まで、様々な角度からお話してきました。
「なるほど、チェックリストって、やっぱり大事なんだな」
「でも、うちの現場に合うチェックリストを作るのは、ちょっと大変そう…」
そう感じている方もいるかもしれません。
でも、大丈夫!
今日、皆さんに紹介した「簡単テンプレート例」を、まずは使ってみてください。
最初は、完璧なチェックリストでなくて簡単な内容でも良いんです。
まずは、現場の作業を思い浮かべながら、テンプレートの項目を埋めてみましょう。
そして、実際に使ってみて、
「ここは、もっとこうした方が分かりやすいな」
「この作業、チェック項目に追加した方が良いかも」
と、感じたことを、どんどん書き加えていってください。
そうやって、少しずつ、少しずつ、皆さんの現場に合った、独自に役立つチェックリストに育てていけば良いんです。
チェックリストは、「ミス」という見えない敵と戦うための、最強の武器です。
そして、その武器を使いこなせるのは、現場で働く皆さん自身です。
「ミスゼロ」の現場は、決して夢ではありません。
今日から、チェックリストという武器を手に、一緒に「ミスゼロ」の現場を目指して、力強く歩み始めましょう!
あなたの現場が変わる、その第一歩を、今日、踏み出してください!