「5S活動」で工場はここまで変わる!
もちろん5S活動とは「整理」「整頓」「清掃」「清潔」「習慣(しつけ)」の5つのSからなる職場環境改善活動のことです。
工場やオフィスなど、あらゆる現場で取り組まれていますが、その効果を最大限に引き出すのは簡単ではありませんよね。
そこで今回は、5S活動の達人である山田製作所様の成功事例を徹底解剖!したいと思います。
なんとYouTube動画でその改善ノウハウを惜しみなく公開されているので、その中から特に秀逸な12の改善事例をピックアップし、専門家目線で解説します。
さらに、なぜ山田製作所様の5S活動が25年以上も継続し、驚異的な成果を上げ続けているのか、その3つの理由を深掘りしていきます。
あなたの職場でもすぐに実践できる具体的な改善アイデアが満載!
さあ、山田製作所様の5Sワールドへ一緒に飛び込みましょう!
山田製作所とはどんな会社?
山田製作所は、金属加工を専門とする町工場です。
従業員数約20名と決して大きな会社ではありませんが、その5S活動への取り組みは業界でもトップレベルと評判です。
その徹底ぶりは、工場内の隅々まで行き届き、まるでショールームのように整然としています。
しかし、彼らの5S活動は単なる見た目の美しさだけではありません。
25年にも及ぶ改善の積み重ねによって、業務効率の向上、品質の安定、そして従業員のモチベーションアップといった、目に見える成果を上げ続けているのです。
一体どのような工夫を重ねてきたのでしょうか?
その秘密は、YouTubeチャンネルで公開されている動画に隠されています。
今回の動画はこちら>https://youtu.be/9qwlcT3w35s?si=UBYk2BXCGZb_3I-x&t=785
動画内では、山田製作所の社員自らが、具体的な改善事例や、その背景にある考え方、そして日々の取り組みについて、包み隠さず紹介してくれています。
その正直で謙虚な姿勢は、多くの視聴者の共感を呼び、5S活動のお手本として注目を集めているのです。
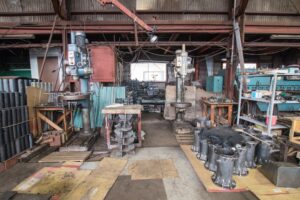
素晴らしすぎる山田製作所の改善事例12選
そしてその山田製作所のYouTube動画から、特に参考になる12個の改善事例を抽出しました。
これらの事例は、どれもシンプルでありながら、効果は絶大です。
あなたの職場でも、すぐに実践できるアイデアがきっと見つかるはずです。
事例①:板材の配置の向きの変更(縦置き化)
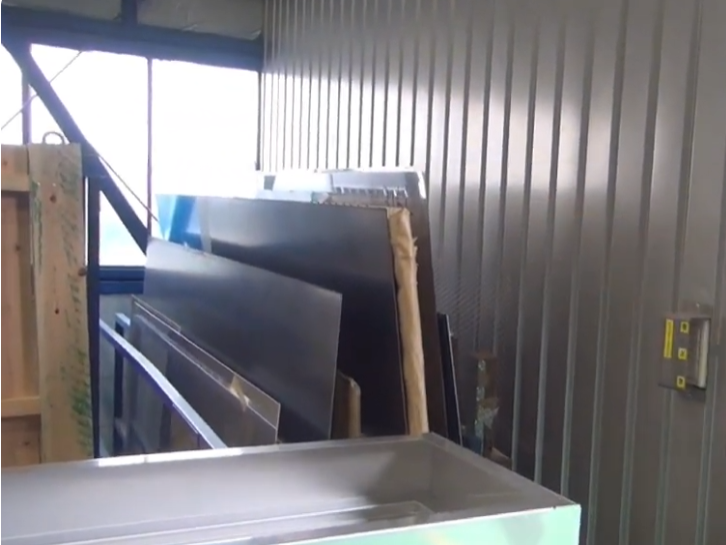
Before: 板材を平置きしていたため、下段の板材を取り出す際に、上の板材を全て移動させる必要があり、2~3人がかりで30分もかかっていました。
After: 板材を縦置きにすることで、1人でも数分程度で簡単に取り出せるようになりました。
改善ポイント:
- 作業効率の劇的向上: 縦置きにすることで、重たい板材を移動させる手間が省け、作業時間が大幅に短縮されました。
- 省人化: 複数人で対応していた作業が1人でできるようになり、人員の有効活用につながります。
- 安全性の向上: 重たい板材の移動に伴う事故のリスクを低減できます。
- スペースの有効活用: 縦置きは平置きよりも省スペースで、保管場所の有効活用にも貢献します。
専門家解説:
この改善は、5S活動の「整理」と「整頓」の要素を含んでいます。
- 整理: 不要なものを捨てる、あるいは必要なものを必要な場所に置くことで、作業スペースを確保し、作業効率を向上させます。
- 整頓: 必要なものを決められた場所に置き、いつでも取り出せる状態にすることで、探し物や移動の時間を削減します。
山田製作所では、板材を縦置きにすることで、これらの要素を実現し、作業効率と安全性を大幅に向上させました。
応用と発展:
この縦置き化のアイデアは、板材だけでなく、他の形状の材料や部品にも応用できます。
- 長尺物: パイプや棒材などを縦置きにすることで、取り出しやすさとスペース効率を向上させます。
- 不定形物: 専用の棚やラックを作成し、縦置きに近い形で保管することで、取り出しやすさとスペース効率を向上させます。
縦置き化に加えて、ラベル表示や色分けなどの工夫を組み合わせることで、さらに管理がしやすくなります。
まとめ:
板材の縦置き化は、シンプルな改善ですが、その効果は絶大です。
ぜひあなたの職場でも、このアイデアを活用して、5S活動を推進してみてください。
事例②:残材台車に寸法表記
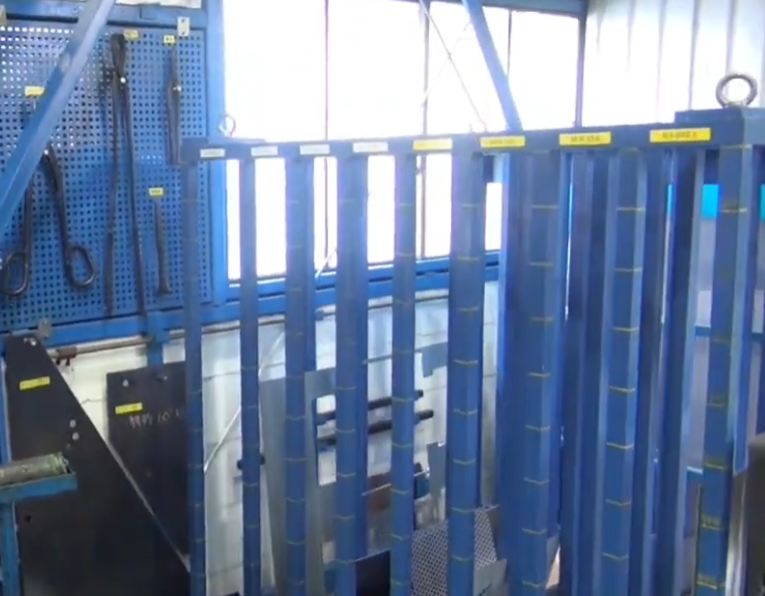
Before: 残材の種類分けはされていたものの、寸法がわからず、必要なサイズの残材を探すのに時間がかかっていました。都度計測する必要があり、手間がかかっていました。
After: 残材台車に残材の種類だけでなく、寸法も表記するようにしました。
改善ポイント:
- 作業時間の短縮: 寸法がひと目でわかるため、計測する手間が省け、作業時間を短縮できます。
- ミス削減: 目視でサイズを確認できるため、誤ったサイズの残材を使用するミスを減らせます。
- 在庫管理の効率化: 残材のサイズと量がすぐに把握できるため、在庫管理が容易になります。
専門家解説:
この改善は、5S活動の「整頓」と「表示」の要素を組み合わせたものです。
- 整頓: 必要なものを決められた場所に置き、いつでも取り出せる状態にすることで、探し物や移動の時間を削減します。
- 表示: ものの名前や数量、使用方法などを表示することで、誰でも簡単に必要な情報を入手できるようにします。
山田製作所では、残材台車に寸法を表示することで、これらの要素を実現し、作業効率と正確性を向上させました。
応用と発展:
この寸法表示のアイデアは、残材だけでなく、様々な場所に適用できます。
- 工具箱: 工具の種類やサイズを表示することで、必要な工具をすぐに見つけられます。
- 部品棚: 部品の種類や数量を表示することで、在庫管理を効率化できます。
- 書類棚: 書類の内容や日付を表示することで、必要な書類をすぐに見つけられます。
表示方法も、ラベル、テプラ、マーカーなど、様々な方法があります。
まとめ:
残材台車への寸法表記は、一見小さな改善ですが、作業効率や正確性、在庫管理に大きな影響を与えます。
ぜひあなたの職場でも、このアイデアを活用して、5S活動を推進してみてください。
事例③:シャーリング工具の手元化管理
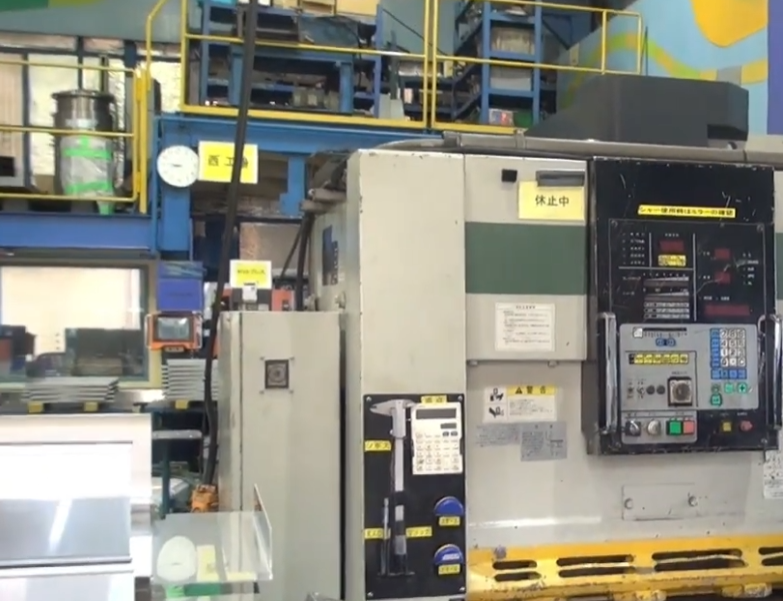
Before: シャーリング加工に必要な工具を取りに行く手間があり、作業が中断されていました。
After: 必要な工具をシャーリング設備の近くに設置することで、工具を取りに行く時間を削減しました。
改善ポイント:
- 作業時間の短縮: 工具を取りに行くムダな時間を削減し、作業効率を向上させました。
- 作業の標準化: 必要な工具を所定の位置に配置することで、作業の標準化を促進し、誰でも迷わず工具を見つけられるようにしました。
- 紛失防止: 工具を特定の場所に集約することで、紛失のリスクを低減しました。
専門家解説:
この改善は、5S活動の「整頓」と「清潔」の要素を組み合わせたものです。
- 整頓: 必要なものを決められた場所に置き、いつでも取り出せる状態にすることで、探し物や移動の時間を削減します。
- 清潔: 常に整理整頓された状態を維持することで、清潔な職場環境を保ち、紛失や故障を防ぎます。
山田製作所では、シャーリング工具を手元化管理することで、これらの要素を実現し、作業効率と品質の向上につなげました。
応用と発展:
- 他の工具にも応用: シャーリング工具だけでなく、他の工程で使用する工具にも手元化管理を適用できます。
- 工具の定量化: 必要な工具の数を決め、常にその数を維持することで、紛失や不足を未然に防ぎます。
- 工具の点検: 定期的に工具の点検を行い、破損や摩耗を見つけたらすぐに交換することで、品質の安定と安全性の確保につなげます。
- 紛失対策の強化: 紛失した場合のルールを明確化し、作業員全員に周知徹底することで、紛失防止を強化します。
- 例えば、紛失した場合は作業を中断し、全員で探すことをルール化する。
- 紛失しやすい工具には、タグやラベルを付けるなどの工夫も有効です。
まとめ:
シャーリング工具の手元化管理は、作業効率の向上だけでなく、品質の安定、安全性の確保、紛失防止など、様々な効果が期待できます。
ぜひあなたの職場でも、このアイデアを活用して、5S活動を推進してみてください。
事例④:治具置き場を独自に作成
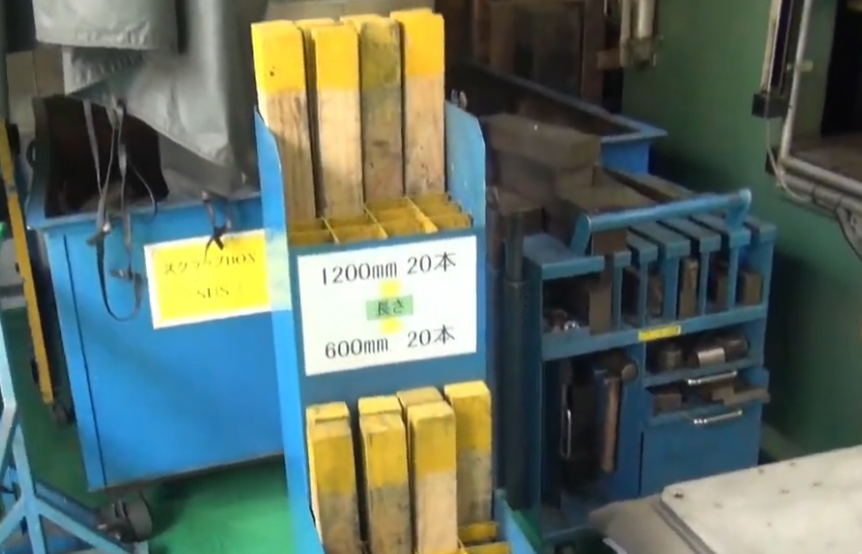
Before: 治具の置き場が定まっておらず、必要な治具を探すのに時間がかかっていました。また、治具が戻されたかどうかがわかりにくく、紛失や重複購入のリスクがありました。
After: 色分けされた治具置き場を独自に作成し、治具を戻す場所を明確にしました。
改善ポイント:
- 作業時間の短縮: 治具の置き場所が明確になり、探す手間が省けるため、作業時間を短縮できます。
- 紛失防止: 戻す場所が決まっているため、治具の紛失を防ぎ、重複購入のリスクを低減できます。
- 視覚的な管理: 色分けによって治具の種類や使用場所が一目でわかるため、管理が容易になります。
- 定位置管理: 治具の定位置を明確にすることで、誰でも迷わず治具を元の場所に戻せるようになります。
専門家解説:
この改善は、5S活動の「整頓」と「表示」の要素を組み合わせたものです。
- 整頓: 必要なものを決められた場所に置き、いつでも取り出せる状態にすることで、探し物や移動の時間を削減します。
- 表示: 色やラベルなどを使って、ものの名前や置き場所を明確にすることで、誰でも簡単に必要な情報を入手できるようにします。
山田製作所では、色分けされた治具置き場を作成することで、これらの要素を実現し、作業効率と治具の管理体制を向上させました。
応用と発展:
- 他の工具や備品にも応用: 治具だけでなく、他の工具や備品にも色分けやラベル表示を適用できます。
- 置き場所の工夫: 使用頻度や形状に合わせて、置き場所を工夫することで、さらに使いやすくすることができます。
- 定期的な見直し: 定期的に治具置き場を見直し、改善点があれば修正することで、より効率的な管理体制を維持できます。
まとめ:
治具置き場の独自作成は、治具の管理だけでなく、作業効率や紛失防止にもつながる効果的な改善です。
ぜひあなたの職場でも、このアイデアを活用して、5S活動を推進してみてください。
事例⑤:消耗品台車を設置
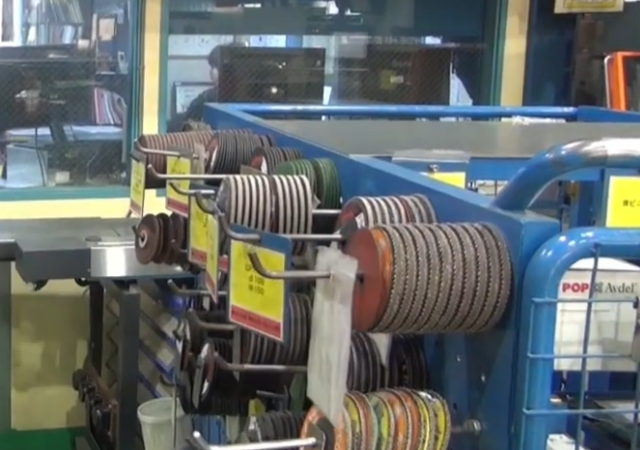
Before: 消耗品の在庫管理が徹底されておらず、在庫切れや二重発注が頻繁に発生していました。
After: 消耗品台車を設置し、在庫状況を見える化しました。また、残量が一定数以下になったら発注するルールと、発注済の札をかけるルールを導入しました。
改善ポイント:
- 在庫切れの防止: 在庫状況を見える化し、発注ルールを明確にすることで、在庫切れを防ぎ、業務の停滞を回避できます。
- 二重発注の防止: 発注済の札をかけることで、二重発注を防ぎ、コスト削減につながります。
- 在庫管理の効率化: 在庫状況が一目でわかるため、発注業務を効率化できます。
- ムダの削減: 在庫切れによる業務の停滞や、二重発注による余分な在庫を抱えるムダを削減できます。
専門家解説:
この改善は、5S活動の「整頓」と「躾」の要素を組み合わせたものです。
- 整頓: 必要なものを決められた場所に置き、いつでも取り出せる状態にすることで、探し物や移動の時間を削減します。
- 躾: 決められたルールを守り、習慣化することで、改善活動を継続的に行えるようにします。
山田製作所では、消耗品台車と発注ルール、発注済の札というシンプルな仕組みを導入することで、これらの要素を実現し、在庫管理の効率化とムダの削減に成功しました。
応用と発展:
- 他の消耗品にも応用: 消耗品台車や発注ルールは、文房具や工具など、他の消耗品にも応用できます。
- 在庫管理システムの導入: より高度な在庫管理を実現するために、在庫管理システムの導入を検討することも有効です。
- 発注ルールの見直し: 在庫状況や使用頻度に合わせて、発注ルールを定期的に見直すことで、より効率的な在庫管理が可能になります。
まとめ:
消耗品台車の設置は、在庫管理の課題を解決するための有効な手段です。
ぜひあなたの職場でも、このアイデアを活用して、5S活動を推進してみてください。
事例⑥:単品で発注する
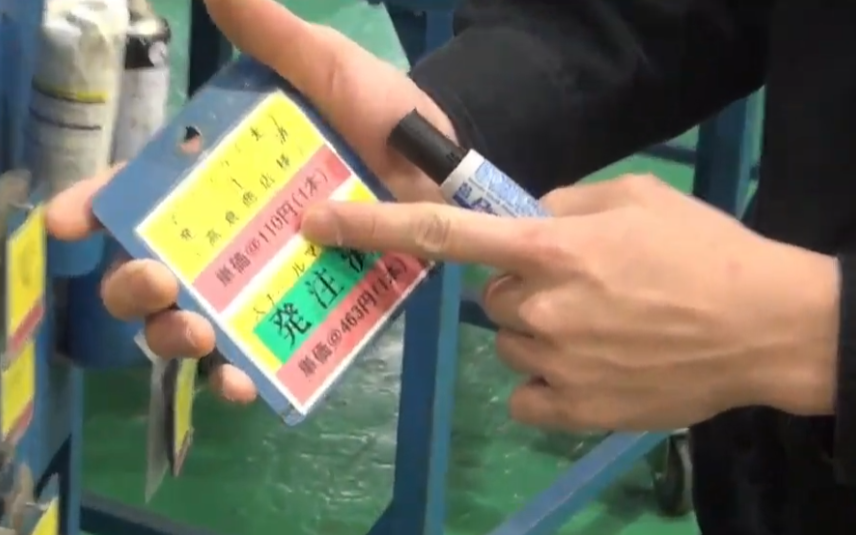
Before: マジックペンなど消耗品をダース単位で購入していましたが、実際に使用するペースは遅く、使わない在庫を抱えていました。
After: 消耗品を必要な分だけ単品で購入するように変更しました。
改善ポイント:
- 在庫コストの削減: 大量購入による余分な在庫を抱える必要がなくなり、在庫コストを削減できます。
- キャッシュフローの改善: 必要以上の資金を在庫に固定せず、他の用途に活用できるようになります。
- デッドストックの削減: 使用されないまま保管され、最終的に廃棄される可能性のあるデッドストックを減らせます。
- スペースの有効活用: 余分な在庫を保管するスペースが不要になり、他の用途に活用できます。
専門家解説:
この改善は、5S活動の「整理」の要素を重視したものです。
- 整理: 不要なものを捨てる、あるいは必要なものを必要な場所に置くことで、作業スペースを確保し、作業効率を向上させます。
山田製作所では、マジックペンを単品で購入することで、「整理」の原則を徹底し、在庫コストやデッドストックの削減に成功しました。
応用と発展:
- 他の消耗品にも応用: マジックペンだけでなく、他の消耗品にも単品購入の考え方を適用できます。
- 購入単位の見直し: 他の消耗品についても、購入単位を見直すことで、在庫コストを削減できる可能性があります。
- 在庫管理システムの活用: 在庫管理システムを導入することで、在庫状況をリアルタイムに把握し、適切な発注量を判断できます。
まとめ:
単品発注は、在庫管理の効率化とコスト削減に貢献する5S活動の重要な要素です。
ぜひあなたの職場でも、このアイデアを活用して、在庫管理を見直してみてください。
事例⑦:共用工具管理ボードの設置
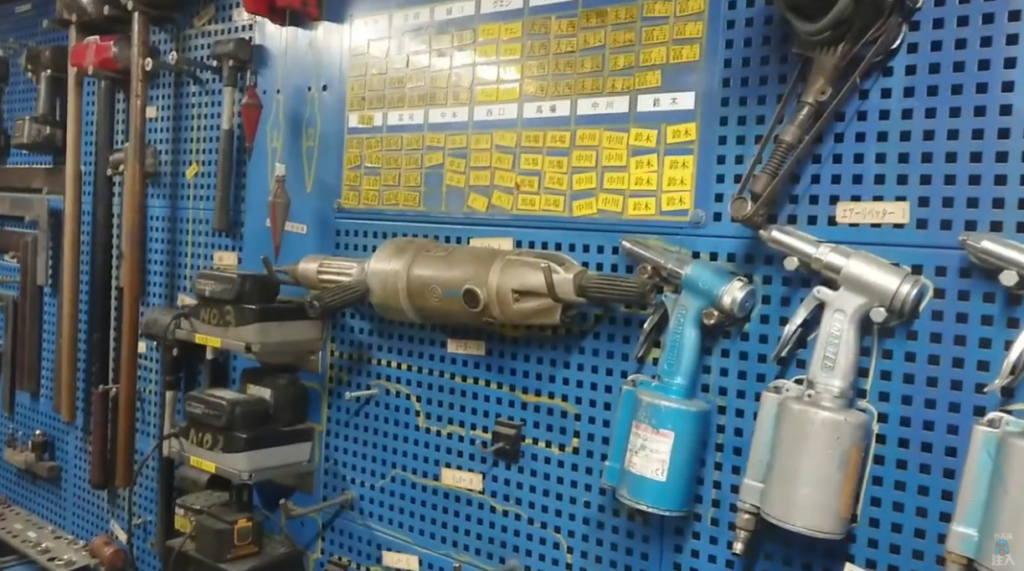
Before: 共用工具の置き場所が明確でなく、探すのに時間がかかっていました。また、誰が持ち出したのかもわからず、紛失や盗難のリスクがありました。
After: 共用工具管理ボードを設置し、工具の種類ごとに置き場所を決め、使用者の名前を表示するようにしました。
改善ポイント:
- 作業時間の短縮: 工具の置き場所が明確になり、探す手間が省けるため、作業時間を短縮できます。
- 紛失・盗難防止: 使用者の名前を表示することで、責任の所在を明確にし、紛失や盗難を防ぎます。
- 見える化: 工具の使用状況が一目でわかるため、管理が容易になります。
- 5S活動の定着: ボードを見ることで、整理整頓の意識が高まり、5S活動の定着につながります。
専門家解説:
この改善は、5S活動の「整頓」と「表示」に加え、「習慣(しつけ)」の要素も含まれています。
- 整頓: 必要なものを決められた場所に置き、いつでも取り出せる状態にすることで、探し物や移動の時間を削減します。
- 表示: ものの名前や置き場所を明確にすることで、誰でも簡単に必要な情報を入手できるようにします。
- 習慣(しつけ): 決められたルールを守り、習慣化することで、改善活動を継続的に行えるようにします。
山田製作所では、共用工具管理ボードを設置し、これらの要素を組み合わせることで、工具管理の効率化と紛失防止を実現しました。
応用と発展:
- 工具の種類に応じた管理: 使用頻度や形状に合わせて、工具の置き方を工夫することで、より使いやすく管理しやすくなります。
- デジタル管理: ツール管理アプリなどを活用し、貸出状況や返却期限などをデジタル管理することで、さらに効率化できます。
- 定期的な見直し: 定期的にボードを見直し、改善点があれば修正することで、より効果的な管理体制を維持できます。
まとめ:
共用工具管理ボードは、工具管理の課題を解決するための有効な手段です。
ぜひあなたの職場でも、このアイデアを活用して、5S活動を推進してみてください。
事例⑧:受注管理ボードで情報の共有化
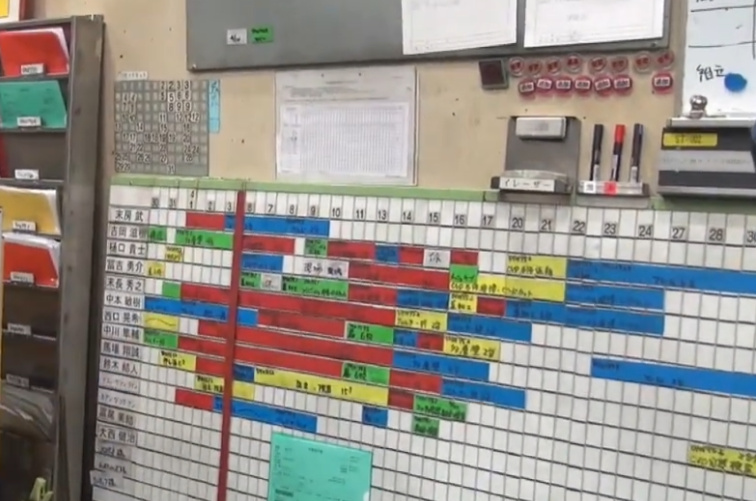
Before: 受注情報は口頭や紙ベースで管理されており、情報共有が不十分で、進捗状況の把握が困難でした。
After: 受注管理ボードを導入し、以下の情報を一元管理しました。
- 誰がどの作業を担当するのか
- 材料の入荷から出荷までのスケジュール
- 外注の予定
- 時間別の詳細なスケジュール
さらに、加工進捗表と色分けでリンクさせ、空き時間に5S活動を行う時間を確保しました。
改善ポイント:
- 情報共有の効率化: 受注情報を一元管理することで、全員が最新の情報を把握できるようになり、コミュニケーションミスや作業の遅れを防ぎます。
- 進捗管理の見える化: 時間別の管理ボードにより、各作業の進捗状況が一目でわかるため、遅れが発生した場合に迅速に対応できます。
- 5S活動の促進: 空き時間を可視化することで、5S活動の時間を確保しやすくなり、継続的な改善活動につながります。
- 納期遵守: スケジュール管理を徹底することで、納期遵守率の向上に貢献します。
専門家解説:
この改善は、5S活動の「躾」と「改善」の要素を組み合わせたものです。
- 躾: 決められたルールを守り、習慣化することで、改善活動を継続的に行えるようにします。
- 改善: 問題点を見つけ出し、それを解決するための対策を講じることで、業務プロセスや品質を向上させます。
山田製作所では、受注管理ボードを導入し、これらの要素を組み合わせることで、情報共有と進捗管理を効率化し、5S活動の推進と納期遵守を実現しました。
応用と発展:
- デジタル化: ホワイトボードだけでなく、タスク管理ツールやプロジェクト管理ツールなどを活用することで、より効率的な情報共有と進捗管理が可能です。
- KPI設定: 受注件数や納期遵守率などのKPIを設定し、定期的に進捗状況をレビューすることで、さらなる改善につなげることができます。
- チームワークの向上: 受注管理ボードをチーム全体で活用することで、コミュニケーションが活性化し、チームワークの向上にもつながります。
まとめ:
受注管理ボードの導入は、情報共有と進捗管理を効率化し、5S活動の推進と納期遵守に貢献する有効な手段です。
ぜひあなたの職場でも、このアイデアを活用して、業務プロセスを改善してみてください。
事例⑨:デジタル管理の推進
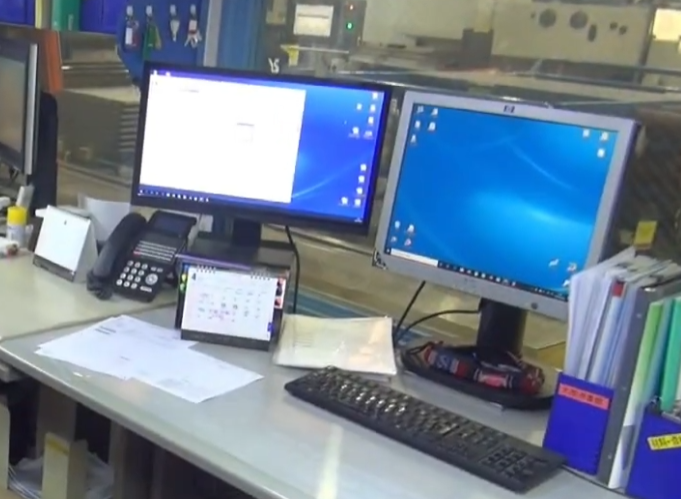
Before: 過去の作業情報や図面などの書類が事務所に溢れており、必要な情報を探すのに時間がかかっていました。また、保管スペースも圧迫していました。
After: 書類の多くをデジタルファイル化し、パソコンで管理するようにしました。
改善ポイント:
- 検索性の向上: デジタルファイル化により、キーワード検索などで必要な情報を素早く見つけ出すことができます。
- 情報共有の促進: ネットワーク上でファイルを共有することで、複数人での情報共有が容易になります。
- スペースの有効活用: 書類の保管スペースが不要になり、事務所をより広く活用できます。
- 紛失・劣化防止: デジタルデータは紛失や劣化のリスクが低く、長期的な保管が可能です。
- ペーパーレス化: 紙の使用量を削減し、環境負荷の低減にも貢献します。
専門家解説:
この改善は、5S活動の「整理」と「清潔」の要素を組み合わせ、さらに現代的なデジタル技術を活用したものです。
- 整理: 不要な書類を処分し、必要な情報だけをデジタル化することで、情報を整理し、探しやすくします。
- 清潔: 事務所内の紙の量を減らすことで、清潔な環境を維持しやすくなります。
山田製作所では、デジタル管理を推進することで、情報へのアクセス性を高め、業務効率を向上させました。
応用と発展:
- クラウドストレージの活用: クラウドストレージサービスを利用することで、場所を選ばずに情報にアクセスできるようになり、BCP対策にもなります。
- データベース化: 顧客情報や製品情報などをデータベース化することで、より高度な情報管理が可能になります。
- セキュリティ対策: デジタルデータはセキュリティ対策が重要です。アクセス権限の設定やバックアップの徹底など、適切な対策を講じることが大切です。
まとめ:
デジタル管理は、現代のビジネスにおいて不可欠な要素です。
ぜひあなたの職場でも、このアイデアを活用して、5S活動を推進してみてください。
事例⑩:文房具の形跡整頓と表示の推進
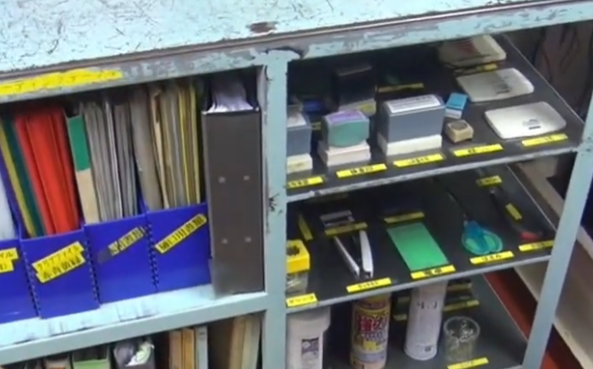
Before: 事務所で使用する文房具が整理されておらず、必要なものがすぐに見つからない状態でした。
After: 文房具を種類ごとに整理し、定位置を決め、表示を行いました。
改善ポイント:
- 作業効率の向上: 必要な文房具をすぐに見つけられるようになり、作業がスムーズに進みます。
- 紛失防止: 定位置を決めることで、文房具の紛失を防ぎます。
- 在庫管理の効率化: 何がどれだけあるか一目でわかるため、無駄な購入を防ぎ、在庫管理を効率化できます。
- 見た目の改善: デスク周りが整理され、清潔感のある職場環境になります。
専門家解説:
この改善は、5S活動の「整頓」と「表示」の要素を徹底的に実践したものです。
- 整頓: 必要なものを決められた場所に置き、いつでも取り出せる状態にすることで、探し物や移動の時間を削減します。
- 表示: ものの名前や置き場所を明確にすることで、誰でも簡単に必要な情報を入手できるようにします。
山田製作所では、文房具の整頓と表示を徹底することで、これらの要素を実現し、業務効率の向上と快適な職場環境づくりに成功しました。
応用と発展:
- 収納ツールの活用: 引き出しやケースなどを活用し、文房具の種類ごとに収納することで、さらに整理整頓しやすくなります。
- ラベル作成: ラベルメーカーやテプラなどを活用し、見やすいラベルを作成することで、より効果的な表示ができます。
- 定期的な見直し: 定期的に文房具の使用状況を見直し、不要なものを処分したり、置き場所を変更したりすることで、常に最適な状態を維持できます。
まとめ:
文房具の整頓と表示は、一見些細なことに思えますが、業務効率や職場環境に大きな影響を与えます。
ぜひあなたの職場でも、このアイデアを活用して、5S活動を推進してみてください。
事例⑪:壁掛け配線の推進
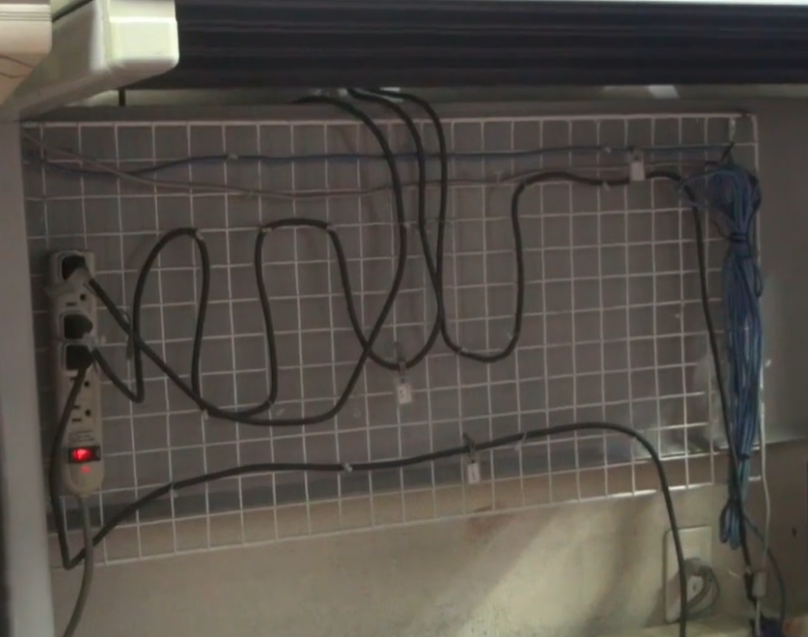
Before: 配線が床に這っており、見た目が悪く、ホコリが溜まりやすく、つまずきや火災の原因となる危険性がありました。床下収納も試しましたが、ホコリが溜まる問題は解決できませんでした。
After: 配線を壁掛けにすることで、これらの問題を解決しました。
改善ポイント:
- 安全性の向上: 床に配線がないため、つまずきや火災のリスクを低減できます。
- 清掃性の向上: ホコリが溜まりにくくなり、清掃が容易になります。
- 美観の向上: 配線が整理され、見た目がすっきりします。
- 点検の容易性: 壁掛けにすることで配線が露出するため、異常の早期発見につながります。
専門家解説:
この改善は、5S活動の「清掃」と「清潔」の要素を重視したものです。
- 清掃: 汚れやゴミを取り除き、整理整頓された状態を維持することで、安全で快適な職場環境を確保します。
- 清潔: 清掃を徹底し、整理整頓された状態を維持することで、美観を向上させ、モチベーションを高めます。
山田製作所では、配線を壁掛けにすることで、これらの要素を実現し、安全で清潔な職場環境を構築しました。
応用と発展:
- 配線ダクトの利用: 配線ダクトを使用することで、配線をより美しく整理できます。
- ケーブルの種類の統一: ケーブルの種類を統一することで、見た目がすっきりし、管理も容易になります。
- 定期的な点検: 定期的に配線の状態を点検し、劣化や損傷がないか確認することで、安全性を維持できます。
まとめ:
壁掛け配線は、安全性、清掃性、美観を向上させるだけでなく、作業効率の向上にもつながる有効な改善策です。
ぜひあなたの職場でも、このアイデアを活用して、5S活動を推進してみてください。
事例⑫:基本は立ち作業
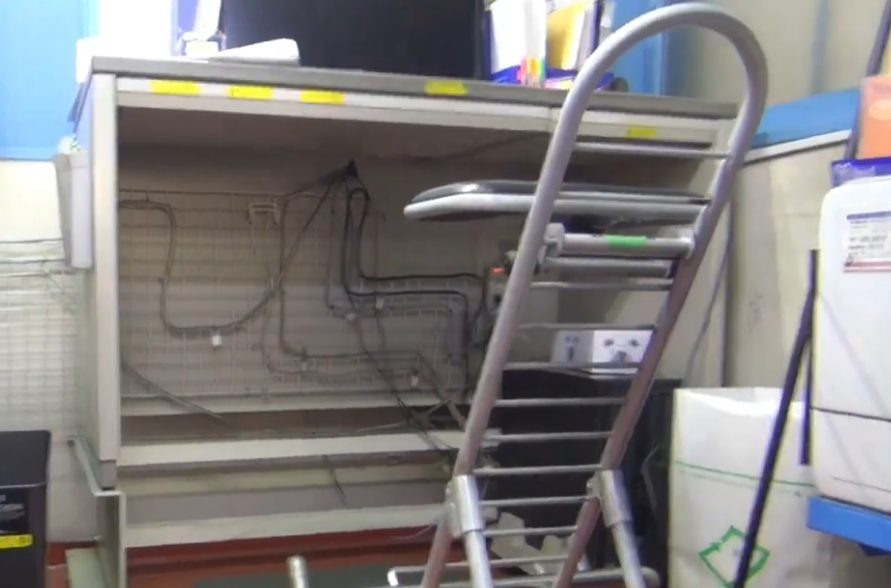
Before: デスクワークは基本的に座り作業で行われており、長時間同じ姿勢での作業は、集中力の低下や腰痛などの健康問題を引き起こす可能性がありました。
After: デスクワークを基本立ち作業に変更しました。ただし、深く考え込む必要がある場合は、高めの椅子に座って作業できるよう配慮されています。
改善ポイント:
- 集中力と生産性の向上: 立ち作業は、適度な緊張感を保ち、集中力を維持するのに役立ちます。
- 健康増進: 長時間座り続けることによる腰痛や肩こりなどのリスクを軽減し、健康増進に繋がります。
- コミュニケーションの活性化: 立ち作業は、気軽に声をかけやすい雰囲気を作り出し、コミュニケーションの活性化を促します。
- 気分転換: 立ち上がったり座ったりすることで、気分転換になり、リフレッシュ効果が期待できます。
専門家解説:
この改善は、5S活動の「清潔」と「習慣(しつけ)」の要素を、従業員の健康という観点から捉えたものです。
- 清潔: 清潔な職場環境を維持することで、従業員の心身の健康を保ちます。
- 習慣(しつけ): 決められたルールを守り、習慣化することで、改善活動を継続的に行えるようにします。
山田製作所では、立ち作業を基本とすることで、従業員の健康を促進し、結果的に生産性の向上にもつなげました。
応用と発展:
- スタンディングデスクの導入: 高さ調整可能なスタンディングデスクを導入することで、個々の体格に合わせた最適な作業環境を構築できます。
- 休憩スペースの充実: 適度な休憩を促すために、リラックスできる休憩スペースを設けることが重要です。
- ストレッチの推奨: 定期的なストレッチを推奨し、従業員の健康維持をサポートします。
まとめ:
立ち作業の導入は、従業員の健康増進と生産性向上に貢献する5S活動の一環です。
ぜひあなたの職場でも、このアイデアを活用して、働きやすい環境づくりに取り組んでみてください。
山田製作所の5S活動が秀逸な3つの理由
これまで12の改善事例を見てきました。しかし山田製作所に世界中から多くの見学者が集まっているのは、なぜなのでしょうか?当社の5S活動が「秀逸」と呼ばれる理由を3つにまとめてみましょう。
理由1:ムダをなくすための工夫の質の高さ
山田製作所の改善事例は、いずれも現場の視点に立った、具体的かつ実践的なアイデアが光ります。
例えば、板材の縦置き化や残材への寸法表記といったシンプルな工夫は、作業時間の短縮やミス削減に直接的に貢献します。
また、治具置き場や消耗品台車の設置、共用工具管理ボードの導入などは、5Sの原則を忠実に守りながらも、現場のニーズに合わせた独自性のある工夫が凝らされています。
これらの改善は、単に見た目を良くするだけでなく、作業効率や品質、安全に直接関わる重要なポイントを押さえている点が特徴です。
理由2:合理性の高い改善の数の多さ
山田製作所では、12個もの改善事例が紹介されていますが、これはほんの一部に過ぎません。
動画内では、工場内のあらゆる場所で、大小さまざまな改善が行われている様子が伺えます。
例えば、
- シャーリング工具の手元化管理
- 単品発注による在庫削減
- デジタル化によるペーパーレス化
- 文房具の整頓と表示
- 壁掛け配線による安全対策
- 立ち作業の導入
など、多岐にわたる改善が、継続的に実施されています。
これらの改善は、それぞれが独立しているのではなく、互いに連携し、相乗効果を生み出している点も注目すべきポイントです。
理由3:25年も継続してきたリーダーシップの強さ
山田製作所の5S活動は、25年という長い年月をかけて、着実に積み重ねられてきました。
これは、経営者やリーダーの強い信念と継続的な努力なしには成し得ません。
動画内では、社員が自主的に改善提案を行い、それを実践していく様子が紹介されています。
これは、トップダウンだけでなく、ボトムアップの改善活動が根付いていることを示しており、組織全体で5S活動を推進する文化が醸成されていることがわかります。
このようなリーダーシップと組織文化こそが、山田製作所の5S活動を成功に導いている最大の要因と言えるでしょう。
山田製作所のような5Sレベルを高めるための3つのポイント
山田製作所の事例を参考に、あなたの職場でも5Sレベルを高めるための3つのポイントを紹介します。
ポイント1:小さなことから始める
5S活動は、一気にすべてのことを変えようとすると、かえって逆効果になることがあります。まずは、**「これならできそう」**と思える小さなことから始めましょう。
例えば、
- デスクの上の整理整頓
- 共用スペースの清掃
- 不要な書類の処分
など、すぐに取り組めることから始め、徐々に改善の範囲を広げていくのがおすすめです。
山田製作所でも、最初は小さな改善からスタートし、25年かけて少しずつレベルアップしてきました。
ポイント2:見える化を取り入れる
5S活動の成果を見えるようにすることで、モチベーションを維持し、改善を継続しやすくなります。
例えば、
- 改善前と改善後の写真を比較する
- チェックリストを作成し、進捗状況を記録する
- 改善事例を共有する掲示板を設置する
など、工夫次第で様々な方法が考えられます。
山田製作所では、共用工具管理ボードや受注管理ボードなど、様々なツールを活用して見える化を進めています。
ポイント3:全員参加を意識する
5S活動は、一部の人の努力だけでは成功しません。
経営者から現場の社員まで、全員が積極的に参加することが重要です。
そのためには、
- 5S活動の目的や意義を共有する
- 改善提案をしやすい雰囲気を作る
- 改善活動に参加した人を表彰する
など、全員が当事者意識を持てるような工夫が必要です。
山田製作所では、毎朝の朝礼で情報共有を行い、社員一人ひとりが改善提案を積極的に行っています。
これらのポイントを参考に、あなたの職場でも5S活動を成功させ、より良い職場環境を築いていきましょう。
まとめ:山田製作所様の12の改善事例から学ぶ、明日からできる5S活動
この記事では、山田製作所様の12の改善事例をご紹介しました。
どの事例も、「そんなことまで!?」と思うような、細部まで徹底された改善ばかりでしたね。
しかし、よく見てみると、特別な道具や技術は一切使われていません。
誰にでもできる、シンプルな工夫の積み重ねで、職場環境はここまで劇的に変わるのです。
「でも、うちにはそんな時間がない…」
そう思った方もいるかもしれません。
しかし、山田製作所様も、最初から完璧だったわけではありません。
25年という長い年月をかけて、少しずつ改善を積み重ねてきたのです。
「塵も積もれば山となる」
まずは、1つの引き出し、1台の機械から、5S活動を始めてみませんか?
きっと、あなたの職場も、想像以上に快適な空間になるはずです。
そして、5S活動は、職場環境の改善だけでなく、仕事の効率化、品質向上、コスト削減、さらには従業員のモチベーションアップにもつながります。
「5S活動は、会社を強くする」
山田製作所様の事例は、この言葉をまさに体現しています。
さあ、あなたも今日から、5S活動の第一歩を踏み出しましょう!
この記事で紹介した12の改善事例を参考に、ぜひあなたの職場でも実践してみてください。
5S活動は、あなたの会社をより強く、より魅力的な場所にするための、強力な武器となるはずです。