やっぱり品質管理って、難しそうなイメージがあると思います。
でも実は、品質管理って、「ムダをなくして、お客様に喜んでもらうための、現場の知恵と工夫」 のことです。
例えば、不良が減れば、材料費や手直しの時間、お客様からのクレーム対応にかかるコストを減らせますし、なによりお客様に迷惑をかけるリスクが低くなります。
つまり、品質管理をしっかりやれば、お客さまを安心できるし、会社も儲かるし、現場の皆さんも気持ちよく働けるようになります。そう聞けば、そりゃ誰だってしっかりやりたい。けど、そのやり方も考え方もよくわからないですよね。
そこで今回は、品質管理の基本から、現場で今日からでも役立つ具体的な方法まで、わかりやすく解説していくこととしました。
特に、「つくる質と考える質との違い」「不良の種類と対策」「QC思考法の実践」など、現場で役立つ内容を意識して説明します。
なので今回も、読み終えるまでのお時間、しばらくお付き合いくださいませ。
品質管理がもたらす価値とは?
今回のテーマは「品質管理」です。品質管理に苦手意識を持っている方もいるかもしれませんが、実は、私たち中小製造業にとって、生き残りをかけた非常に重要な取り組みなのは、普段の緊張感から想像はつきますよね。
品質管理は「コスト削減」と「信頼獲得」の鍵
一般的に「品質管理」と聞くと、「検査を厳しくする」とか「不良品を出さないようにする」といった取り組みのイメージが強いですよね。もちろんそれらも大切な要素ですが、品質管理に取り組んだ結果、生み出される価値が多くのヒトが想像するより大きい、という現実があります。
実は品質管理に取り組むことによって、「コスト削減」と「信頼獲得」という、2つの大きな価値を生み出してくれます。それってそれぞれどういうことか?について説明していきましょう。
中小製造業ほど不良がもたらすロスやクレーム対応コストは大きい
私たち中小製造業は、大企業に比べて、人的リソースも資金も限られています。そんな中で、不良品をたくさん出してしまったり、お客様からクレームを受けたりすると、その挽回や要因調査や説明対応に追われ、本来やるべき仕事に手が回らなくなってしまいます。
また不良品を作り直すための材料費、人件費、そしてお客様への謝罪や返品対応にかかる時間…。これらはすべて、本来なら必要のない「無駄なコスト」ですよね。
品質管理を徹底することで、不良ロスの削減と顧客満足度の向上が可能
しかし、品質管理を徹底すれば、本来対応しなくてもよい「無駄なコスト」を大きく削減することができます。不良品が減れば、材料の無駄遣いがなくなり、作り直しの手間も省けます。お客様からのクレームも減り、信頼度が向上します。
お客様からの信頼を得られれば、継続的な取引につながり、新たな案件を相談してもらえる可能性も高まります。つまり、品質管理は、「コスト削減」と「売上アップ」の両方に貢献する、非常に重要な取り組みなのです。
でも、品質管理ってどういう取り組みなんでしょうか?よくわからない方もいらっしゃいます。そこでまずはその基本的理解からお話していきます。
品質管理の基本理解
ここでは、「品質」とは何か?という根本的な問いから、中小製造業が抱える課題、そして「設計品質」と「製造品質」という2つの重要な概念について、わかりやすく解説します。
品質とは何か?~定義から考える本質
まずは品質とは何か?その定義から本質的な意味を考えていきましょう。
品質の定義
「品質」という言葉は、普段何気なく使っていますが、改めて「品質って何?」と聞かれると、意外と答えるのが難しいものです。まずは、教科書的な定義から見ていきましょう。

小学館の日本大百科全書によると、品質とは「使用目的に応じた商品の(中略)実質的性能や消費に役だつ一定の機能」と定義されています。
…ちょっと堅苦しいですね。現場レベルで言い換えると、「お客様が求める機能を確実に満たすこと」 と言えるでしょう。
例えば、自動車の部品であれば、「決められた耐久性があるか」「高温や低温でも正常に動作するか」「安全基準を満たしているか」などが、お客様が求める機能です。これらの機能を確実に満たして、初めて「品質が良い」と言えるのです。
さらに言えば、「品質=顧客満足」 と言い換えることもできます。お客様が満足してくれれば、それが「良い品質」なのです。
なぜ品質管理が必要なのか:中小製造業が抱える課題
では、なぜ私たち中小製造業にとって、品質管理が重要なのでしょうか? それは、私たちが抱える「課題」と深く関係しています。
部署間の連携不足(営業と設計、設計と製造のコミュニケーションギャップ)
皆さんの会社では、営業、設計、製造の各部門が、うまく連携できていますか?
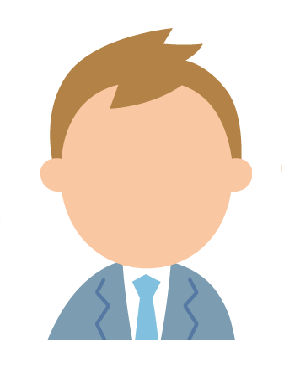
「お客様は、こんな機能を求めているよ!」
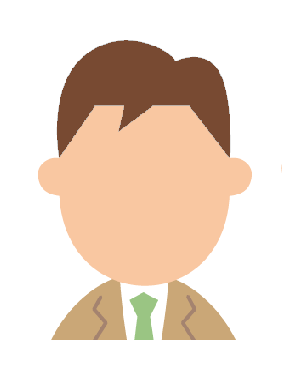
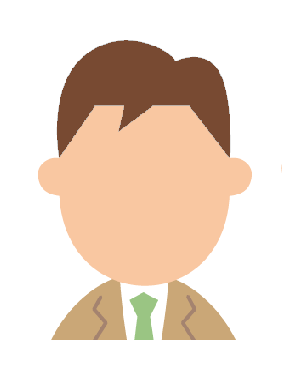
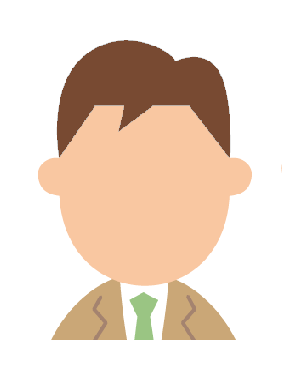
「よし、それなら、こんな設計にしよう!」
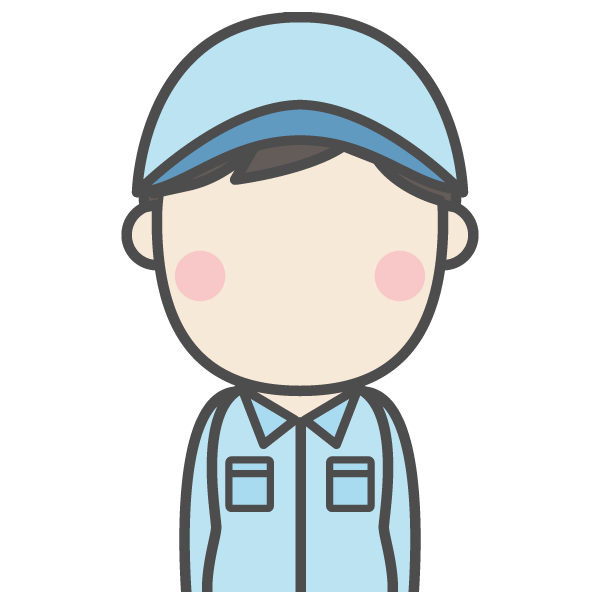
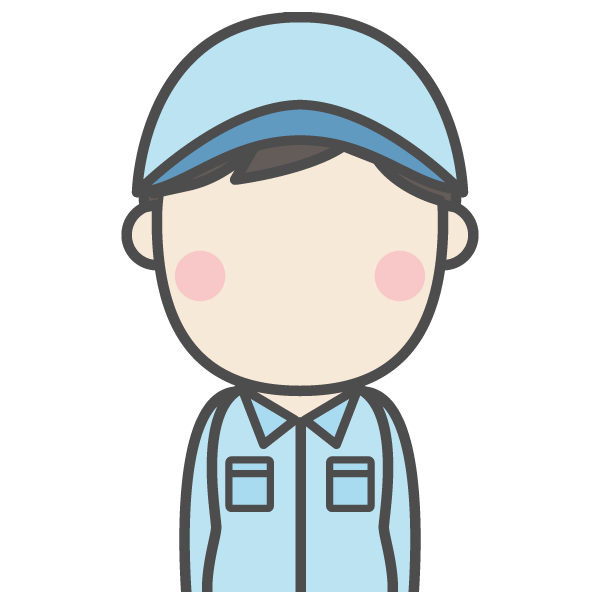
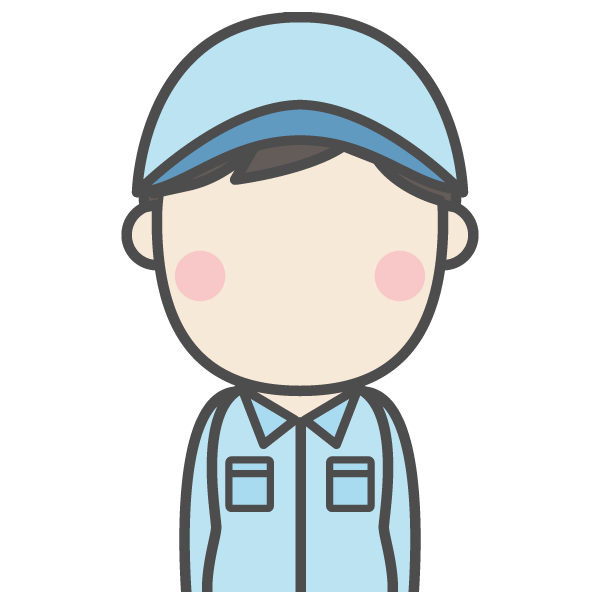
「えっ、こんなの作れないよ…」
こんなやりとりは実際にないかもしれませんが、目指す方向を言葉にするとこうなるはずです。つまり、各部門がバラバラに動いていて、情報がうまく伝わっていないと、お客様が本当に求めている製品を、現実の世界に生み出すことはできません。
つまり、これらの部門間の役割を超越して会社全体として、お客さまから求められる品質をしっかり確保できるかどうか?は、とても重要であり、そのためのしくみづくりが求められるわけです。
品質不良が発生した時のダメージ(コスト面・信頼面)
そしてその「しくみ」をうまく組み立てらてない結果、もし不良品を出してしまったら…?
- 材料費、人件費が無駄になる
- 作り直しのための時間と手間がかかる
- お客様からの信頼を失う
- 最悪の場合、取引停止になる
これは中小製造業にとって、経営を揺るがす大問題となるわけなのです。おわかりですよね。
設計品質と製造品質~それぞれの重要性
お客さまから求められている「良い品質」を実現するためには、「設計品質」 と 「製造品質」 の2つが重要です。この2つは、車の両輪のようなもので、どちらが欠けても、高品質な製品は作れません。


設計品質の具体例
設計品質 とは、「お客様が求める機能を、製品の設計に、どれだけ盛り込めているか」 ということです。
例えば、自動車部品であれば、
- 耐久性:何万キロ走行しても壊れないか?
- 温度条件:高温や低温でも正常に動作するか?
- 安全性:安全基準を満たしているか?
- 寸法精度:指定された寸法通りに作れるか?
などを、設計段階でしっかりと検討し、図面や仕様書に落とし込む必要があります。
設計段階の不備は後工程で莫大な手直しコストを生む
もし、設計段階でミスがあると、後工程で大変なことになります。製造途中で「この部品、寸法が合わないぞ!」「この材料、強度が足りないぞ!」といった問題が発覚し、設計からやり直し…なんてことになったら、時間もコストも、莫大な無駄が発生してしまいます。
製造品質の具体例
製造品質 とは、「設計図面や仕様書通りに、製品をどれだけ正確に作れるか」 ということです。
例えば、
- 組立工程:部品を正しい順番で、確実に組み立てる
- 溶接工程:適切な温度と時間で、しっかりと溶接する
- 塗装工程:ムラなく、均一に塗装する
など、各工程で、決められた手順を守り、正確に作業することが重要です。
現場での作業精度や標準手順の遵守度が製品品質を大きく左右
いくら素晴らしい設計図があっても、現場の作業者が、その通りに作れなければ、意味がありません。作業者の技術力はもちろん、作業手順が明確になっているか、作業環境が整っているか、なども、製造品質に大きく影響します。
両者の掛け算関係
設計品質(考える質) × 製造品質(つくる質) = 最終製品の品質
この式が示すように、設計品質と製造品質は、どちらか一方だけが高くてもダメなのです。両方が高いレベルで実現されて、初めて「高品質な製品」が生まれます。
例えば、設計品質が100点でも、製造品質が50点なら、最終製品の品質は50点にしかなりません。逆に、製造品質が100点でも、設計品質が50点なら、やはり最終製品の品質は50点です。
どちらが欠けても高品質は実現できない
設計部門と製造部門が、しっかりと連携し、お互いの意見を尊重しながら、協力して「良い品質」を作り上げていくことが、何よりも大切なのです。
さあ、品質管理の基本は理解できましたか? では次に不良品の種類と対策について、さらに詳しく見ていきましょう!
不良の種類と対策~コストダウンにも直結
さて「品質」の基本について学びましたが、さらに踏み込んで、「不良」について考えていきましょう。「不良」を減らすことは、コスト削減に直結するだけでなく、お客さまからの信頼を高め、会社の未来を守ることにもつながります。
内部不良と外部不良の違いと影響
不良には、大きく分けて 「内部不良」 と 「外部不良」 の2種類があります。


内部不良の実例
内部不良 とは、「製品が出荷される前に、社内で見つかる不良」 のことです。
例えば、
- 寸法ミス: 部品の寸法が、図面と違っている
- 半田不良: 電子部品の半田付けが、不十分である
- 部品の組付ミス: 部品を違う場所に付けてしまった、取り付け方が間違っている
- 外観不良: 製品に傷や汚れがある、塗装が剥がれている
など、製造工程の様々な場面で発生します。
手直し工数の増大、納期遅延、材料ロスなどを引き起こす
内部不良が発生すると、
- 不良品を直すための、余計な手間(手直し工数)がかかる
- 納期に間に合わなくなる
- 不良品に使った材料が無駄になる
など、様々な問題が発生します。これらはすべて、会社の「損失」につながります。
外部不良(流出不良)の実例
外部不良 (流出不良)とは、「製品が出荷された後、お客様の元で見つかる不良」 のことです。
例えば、
- 出荷後のクレーム: お客様から「規格から外れている」「製品が動かない」「すぐに壊れた」などの苦情が来る
- リコール: 製品に重大な欠陥があり、回収・修理が必要になる
- 損害賠償リスク: 製品の欠陥が原因で、お客様が怪我をしたり、損害を受けたりした場合、賠償責任を負う可能性がある
など外部不良が流出すれば、内部不良よりもさらに深刻な問題を引き起こします。
企業ブランドや信頼を失墜させる大きなリスク
外部不良は、会社の信用を大きく傷つけます。
- お客様からの信頼を失う
- 「あの会社の製品は、信用できない」という悪い評判が広まる
- 取引先から、取引を打ち切られる
- 最悪の場合、会社の存続が危うくなる
など、取り返しのつかない事態に陥る可能性もあります。
内部不良を抑えるメリット
内部不良を減らすことは、会社の「利益」に直結します。
- 直接コスト(材料費・人件費)の削減: 不良品が減れば、材料の無駄遣いがなくなり、手直しにかかる人件費も削減できます。
- 現場のモチベーション向上: 不良品が減ると、現場の作業者は「自分たちの仕事は、きちんとお客様に届いている」という達成感を得られます。また、「不良を出さないようにしよう!」という意識も高まります。
外部不良を抑えるメリット
外部不良を減らすことは、会社の「未来」を守ることにつながります。
- 顧客満足度向上、リピーター獲得: お客様に「良い製品だ」と満足してもらえれば、また同じ製品を買ってくれる可能性が高まります。
- 市場からの信頼獲得、長期的な売上増: 「あの会社の製品は、安心して使える」という評判が広まれば、新しいお客様も増え、会社の売上も安定します。
内部不良と外部不良、どちらも減らすことが重要ですが、特に外部不良は、会社の存続に関わる重大な問題です。「外部不良ゼロ」 を目指して、品質管理に取り組む必要があります。
では次は、これらの問題解決のための基本的な考え方である「QC思考法」について解説します。
不良を防ぐ具体策:ばらつき対策と最終確認
では、いよいよ品質管理の実践編! 不良を未然に防ぐための具体的な対策として、「ばらつき対策」と「最終確認」の2つの攻略策を解説します。


攻略策①ばらつきを最小化する
「ばらつき」とは、製品の品質が、目標値からどれだけズレているか、ということです。例えば、同じ製品を100個作ったときに、寸法や重さが、すべてピッタリ同じになることは、まずありません。必ず、多少の「ばらつき」が生じます。
この「ばらつき」が大きいと、不良品が発生する可能性が高くなります。そこで、「ばらつき」をできるだけ小さくする ことが、品質管理の重要なポイントになります。
具体的な方法としては、
- CNCマシンや測定器の定期校正: CNCマシン(数値制御で動く工作機械)や測定器は、使っているうちに精度が落ちてくることがあります。定期的に校正(精度を調整すること)を行い、常に正確な状態を保つことが重要です。
- 作業手順書の活用: 作業手順書は、「誰が、いつ、どこで、何を、どのように」作業するかを明確に示したものです。作業手順書に従って作業することで、作業者による「ばらつき」を減らすことができます。
- 作業者の技能訓練・認定制度の導入によるヒューマンエラー低減: 作業者の技術力は、製品の品質に大きく影響します。定期的な技能訓練を実施し、一定のレベルに達した作業者を認定する制度を導入することで、ヒューマンエラー(人為的なミス)を減らすことができます。
これらの対策を組み合わせることで、製造工程における「ばらつき」を最小限に抑え、不良品の発生を防ぐことができます。
攻略策②最終確認の重要性
どんなに「ばらつき」を小さくしても、不良品がゼロになることは、残念ながらありません。そこで、「最終確認」 が重要になります。
「最終確認」とは、製品が出荷される前に、品質基準を満たしているかどうかを、最終的にチェックすることです。
具体的な方法としては、
- ダブルチェック体制: 一人の作業者だけでなく、複数の目でチェックすることで、見落としを防ぎます。
- 検査記録の電子化: 検査結果を紙ではなく、電子データとして記録することで、データの改ざんを防ぎ、トレーサビリティ(追跡可能性)を確保します。
- 出荷前の品質監査: 品質管理部門が、出荷前の製品を抜き取り検査し、品質に問題がないかを確認します。
これらの対策を徹底することで、不良品がお客様の元に届くことを、未然に防ぐことができます。
具体的チェックリストの作り方
「最終確認」を効果的に行うためには、「チェックリスト」 を作成することが有効です。
チェックリストの作り方は、
- 不良が発生しやすい工程をリストアップ: 過去の不良データや、現場の作業者の意見を参考に、不良が発生しやすい工程を洗い出します。
- 検査基準と必要検査項目を明確化: 各工程で、何を、どのように検査するのか、具体的な検査基準と検査項目を決めます。
例えば、
工程 | 検査項目 | 検査基準 | 検査方法 |
---|---|---|---|
部品A組立 | 部品の取り付け位置 | 図面通りに取り付けられていること | 目視、ノギス |
部品A組立 | ネジの締め付けトルク | 規定トルク(〇〇N・m)で締め付けられていること | トルクレンチ |
製品B塗装 | 塗装のムラ | 目視でムラがないこと | 目視、膜厚計 |
製品B外観 | 傷、汚れ | 目視で傷、汚れがないこと | 目視、ルーペ |
このようなチェックリストを作成し、検査担当者が、このリストに従って検査を行うことで、検査漏れを防ぎ、検査の質を均一に保つことができます。
「ばらつき対策」と「最終確認」を徹底することで、不良品を大幅に減らし、お客様に安心して使っていただける製品を提供することができます。
では次は、問題解決のための基本的な考え方である「QC思考法」について解説します。これはとても大切な考え方になるので、ぜひ読み進めてください!
品質管理を成功に導く3つのQC的思考と実践
ここまで、品質管理の基本、不良の種類と対策、具体的な対策について学んできました。次はさらに一歩進んで、品質管理を成功に導くための「QC的思考」と、その実践方法について解説します。
QC的思考とは、「品質管理(Quality Control)」の視点から、問題解決に取り組むための考え方です。この考え方を身につけることで、品質管理の活動を、より効果的に進めることができます。
QC的思考①消費者指向:顧客の声を現場に活かす


QC的思考の基本は、「消費者指向」です。つまり、「常にお客様の立場になって考える」ということです。
市場クレーム情報のフィードバックルートを整備
お客様からクレームがあった場合、その情報を、営業部門だけで抱え込まず、品質保証部門、そして製造現場まで、迅速かつ正確に伝える ことが重要です。
- 営業: お客様からクレームを受け付ける
- 品質保証部門: クレームの原因を調査・分析する
- 製造現場: 原因に基づいた対策を講じ、再発防止に努める
このような情報共有体制を整備することで、お客様の声を、製品の改善に活かすことができます。
クレームの情報をもとに設計・製造条件を見直す
クレームの原因が、設計にあるのか、製造にあるのか、それともお客様の使用方法にあるのかを、しっかりと分析し、必要に応じて、設計や製造条件を見直すことが重要です。
お客様の使用環境を想定した製造条件の設定
製品は、お客様の元で、様々な環境で使用されます。例えば、
- 高温多湿の場所で使われる
- 振動の多い場所で使われる
- 屋外で、雨風にさらされる
など、製品によって、使用環境は大きく異なります。
実使用環境(温度や振動など)を想定した試験や評価
製品を設計・製造する際には、お客様の使用環境を想定し、それに耐えられるかどうかを、試験や評価によって確認する必要があります。
「実際にお客様がどんな使い方をするか」を製造ラインにも共有
そして、その情報を、製造現場の作業者にも共有することが重要です。「この製品は、こんな場所で、こんな風に使われるんだ」ということを理解することで、作業者の品質に対する意識も高まります。
QC的思考②重点指向:限られたリソースの活かし方


私たち中小製造業は、人、モノ、お金、時間、すべてのリソースが限られています。そのため、「重点指向」、つまり、「重要なポイントに、集中的に資源を投入する」 ことが重要です。
不良率の高い工程に優先的に注力
すべての工程を、同じように管理するのではなく、不良率の高い工程に、優先的に注力する ことが、効率的な品質管理につながります。
ばらつきが大きいポイントを統計的に把握し改善
「どの工程で、どんな不良が多いのか?」「どの工程の、ばらつきが大きいのか?」を、データに基づいて、統計的に把握することが重要です。
Pareto図などを活用して優先順位を明確に
パレート図などのツールを活用することで、問題点を「見える化」し、優先順位を明確にすることができます。(パレート図については、後の章で詳しく解説します)
重要品質特性の管理
製品には、様々な品質特性があります。例えば、
- 寸法精度
- 締付トルク
- 溶接部強度
- 外観
- 耐久性
など、製品によって、重要な品質特性は異なります。
例えば「寸法精度」「締付トルク」「溶接部強度」など、製品に直結する項目は重点管理
これらの品質特性の中でも、特に重要なもの、つまり、製品の機能や安全性に直結する項目 は、重点的に管理する必要があります。
コストインパクトが大きい部分ほど早期に対策
また、不良が発生した場合に、コストへの影響が大きい項目ほど、早期に対策を講じる必要があります。
QC的思考③事実に基づく管理:三現主義の徹底


QC的思考のもう一つの基本は、「事実に基づく管理」 です。つまり、「自分の目で見て、自分の耳で聞いて、自分の手で触って、事実を確認する」 ということです。
そのために重要なのが、「三現主義」 です。
現場:発生場所での即時確認
問題が発生したら、すぐに 「現場」 に行き、自分の目で状況を確認することが重要です。
作業者へのヒアリングと生の情報収集
現場の作業者に話を聞き、生の情報(一次情報)を収集することも大切です。
不具合が起きたときは必ず「その場を見る」のが基本
「机の上で考える」のではなく、「現場で考える」ことが、問題解決への近道です。
現物:不良品を目で見て触って確認
問題の原因を特定するためには、「現物」 を確認することが不可欠です。
良品との比較と測定データの分析
不良品を、良品と比較したり、測定データと照らし合わせたりすることで、問題の原因が見えてくることがあります。
画像や動画での記録で再発防止策を立案
不良品の状態を、写真や動画で記録しておくと、後で原因を分析したり、再発防止策を検討したりする際に役立ちます。
現実:作業手順や管理基準が守られているかチェック
問題が発生した際には、「現実」、つまり、「実際の作業状況」 を確認することも重要です。
手順逸脱がないか、記録類を点検
作業手順書通りに作業が行われているか、作業記録はきちんと付けられているか、などをチェックします。
「作業標準通りにできていない」場合の原因究明
もし、作業手順書通りに作業が行われていない場合は、その原因を究明し、対策を講じる必要があります。
「消費者指向」「重点指向」「事実に基づく管理(三現主義)」、この3つのQC的思考を意識して、品質管理に取り組むことで、必ずや、皆さんの工場の品質レベルは向上するはずです!
品質管理を機能させる組織づくりのポイント
QC的思考を理解した上で、それを実践するためには、「組織づくり」 が非常に重要になってきます。どんなに素晴らしいツールや手法があっても、それを使いこなす「人」と、その「人」が働く「組織」が機能していなければ、品質管理はうまくいかないからです。
そこで次に、品質管理を機能させるための組織づくりのポイントとして、
- 部署間コミュニケーションの強化
- 現場主導の改善活動を促す仕組み
の2つを解説します。
部署間コミュニケーションの強化
品質管理は、特定の部署だけで行うものではありません。営業、設計、製造、品質保証など、すべての部署が連携して取り組む 必要があります。
そのためには、部署間のコミュニケーションを強化する ことが不可欠です。
営業、設計、製造、品質保証が定期的に情報交換
例えば、
- 週に1回、各部門の代表者が集まって、品質に関する会議を行う
- 新しい製品を開発する際には、各部門の担当者が集まって、合同で検討会を行う
- クレームが発生した際には、関係部署が速やかに情報を共有し、連携して対応する
など、定期的な情報交換の場を設けることが重要です。
不良情報の共有から再発防止策の浸透までをスムーズに
特に、不良に関する情報は、迅速かつ正確に共有する必要があります。
- 不良が発生した日時、場所、内容
- 不良の原因
- 講じた対策
- 再発防止策
これらの情報を、関係部署間で共有し、再発防止策を徹底することで、同じような不良の発生を防ぐことができます。
現場主導の改善活動を促す仕組み
品質管理は、トップダウン(上からの指示)だけでなく、ボトムアップ(現場からの提案) で進めることが重要です。現場の作業者は、日々、製品と向き合っているため、品質に関する問題点や改善点に、最も気づきやすい立場にあります。
改善提案制度、Kaizen活動の事例紹介
現場からの改善提案を促すためには、
- 改善提案制度: 従業員が、自由に改善提案を提出できる制度を設ける
- カイゼン活動: 小集団(チーム)で、継続的に改善活動を行う
などの仕組みを導入することが効果的です。
例えば、
- 「工具の置き場所を変えたら、作業効率が上がった」
- 「作業手順書を写真付きにしたら、ミスが減った」
- 「部品の梱包方法を変えたら、輸送中の破損が減った」
など、現場からの小さな改善提案が、大きな成果につながることも少なくありません。
現場作業者の声を経営層が評価する文化づくり
そして、何よりも大切なのは、現場からの提案を、経営層がしっかりと評価する文化 を作ることです。
- 優れた提案には、表彰や報奨金を出す
- 提案内容を、社内報や掲示板で紹介する
- 経営層が、現場に足を運び、直接、作業者の話を聞く
など、現場からの声を尊重し、積極的に評価することで、従業員のモチベーションを高め、改善活動を活性化させることができます。
「品質管理は、全員参加で」
この言葉を合言葉に、部署間の壁を越え、現場の知恵と力を結集して、品質管理に取り組んでいきましょう!
これで、品質管理に関する一連の解説は終わりです。このブログ記事が、皆さんの工場の品質向上に、少しでも役立つことを願っています。
「品質は、一日にしてならず」
地道な努力の積み重ねが、必ずや、大きな成果につながります。諦めずに、継続して品質管理に取り組み、お客様に喜ばれる製品を作り続けていきましょう!
まとめ:品質管理の全体像=高品質は“設計×製造×管理”の総合力の証明
長い記事を最後までお読みいただき、ありがとうございました! 品質管理について、様々な角度から解説してきましたが、最後に、全体像をまとめておきましょう。
品質管理の本質は「お客様にとって価値あるモノを安定して提供する」こと
品質管理とは、単に「不良品を出さない」ことだけではありません。お客様が求める品質、つまり、「お客様にとって価値あるモノ」を、安定して、効率よく提供する ことが、品質管理の本質です。
そのためには、
- 設計品質: お客様のニーズを的確に捉え、それを製品の設計に反映させる
- 製造品質: 設計図面や仕様書通りに、正確に製品を作る
- 品質管理: 品質を維持・向上させるための、様々な活動を行う
この3つが、三位一体となって機能することが重要です。
高品質は、“設計 × 製造 × 管理”の総合力の証明
つまり、高品質な製品は、設計、製造、管理、それぞれの部門が、高いレベルで連携し、協力し合うことで、初めて実現できるのです。
不良対策は「ばらつきをいかに抑えるか」と「最終確認を徹底するか」にかかっている
不良品を減らすためには、
- ばらつきをいかに抑えるか: 製造工程における「ばらつき」を最小限に抑える
- 最終確認を徹底するか: 出荷前に、品質基準を満たしているかどうかを、厳格にチェックする
この2つが、非常に重要です。
QC的思考(消費者指向、重点指向、事実に基づく管理)は現場改善の強い味方
そして、品質管理を効果的に進めるためには、「QC的思考」 が欠かせません。
- 消費者指向: 常にお客様の立場になって考える
- 重点指向: 重要なポイントに、集中的に資源を投入する
- 事実に基づく管理(三現主義): 現場・現物・現実を、自分の目で見て、確認する
これらの考え方は、現場の改善活動を、より効果的に、より効率的に進めるための、強力な武器となります。
組織全体で品質に取り組むことで、大きなコスト削減と顧客満足度の向上が見込める
品質管理は、特定の部署や担当者だけが行うものではありません。経営層から現場の作業者まで、組織全体で取り組む ことで、初めて大きな成果を上げることができます。
そして、その成果は、
- コスト削減: 不良品の減少、手直し工数の削減、材料ロスの削減
- 顧客満足度の向上: お客様からの信頼獲得、リピーターの増加、新規顧客の開拓
という形で、必ずや、皆さんの会社に、大きなメリットをもたらしてくれるはずです。
品質管理は、終わりのない旅です。
常に改善を繰り返し、より良い製品、より良いサービスを、お客様に提供し続けること。それが、私たち中小製造業の使命であり、生き残るための道なのです。
今回の内容が、皆さんの品質管理の旅の、良き道しるべとなることを、心から願っています。
さあ、みんなで一緒に、品質管理の整備で、未来を切り拓きましょう!