日々、多くの製造現場で問題が生まれています。たとえばこんな悩み、皆さまの職場が直面したことはないでしょうか?
「営業が取ってきた仕事、納期が厳しすぎる…」 「倉庫にモノが溢れて、足の踏み場もないじゃない」 「不良品がまた出た!いったい、誰の責任だ?」
現場はいつも、問題の火消しに追われ、疲弊しきっている…。そんな状況が多くの現場で溢れています。でも、実は、これらの問題、ある考え方で問題を整理して、スッキリ解決できるかもしれない理論があります。
その名も、「TOC理論」です。
「なんだか難しそう…」と思ったあなた、安心してください。TOC理論は、実は現場目線の、とってもシンプルで強力な問題解決の考え方なんです。
そこで今回はは、「TOC理論で中小製造業のスループットを劇的に改善する事例研究~ボトルネック解消の真実とは?~」と題して、
- 製造現場を苦しめる「あるある」な問題の数々
- それらの問題がなぜ起こるのか、その根本原因
- そして、TOC理論がどのように問題を解決に導くのか
…これらを、現場で働く皆さまにも分かりやすく、具体的な事例を交えながら解説していきます。
「ウチの現場も、もっと良くなるかも…!」
そんな希望の光を、おとどけしたいと思ってこの記事を書いています。
今回も読み終えるまでのお時間、しばらくお付き合いくださいませ。
悲鳴を上げる現場!あなたの会社は大丈夫?中小製造業を苦しめる5つの問題
さきほどお話したとおり、多くの中小製造業の現場は、日々様々な問題に直面し、疲弊しています。ここでは、現場を苦しめる代表的な5つの問題を見ていきましょう。これらの問題は、実は密接に関連し合っており、1つの問題が別の問題を引き起こす、負のスパイラルを生み出しているのです。
1. 納期遅れが常態化!無理な納期とリソース不足が現場を追い詰める
「また納期に間に合わない…」「人手が足りないんだ!」「機械がフル稼働でも、全然追いつかないぞ!」
顧客から要求される納期は厳しさを増す一方、現場の人手不足や設備老朽化などの問題は深刻化。常に納期との戦いに追われ、現場は疲弊しています。
困った問題
- 無理な納期の常態化: 営業が顧客に約束した納期が、製造現場の実情を無視したものであることが多い。「何とかしてくれ!」と現場に無理な要求が押し付けられます。
- 過剰な残業・休日出勤: 納期を守るため、残業や休日出勤が常態化。作業者の肉体的・精神的負担は限界に近づいています。
- リソース不足の深刻化: 人手不足に加え、設備の老朽化やメンテナンス不足も深刻。生産能力は頭打ちで、需要増に対応できません。
- 品質との両立困難: 納期を優先するあまり、品質がおろそかになり、結果として手戻りやクレーム増加を招く悪循環に陥っています。
現場の苦悩
- 「また徹夜か…、体がもたないよ」
- 「家族との時間が全然取れない…、何のために働いているんだろう」
- 「機械が壊れたら、本当に納期に間に合わないぞ…」
- 「こんなに急がせたら、品質が心配だ…」
2. 在庫の山、山、山…!過剰生産が招く、スペース不足と資金繰り悪化
「この在庫、いつ使うんだ?」「もう、置く場所がないぞ!」「倉庫代もバカにならない…」
売れる見込み以上に製品を作りすぎて、倉庫は在庫の山。過剰生産は、スペース不足を招くだけでなく、資金繰りにも悪影響を与えています。
困った問題
- 倉庫スペースの圧迫: 製造した製品や部品が倉庫を占拠し、作業スペースが狭くなる。製品の移動や整理に手間がかかり、作業効率も低下します。
- 資金繰りへの悪影響: 売れない在庫は、資金を寝かせているのと同じ。仕入先への支払いは発生するのに、売上は立たず、キャッシュフローが悪化します。
- 在庫管理の煩雑化: 在庫の種類や量が増えすぎると、管理が煩雑になり、紛失や劣化のリスクも高まります。
- 廃棄リスクの増大: 長期間売れ残った在庫は、最終的に廃棄処分となる可能性も。コストをかけて作った製品が、無駄になってしまいます。
現場の不満
- 「こんなに作ってどうするんだ?置き場所にも困るし、無駄が多すぎる!」
- 「倉庫がぐちゃぐちゃで、必要なものがすぐに見つからない!イライラする!」
- 「在庫管理、もっと何とかならないのか…?」
- 「このままじゃ、資金繰りが危ないぞ…」
3. 品質トラブルが止まらない!場当たり的対応と、責任の押し付け合いが現場を疲弊させる
「また不良品が出たぞ!」「今度は何が原因だ?」「ちゃんと検査したのか!?」
品質トラブルが発生するたびに、現場は場当たり的な対応に追われ、疲弊しています。さらに、部署間での責任の押し付け合いが、問題解決を遅らせています。
困った問題
- 場当たり的な対応の連続: トラブルが発生するたびに、その場しのぎの対策を繰り返す「モグラ叩き」状態。根本的な原因究明がおろそかになっています。
- 責任の押し付け合い: 問題が発生すると、部署間で責任のなすりつけ合いが発生。「ウチの責任じゃない」「そっちの工程に問題があるはずだ」と言い争いになり、問題解決は後回しに。
- 原因の不明確さ: トラブルの原因がはっきりしないまま、対策が打たれるため、再発防止につながらず、同じようなトラブルが繰り返されます。
- 増え続ける手戻り作業: 不良品の修理や再検査に時間を取られ、通常業務に支障をきたします。
現場の悲痛な声
- 「また不良品か…、うんざりだ」
- 「いったい誰のせいなんだ?もう、押し付け合いはやめてくれ!」
- 「原因がわからないのに、どう対策すればいいんだ…」
- 「手戻り作業ばかりで、本来の仕事が進まない…」
4. 営業vs製造!部門間対立が現場の混乱を招く
「営業は何を考えてるんだ!あんな無茶な納期、現場にできるわけないだろう!」「製造はいつも言い訳ばかりだ!顧客の要望に応えるのが仕事だろう!」
営業部門と製造部門の対立は、現場に混乱をもたらします。特に、両部門の板挟みとなる現場リーダーは、精神的にも大きな負担を強いられています。
困った問題
- 情報共有不足: 営業と製造の間で、顧客情報や納期に関する情報共有が不十分。現場は、急な仕様変更や納期変更に振り回されます。
- 不明瞭な指示系統: 営業と製造のどちらの指示に従えば良いのか、現場が混乱。「とりあえず急いで作れ」「今は品質より数量優先だ」など、一貫性のない指示に困惑します。
- 責任所在の曖昧さ: トラブル発生時に、営業と製造のどちらに責任があるのかが不明確。責任の押し付け合いが発生し、問題解決が遅れます。
- モチベーションの低下: 上層部が互いに非難し合う姿に、現場は失望。「どうせ、現場のことなんて考えてないんだ…」と、仕事への意欲を失っていきます。
現場の失望
- 「上は現場のこと、全然わかってない…」
- 「営業と製造、もっとうまく連携してくれよ…」
- 「こんな環境じゃ、いい仕事なんてできるわけない…」
- 「板挟みになるのは、いつも現場のリーダーなんだよな…」
5. ベテラン頼みが限界…!技術伝承が進まず、現場の負担は増すばかり
「この作業、どうやるんだっけ?」「○○さん、ちょっと教えてください!」「また新人か…、教える時間がないんだよな…」
難しい作業や特殊な技能が必要な作業は、特定のベテラン社員に頼りがち。しかし、技術伝承が進まず、現場の負担は増える一方です。
困った問題
- 属人化の進行: 特定の社員しかできない作業が多く、その人が休むと業務が滞るリスクを抱えています。
- 技術伝承の遅れ: ベテラン社員の技術を若手に伝える仕組みが確立されておらず、技術伝承が進んでいません。
- 新人教育の負担: 新人が入るたびに、ベテラン社員が教育係を任され、通常業務に支障をきたします。
- 改善提案の軽視: 現場からの改善提案が「時間がない」「人手が足りない」などの理由で、軽視されがちです。
現場の葛藤
- 「新人に教える時間がない…、でも教えないと仕事にならないし…」
- 「難しい作業、もっと他の人にも覚えてもらわないと、いつまでも負担が減らない…」
- 「現場の意見、もっと聞いてほしい…」
- 「ベテランが辞めたら、ウチの現場はどうなるんだ…?」
なぜ問題は起こるのか?現場を苦しめる真犯人を暴く!
さきほどは、現場を悩ませる5つの問題を取り上げました。ここでは、それらの問題が なぜ 起こってしまうのか、その根本原因を深掘りしていきます。実は、これらの問題はバラバラに発生しているのではなく、複雑に絡み合い、悪循環を生み出している のです。
1. 全ての元凶!無理な納期・価格設定が現場を追い詰める
品質トラブル、納期遅れ、現場の疲弊…これら多くの問題の根本原因は、営業部門による「無理な納期・価格設定」にあります。
因果関係の流れ
- 営業が無理な納期・価格を顧客に約束: 営業は、受注獲得のために、顧客の要望を鵜呑みにして、実現が難しい納期や価格を約束してしまいます。「何とかします!」と安請け合いした結果…。
- 製造現場にしわ寄せ: 無理な納期・価格は、そのまま製造現場への過剰な負荷となります。「とにかく間に合わせろ!」「コスト削減だ!」と現場は追い詰められます。
- 確認・検査工程の省略・簡略化: 納期に間に合わせるため、本来必要な確認や検査の工程が省略されたり、簡略化されたりします。「時間がないから、多少は目をつぶって…」という危険な判断が下されがちです。
- 品質トラブル・納期遅延の発生: その結果、不良品が発生したり、納期遅れが発生したりし、顧客からのクレームにつながります。
- さらに現場が逼迫: クレーム対応、再発防止、原因調査。トラブル対応で、通常業務はさらに圧迫されてしまいます。
このように、営業が安易に結んだ「無理な約束」が、現場を疲弊させる悪循環の出発点となっているのです。
2. 売上至上主義が招く、在庫過剰と部門間対立
在庫の山、営業部門と製造部門の対立…。これらの問題の背後には、会社の「売上至上主義」という体質が潜んでいます。
因果関係の流れ
- 営業は「売上至上主義」: 営業部門は、売上目標の達成を最優先に考えます。そのため、顧客の要望を何でも受け入れ、実現困難な案件でも受注しようとします。
- 営業と製造の目標にギャップ: 営業は「売ること」が目標、製造は「納期内に、品質の良い製品を作ること」が目標。この目標のギャップが、両者の対立を生みます。
- 楽観的な販売計画: 売上至上主義のもと、過去の実績や市場動向を十分に分析せず、楽観的な販売計画が立てられます。「これだけ売れるはずだ!」という希望的観測が先行し…。
- 過剰生産、在庫の山: 製造部門は、その販売計画に基づき、製品を生産。しかし、現実は計画通りにはいかず、製品は売れ残り、在庫が山積みになります。
- 部門間対立の激化: 営業は「売れないのは製造のせいだ!」、製造は「無理な計画を立てる営業が悪い!」と、お互いを非難し合います。
「売上至上主義」という企業体質が、営業と製造の対立を招き、在庫過剰という経営問題を引き起こしているのです。
3. ボトルネック放置が、納期遅れと残業地獄を生む
納期遅れ、慢性的な残業…。これらの問題の温床となっているのが、製造工程内の「ボトルネック」です。
因果関係の流れ
- 特定の工程がボトルネックとなる: 製造工程の中で、特定の工程(機械や作業者)の処理能力が低く、全体の流れを滞らせる「ボトルネック」が存在します。
- ボトルネックに業務が集中: 他の工程がいくら頑張っても、ボトルネックの処理能力以上に生産量は増えません。結果、ボトルネック工程の前には仕掛品が滞留し、ボトルネック工程担当者には過剰な負荷が集中します。
- 納期遅れが発生: ボトルネックが全体の生産スピードを制限するため、納期遅れが発生しやすくなります。
- 残業・休日出勤で対応: 納期に間に合わせるため、現場は残業や休日出勤で対応せざるを得なくなります。「何とかしてくれ!」という号令のもと…。
- さらなる疲弊、品質問題へ: 過重労働は、作業者の疲弊を招き、ミスや品質問題の発生リスクを高めます。そして、それらがまた納期遅れを招くという悪循環に…。
ボトルネックを放置することは、製造工程全体の流れを悪くし、現場を疲弊させ、経営を圧迫する「諸悪の根源」なのです。
4. 見えざるコスト、在庫と品質問題がキャッシュフローを蝕む
資金繰りが苦しい…。その原因は、一見、現場の問題と思われる「在庫」と「品質」に潜んでいます。
因果関係の流れ
- 過剰在庫が資金を圧迫: 売れない在庫は、お金が形を変えたもの。つまり、売れない在庫は、資金を寝かせているのと同じです。倉庫に眠る在庫が、キャッシュフローを悪化させます。
- 品質トラブルが損失を生む: 品質トラブルは、製品の修理や廃棄、顧客への補償など、直接的なコスト増につながります。さらに、顧客からの信用を失い、将来の売上にも悪影響を及ぼします。
- 資金繰り悪化: 在庫と品質問題による損失で、会社の資金繰りが悪化。必要な投資ができなくなり、競争力が低下します。
- 現場への悪影響: 資金不足は、現場にも悪影響を与えます。必要な資材が購入できず、生産活動に支障をきたしたり、改善活動が停滞したりする原因になります。
在庫と品質は、製造現場だけでなく、経営全体に大きな影響を与える、見えざるコストなのです。
5. コミュニケーション不全が、現場の士気を奪い、負の連鎖を加速させる
現場の声が届かない、社員のモチベーションが低い…。これらの問題の根底には、組織内の「コミュニケーション不全」があります。
因果関係の流れ
- 現場の情報が上に伝わらない: 現場で発生している問題や改善提案が、上層部に適切に伝わっていません。報告の仕組みが整備されていなかったり、現場リーダーが問題を抱え込んでしまったりすることが原因です。
- 経営層は現場の実態を把握できない: 上層部は、現場の実情を知らないまま、机上の空論で経営判断を下してしまいます。その結果、現場の実態と乖離した指示が出され、現場の混乱を招きます。
- 現場のモチベーション低下: 「どうせ、自分たちの意見は聞いてもらえない」「上は現場のことを何もわかっていない」と、現場の社員は諦めムードになり、モチベーションが低下します。
- 負の連鎖の加速: モチベーションの低下は、生産性の低下、品質の悪化、離職率の増加などを招き、さらに問題を深刻化させます。
組織内の「情報の壁」が、現場の活力を奪い、負の連鎖を加速させる要因となっているのです。
では、これらの悪循環を断ち切り、製造業の課題解決への光明となる「TOC理論」とは、どのようなものなのでしょうか?
救世主、TOC理論!製造業の課題解決への光明
これまで、中小製造業の現場を苦しめる「5つの真犯人」を暴いてきました。しかし、そんなに悲観することもありません。これらの問題を解決に導く強力なツール 「TOC理論」 なスタイルでこれら問題に対して対策することができます。ではそんな「TOC理論」とはどんなもの?
TOC理論って何だ?「最も弱い部分」が全てを決める!
TOCとは、Theory of Constraints(制約理論) の略称です。一言でいうと、「どんなシステムも、そのパフォーマンスは最も弱い部分(=制約)によって決まる」 という考え方です。
基本原則
TOC理論では、以下の5つのステップで問題解決に取り組みます。
- 制約を見つける: システム全体のパフォーマンスを制限している、最も弱い部分(ボトルネック)を特定します。
- 制約を徹底活用する: ボトルネックが最大限に能力を発揮できるよう、あらゆる手段を講じます。
- 制約以外を制約に従わせる: ボトルネック以外の工程は、ボトルネックの能力に合わせて調整します。
- 制約の能力を高める: 設備増強や人員配置の見直しなどにより、ボトルネック自体の能力を高めます。
- 新たな制約を見つける: 1つの制約が解消されると、別の部分が新たな制約になります。再びステップ1に戻り、継続的に改善を続けます。
具体例で考えてみましょう
例えば、5つの工程からなる製造ラインがあるとします。
- 工程A:1時間あたり15個処理できる
- 工程B:1時間あたり12個処理できる
- 工程C:1時間あたり18個処理できる
- 工程D:1時間あたり15個処理できる
- 工程E:1時間あたり20個処理できる
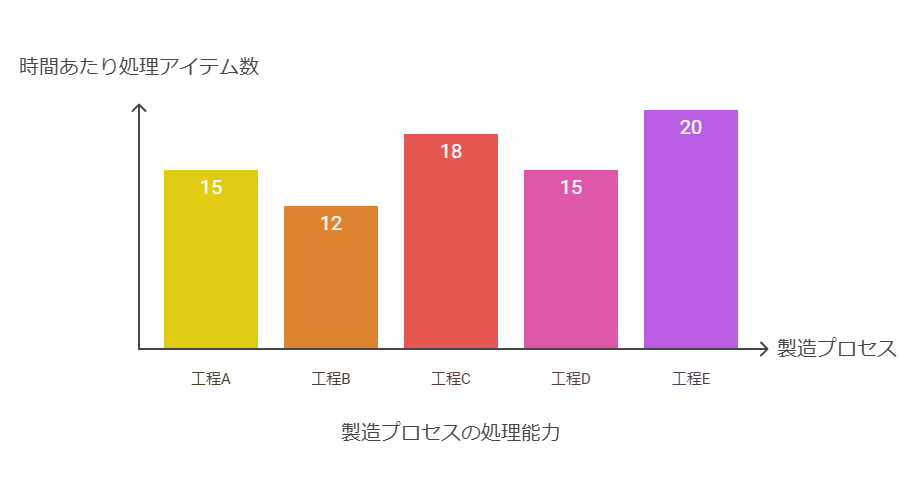
この場合、工程Bが「制約」 となります。なぜなら、他の工程がいくら頑張っても、工程Bが1時間に12個しか処理できないため、ライン全体のスループット(生産量)は1時間あたり12個以上に増えない からです。
上記を見るとわかると思うのですが、工程Aがフル生産すれば工程Bの前に、1時間あたり3個ずつ在庫は増えていくことになります。また工程C、D、Eも工程Bの12個ずつしか流れてこないので、工程はどれも待ち状態ですよね。
そのためTOC理論では、まず工程Bの能力を最大限に引き出し、他の工程を工程Bのペースに合わせ、次に工程Bの能力向上を図ります。そして、工程Bの能力が向上し、別の工程(例えば工程A)が新たな制約となったら、再び同じステップで改善を進めていきます。
TOC理論 vs 一般的な問題解決:「全体最適」への道
一般的な問題解決のアプローチは、「部分最適」 に陥りがちです。つまり、個々の問題に個別に対処するため、部分的には改善されても、全体としては非効率なまま ということがよくあります。
例えば、
- 営業は、とにかくたくさん売ろうとする → 在庫過剰
- 製造は、各工程の効率を上げようとする → ボトルネック以外を改善しても、全体の生産量は増えない
- 各部門が、自分の部門の目標だけを追求する → 部門間の対立
一方、TOC理論は、「全体最適」 を目指します。つまり、「制約」というシステム全体のパフォーマンスを制限する要因に焦点を当て、そこを改善することで、全体のパフォーマンスを大きく向上させる ことを狙います。
TOC理論の強み
- シンプルでわかりやすい: 「制約」に焦点を当てるという、非常にシンプルな考え方です。
- 迅速な効果: 「制約」に集中して改善を行うため、比較的短期間で効果を実感できます。
- 継続的な改善: 制約は常に移動するため、一度改善して終わりではなく、継続的な改善活動につながります。
TOC理論が”効く”理由:製造現場の問題にどうアプローチする?
TOC理論は、これまで見てきた製造現場の問題に、どのように効果を発揮するのでしょうか?
- 品質トラブル: 品質トラブルの真因となっている「制約」を特定し、その工程の品質管理を徹底することで、不良品の発生を抑えます。例えば、検査工程がボトルネックなら、検査員の増員や検査機器の導入などが考えられます。
- 現場目線の効果: 不良品が減ることで、手直しや再検査の工数が削減され、現場の負担が軽減されます。「また不良品か…」というストレスから解放されるでしょう。
- 在庫過剰: 「制約」に合わせて生産量を調整することで、過剰生産を抑制し、在庫を適正化します。例えば、ボトルネック工程の生産能力に合わせて、前工程の生産量を調整します。
- 現場目線の効果: 倉庫がスッキリし、モノの移動や整理が楽になります。「必要なモノがすぐに見つかる!」という、効率的な作業環境が実現するでしょう。
- 部門間対立: 「制約」という共通の課題に、全部門が協力して取り組むことで、部門間の連携が強化されます。例えば、営業はボトルネック工程の能力を考慮した納期設定を行い、製造は営業と情報を共有しながら生産計画を立てます。
- 現場目線の効果: 営業と製造の対立が減り、現場のリーダーは、部門間の調整に費やす時間を、本来の業務に充てることができるようになります。「営業vs製造」の板挟みから解放されるでしょう。
- 納期遅れ: 「制約」を徹底活用し、ボトルネック工程の能力を最大限に引き出すことで、生産リードタイムを短縮し、納期遅れを解消します。例えば、ボトルネック工程には熟練作業者を配置し、段取り替え時間を短縮するなどの対策を行います。
- 現場目線の効果: 納期に追われるプレッシャーから解放され、精神的な余裕が生まれます。残業時間の削減にもつながり、作業者のワークライフバランスが改善するでしょう。
- キャッシュフロー悪化: 在庫の適正化と品質トラブルの削減により、キャッシュフローが改善します。不要な在庫を減らし、不良品による損失を抑えることで、資金繰りが安定します。
- 現場目線の効果: 必要な資材や設備をタイムリーに調達できるようになり、生産活動がスムーズになります。改善活動への投資も可能になり、現場のモチベーション向上につながるでしょう。
TOC理論は万能薬?メリットとデメリット、適用範囲を考える
TOC理論は非常に強力な問題解決ツールですが、万能薬ではありません。
TOC理論のメリット
- シンプルで理解しやすい: 専門知識がなくても理解しやすい、シンプルな理論です。
- 迅速な効果: 制約に集中することで、短期間で効果を実感できます。
- 全体最適を実現: 部分最適ではなく、システム全体のパフォーマンスを向上させます。
- 継続的改善を促進: 制約は常に移動するため、継続的な改善活動につながります。
TOC理論のデメリット
- 制約の特定が難しい場合がある: 複雑なシステムでは、制約を正確に特定することが難しい場合があります。
- 現場の理解と協力が必要: TOC理論を導入するには、経営層だけでなく、現場の理解と協力が不可欠です。
- 適用範囲に限界がある: すべての問題に適用できるわけではなく、特に、外的要因(例:市場の急激な変化)には対応が難しい場合があります。
適用が効果的な場合
- 製造業: 生産ラインのボトルネック解消、リードタイム短縮、在庫削減などに効果的です。
- プロジェクト管理: プロジェクトのクリティカルパス(制約)を特定し、納期短縮を図ることができます。
- サプライチェーン管理: サプライチェーン全体のボトルネックを特定し、供給の効率化を図ることができます。
適用が難しい場合
- 制約が特定しにくい、あるいは頻繁に変わる場合: 例えば、非常に複雑なシステムや、外的要因の影響が大きいビジネスなど。
- 人間関係が主な問題の場合: TOC理論は、人間関係の改善には直接的な効果はありません。
現場へのメッセージ:TOC理論で、現場から会社を変えよう!
TOC理論は、現場のリーダーにとって、非常に心強い味方となります。なぜなら、TOC理論は、現場の「困った」を解決するための具体的な方法論 を提供してくれるからです。
「どうせ、上は現場のことなんてわかってくれない…」と諦める前に、ぜひTOC理論を学んでみてください。TOC理論を実践することで、皆さんの現場は、そして会社全体は、きっと大きく変わるはずです!
TOC理論は、現場から会社を変える、強力な武器なのです!
【事例】TOC理論でV字回復!中小製造業A社の奇跡
では本当にそんなことが可能なのか?TOC理論を導入し、劇的なV字回復を遂げた中小製造業A社の事例を紹介します。A社は、かつては多くの問題を抱え、倒産寸前の状態でした。しかし、TOC理論との出会いが、A社の運命を大きく変えたのです。
崩壊寸前だったA社:品質問題、在庫過剰、対立、資金難…問題のデパート
A社は、精密機器部品を製造する、従業員数約50名の中小企業です。数年前までは、安定した経営を続けていましたが、市場の変化への対応が遅れ、徐々に業績が悪化。TOC理論導入前は、以下のような問題を抱え、まさに「問題のデパート」状態でした。
- 品質問題: 主要取引先からのクレームが頻発。原因は特定できず、場当たり的な対策を繰り返すばかり。
- 在庫過剰: 売れない製品の在庫が倉庫に山積み。販売計画は、営業部門の希望的観測に基づくもので、市場の需要と大きく乖離していました。
- 部門間対立: 営業部門は「売れないのは製造の品質が悪いからだ」と主張し、製造部門は「営業が無茶な納期を設定するからだ」と反論。社内の雰囲気は最悪でした。
- 資金繰り悪化: 過剰在庫と品質問題による損失が重なり、資金繰りが急速に悪化。銀行からの追加融資も断られ、倒産の危機に瀕していました。
- 社員の士気低下: 将来への不安から、社員のモチベーションは低下。離職者も後を絶たず、現場は疲弊しきっていました。
TOC理論との出会い:ボトルネック「製造工程の能力不足」を特定
藁にもすがる思いで、A社の経営陣は、外部コンサルタントに支援を依頼。そこで紹介されたのが、TOC理論でした。
コンサルタントは、まずA社の製造工程を徹底的に分析しました。その結果、特定の加工工程(工程X)がボトルネック となっていることが判明しました。工程Xの処理能力が、全体の生産量を制限していたのです。
さらに、詳しく調査を進めると、工程Xの能力不足の原因は、設備の老朽化 と 作業員のスキル不足 であることが明らかになりました。
TOC理論で問題解決へ:現場と経営が一丸となった改善活動
A社は、TOC理論に基づき、以下の5つのステップで問題解決に取り組みました。
ステップ1:制約(ボトルネック)を特定する
- 前述の通り、工程Xがボトルネックであると特定されました。
ステップ2:制約を徹底活用する
- 工程Xの稼働率を最大限に引き上げるため、24時間稼働 に切り替えました。
- 工程Xに 最も熟練した作業員を配置 し、作業効率の向上を図りました。
- 工程Xの 段取り替え時間を短縮 するための改善活動を実施しました。
ステップ3:制約以外を制約に従属させる
- 工程Xの処理能力に合わせて、他の工程の生産量を調整 しました。
- 工程Xの前には、適正量の仕掛品バッファ を設けることで、工程Xが常に稼働できる状態を維持しました。
- 営業部門は、工程Xの能力を考慮した 現実的な納期設定 を行うようになりました。
ステップ4:制約の能力を高める
- 老朽化した設備を更新 し、処理能力を向上させました。
- 工程Xの作業員に対して 徹底的な技術指導 を行い、スキルアップを図りました。
- 工程Xの 作業手順を標準化 し、誰でも効率的に作業できるようにしました。
ステップ5:新たな制約を見つける
- 工程Xの能力向上に伴い、別の工程(工程Y)が新たなボトルネック となりました。
- A社は、再びTOC理論のステップ1に戻り、工程Yの改善に取り組み始めました。
並行して、以下の活動も実施しました。
- 営業と製造部門の連携強化: 営業と製造が定期的にミーティングを行い、情報共有を徹底しました。顧客の要望や市場動向を正確に把握し、現実的な生産計画を立案しました。
- 在庫の適正化: TOC理論に基づき、生産量を調整することで、過剰在庫を大幅に削減。倉庫スペースを有効活用できるようになり、資金繰りも改善しました。
- 品質の改善: ボトルネック工程の品質管理を徹底するとともに、全社的な品質改善活動を展開。クレーム件数は激減し、顧客からの信頼を回復しました。
- 資金調達の再構築: 外部の専門家と協力し、事業計画を見直し。銀行との交渉を重ね、新たな融資を取り付けることに成功しました。さらに、不要な資産を売却するなどして、財務体質の強化を図りました。
驚異の成果!スループット向上、品質改善、そして社員の笑顔
TOC理論導入後、A社は劇的な変化を遂げました。
- スループット(生産量)が30%向上: ボトルネック工程の改善により、全体の生産量が大幅に向上しました。
- リードタイムを50%短縮: 生産工程全体の流れがスムーズになり、顧客への納期を大幅に短縮することに成功しました。
- 品質トラブルが80%減少: 徹底した品質管理により、クレーム件数が激減しました。
- 在庫を40%削減: 過剰在庫を削減し、資金繰りが大幅に改善しました。
- 営業利益率が150%改善: コスト削減とスループット向上が利益増加に直結しました。
- 社員のモチベーション向上: 会社の業績回復と、職場環境の改善により、社員の士気が向上。離職率も低下しました。
- 部門間の協力体制が強化: TOC理論導入は部門間の壁をなくすきっかけとなりました。営業と製造が一体となって目標達成に取り組む風土が醸成されました。
TOC理論がもたらした真の価値:持続可能な成長への道筋
A社のV字回復は、TOC理論が単なる問題解決の手法ではなく、企業文化を変革する力 を持っていることを証明しています。
A社は、TOC理論を通して、以下の3つの重要な価値を手に入れました。
- 問題解決能力の向上: TOC理論の5つのステップを繰り返し実践することで、社員は自ら問題を発見し、解決する能力を身につけました。
- 全体最適の視点: 部分最適ではなく、常に全体最適を意識する企業文化が醸成されました。
- 持続可能な成長基盤: 目先の利益追求ではなく、継続的な改善を重視する企業体質へと変革を遂げました。
A社の事例は、TOC理論が中小製造業の未来を切り拓く、強力なツールであることを示しています。 A社のように、TOC理論で「奇跡」を起こす企業が、今後ますます増えていくことを期待しています。
今日から始める!TOC理論実践ガイド~5つのステップで現場が変わる
さきほどは、TOC理論を導入してV字回復を遂げたA社の事例を紹介しました。「ウチの会社も、あんな風に変われたら…」と思った方も多いのではないでしょうか?
そこで、皆さんの現場でTOC理論を実践するための具体的なステップ を簡単に解説します。特別な知識や経験は必要ありません。今日からすぐに始められる、実践的なガイドラインです!
ステップ1:最大の敵を見つけ出せ!制約(ボトルネック)特定の極意
TOC理論では、まず初めに 「制約(ボトルネック)」 を見つけることが最も重要です。制約とは、システムのパフォーマンスを制限している最も弱い部分 のことです。製造現場で言えば、全体の生産量を決めてしまう、最も処理能力の低い工程や機械、作業者が制約になります。
制約特定の具体的な方法
- 現場観察: まずは、製造ライン全体を注意深く観察しましょう。
- 仕掛品が滞留している工程: 特定の工程の前に、いつも仕掛品が山積みになっていませんか?そこがボトルネックの可能性があります。
- 常にフル稼働の工程: 他の工程が手待ち状態になっているのに、常にフル稼働している工程はありませんか?
- 作業者の動き: 特定の作業者だけが、いつも忙しそうに動き回っていませんか?
- データ収集: 各工程の生産量、サイクルタイム、稼働率などのデータを収集し、分析しましょう。
- 生産量が少ない工程: 1時間あたりの生産量が、他の工程と比べて著しく少ない工程は、ボトルネックの可能性があります。
- サイクルタイムが長い工程: 1つの製品を処理するのにかかる時間が長い工程も、ボトルネックの疑いがあります。
- 稼働率のバラツキ: 他の工程が安定して稼働しているのに、特定の工程だけ稼働率が低い、または高すぎる場合、ボトルネックが存在する可能性があります。
- ヒアリング: 現場の作業者に、直接話を聞いてみましょう。
- 「いつも忙しい工程はどこですか?」
- 「作業が滞りやすい工程はどこですか?」
- 「どの機械が、よくトラブルを起こしますか?」
現場リーダーへのアドバイス: 現場を歩き回り、自分の目で見て、現場の声に耳を傾けることが重要です。現場のリーダーである皆さんは、誰よりも現場を熟知しています。その経験と知識を活かし、ボトルネックを特定しましょう!
ステップ2:ボトルネックを最大限に活かす!制約徹底活用の秘訣
ボトルネックを特定したら、次は その能力を最大限に引き出す ことを考えます。ここでのポイントは、ボトルネック工程を絶対に止めないこと です。
制約徹底活用の具体策
- 優先順位設定: ボトルネック工程を最優先に稼働させ、他の工程はボトルネックのペースに合わせます。
- ボトルネック工程の作業に必要な資材、人員は、最優先で確保しましょう。
- ボトルネック工程の作業者は、他の作業を兼務させず、ボトルネック工程の作業に専念させましょう。
- 無駄の排除: ボトルネック工程の稼働を妨げる、あらゆる無駄を排除します。
- 段取り替え時間の短縮: 段取り替えの手順を見直し、可能な限り短縮化を図りましょう。
- チョコ停の削減: 設備のメンテナンスを徹底し、突発的な故障やトラブルを未然に防ぎましょう。
- 作業の標準化: 作業手順を標準化し、誰が作業しても、同じ品質、同じスピードで作業できるようにしましょう。
- 制約工程の保護: ボトルネック工程の前に、適正量の仕掛品バッファを設けます。
- バッファを設けることで、前工程のトラブルでボトルネック工程が停止するのを防ぎます。
- バッファの量は、多すぎても少なすぎてもいけません。過去のデータや経験を基に、適正量を設定しましょう。
現場リーダーへのアドバイス: ボトルネック工程の作業者と密にコミュニケーションを取り、ボトルネック工程を止めないための対策を一緒に考えましょう。現場の知恵を結集することが、制約徹底活用への近道です!
ステップ3:全体をコントロールせよ!制約に従属させる仕組みづくり
ボトルネック工程の能力を最大限に引き出したら、次は 他の工程をボトルネック工程に従属 させます。つまり、ボトルネック工程のペースに合わせて、全体の生産量をコントロールするのです。
制約に従属させる具体策
- ペース調整: ボトルネック工程の生産能力に合わせて、前後の工程の生産量を調整します。
- ボトルネック工程が1時間あたり10個生産できるなら、前後の工程も1時間あたり10個、もしくはそれ以下に生産量を調整します。
- ボトルネック工程より前に、必要以上に仕掛品を投入しないように注意しましょう。
- 同期: 各工程の作業開始・終了タイミングを調整し、ボトルネック工程に仕掛品がスムーズに流れるようにします。
- 各工程のサイクルタイムを調整し、ボトルネック工程に負担をかけないようにしましょう。
- 情報共有: ボトルネック工程の状況を、全ての工程で共有します。
- 生産管理ボードなどを活用し、ボトルネック工程の生産量、仕掛品バッファの量を「見える化」しましょう。
- ボトルネック工程でトラブルが発生した場合は、迅速に情報を共有し、関係する工程がすぐに対応できるようにしましょう。
DBR(ドラム・バッファ・ロープ)の活用
TOC理論では、「DBR(ドラム・バッファ・ロープ)」 という仕組みを使って、生産をコントロールします。
- ドラム: ボトルネック工程の生産ペース。太鼓を叩くように、このペースで生産します。
- バッファ: ボトルネック工程の前に設ける仕掛品在庫。ボトルネック工程を保護する役割を果たします。
- ロープ: ボトルネック工程の生産指示を、前工程に伝える仕組み。ロープで引っ張るように、ボトルネック工程のペースに合わせて、前工程の作業を同期させます。
現場リーダーへのアドバイス: まずは、ボトルネック工程の能力を正しく把握することが重要です。その上で、各工程の作業者と話し合い、ボトルネック工程に合わせた生産計画を立てましょう。DBRの仕組みは、最初は難しく感じるかもしれませんが、慣れれば現場の統制が取りやすくなる強力なツールです!
ステップ4:弱点を強みに変える!制約を改善する方法
ここまでのステップで、ボトルネック工程を徹底活用し、全体の流れを整えてきました。しかし、これだけでは、まだ十分とは言えません。最終的には、ボトルネックそのものの能力を高める 必要があります。
制約改善の具体策
- 設備改良: ボトルネック工程の設備を、より高性能なものに更新したり、増設したりすることで、生産能力を高めます。
- 老朽化した設備を、最新鋭の設備に置き換えることで、生産効率が大幅に向上する可能性があります。
- ボトルネック工程に、もう1台同じ設備を導入し、並列で作業することで、生産能力を倍増させることができます。
- 作業プロセス改善: ボトルネック工程の作業手順を見直し、無駄な動作を排除したり、作業を標準化したりすることで、作業効率を高めます。
- 作業動線を分析し、移動距離を短縮することで、サイクルタイムを短縮できるかもしれません。
- 作業手順書を整備し、誰でも同じ品質、同じスピードで作業できるようにすることで、生産性が安定します。
- リソース追加: ボトルネック工程に、人員やスキルを追加投入することで、生産能力を高めます。
- ボトルネック工程に、熟練作業者を増員することで、生産効率が向上する可能性があります。
- ボトルネック工程の作業者に、必要なスキルを習得させるための教育・訓練を実施することも有効です。
現場リーダーへのアドバイス: 制約改善には、投資が必要となる場合もあります。現場のリーダーとしては、ボトルネックを改善することで、どれだけの効果が見込めるのか、具体的な数値データを示して、上層部に提案することが重要です。現場の声を、経営判断につなげましょう!
ステップ5:終わりなき改善の旅へ!次の制約を見つけて、成長を加速
ステップ4でボトルネックを改善したら、それで終わりではありません。1つの制約が解消されると、必ず別の場所に新たな制約が現れます。 TOC理論では、このプロセスを繰り返し、継続的に改善を続けていくことが重要です。
継続的改善の具体策
- 継続的モニタリング: 各工程の生産量、サイクルタイム、稼働率などのデータを継続的に監視し、新たなボトルネックの兆候をいち早く察知します。
- 生産管理システムなどを活用し、データをリアルタイムで「見える化」することが重要です。
- 現場の作業者からの報告にも、注意深く耳を傾けましょう。
- 新たな制約発見: ステップ1に戻り、新たなボトルネックを特定します。
- 以前はボトルネックではなかった工程が、新たなボトルネックになっている可能性があります。
- 生産量が増加するにつれて、これまで顕在化していなかった問題が、ボトルネックとして現れることもあります。
- 改善サイクル維持: ステップ2~4を繰り返し、新たなボトルネックを解消していきます。
- TOC理論は、一度導入して終わりではなく、継続的に実践していくことが重要です。
- 改善活動を通じて、現場の作業者の問題解決能力も向上していきます。
現場リーダーへのアドバイス: TOC理論は、現場のリーダーが中心となって実践することで、最大の効果を発揮します。改善活動を継続的にリードし、現場のメンバーを巻き込みながら、成長し続ける現場を目指しましょう!
この5つのステップを実践することで、皆さんの現場は、今よりもっと強く、もっと効率的な、そしてもっと魅力的な職場へと変わるはずです。
TOC理論成功への7つの鍵~現場と経営が一体となるために
さきほどの「実践ガイド」では、TOC理論を現場で実践するための具体的なステップを解説しました。しかし、TOC理論を真に成功させるためには、現場の努力だけでなく、経営層の理解と協力 が不可欠です。ここでは、TOC理論を成功に導くための7つの重要なポイントを、現場と経営が一体となる視点から解説します。
1. ボトルネック特定の重要性:すべての改善の出発点
「宝探しは、まず地図から」
TOC理論の出発点は、ボトルネックの特定 です。ボトルネックを正確に見つけなければ、的外れな改善活動に時間と労力を浪費してしまいます。
- 現場: 現場のリーダーは、日々の業務の中で、どこに問題があるのかを最もよく知っています。現場の観察、データ分析、作業者からのヒアリングなどを通じて、ボトルネック特定に積極的に取り組みましょう。
- 経営: 経営層は、現場からの報告を鵜呑みにするのではなく、自らも現場に足を運び、現状を把握する ことが重要です。現場のリーダーと一緒になって、ボトルネック特定に取り組みましょう。
ボトルネック特定は、宝の地図を手に入れるようなものです。 正確な地図があれば、効率的に宝(=改善)を見つけることができます。
2. 制約を徹底活用する:部分最適から全体最適へ
「弱点を最大限に活かす」
ボトルネックを特定したら、その能力を最大限に引き出すことに注力します。ボトルネック以外の工程を改善しても、全体の生産量は増えません。
- 現場: ボトルネック工程の作業が最優先です。ボトルネック工程を絶対に止めない という意識を、チーム全員で共有しましょう。段取り替え時間の短縮、チョコ停削減など、ボトルネック工程の稼働率を高めるための改善活動に、積極的に取り組みましょう。
- 経営: ボトルネック工程の徹底活用は、「部分最適」から「全体最適」への転換 を意味します。各部門が、それぞれの目標ではなく、ボトルネック工程の能力を最大限に引き出すという共通の目標に向かって協力する体制を構築しましょう。
ボトルネックを徹底活用することは、弱点を強みに変える第一歩です。
3. 全体を制約に従属させる:組織の足並みを揃える
「オーケストラは、指揮者に合わせる」
ボトルネック工程の能力を最大限に引き出したら、他の工程をボトルネック工程のペースに合わせます。
- 現場: ボトルネック工程の生産ペースに合わせて、前後の工程の生産量を調整しましょう。DBR(ドラム・バッファ・ロープ) などのツールを活用し、生産の流れを同期させることが有効です。
- 経営: ボトルネック工程の能力に基づいて、現実的な生産計画 を立案しましょう。営業部門には、ボトルネック工程の能力を考慮した納期設定を徹底させることが重要です。
組織全体が、ボトルネック工程という「指揮者」に合わせて動くことで、無駄のない、効率的な生産体制が実現します。
4. 制約の能力向上:ボトルネック解消で全体のレベルアップ
「弱点を克服し、さらなる高みへ」
ボトルネックを徹底活用し、全体を従属させたら、次はボトルネックそのものの能力向上を図ります。
- 現場: ボトルネック工程の作業手順を見直し、無駄な動作を排除したり、作業を標準化したりすることで、作業効率を高めましょう。現場のリーダーは、改善提案を積極的に奨励し、実現に向けてサポート することが重要です。
- 経営: ボトルネック工程の能力向上には、設備投資や人員増強などの経営判断 が必要となる場合があります。現場からの提案を真摯に受け止め、必要な投資を迅速に実行しましょう。
ボトルネックの能力向上は、組織全体のレベルアップにつながります。
5. 継続的改善のサイクル:新たな制約に挑み続ける
「改善に終わりなし」
1つのボトルネックが解消されても、それで終わりではありません。必ず、別の場所に新たなボトルネックが現れます。
- 現場: 各工程の生産量、サイクルタイム、稼働率などのデータを継続的に監視し、新たなボトルネックの兆候をいち早く察知しましょう。現場のリーダーは、改善活動を習慣化させ、常に問題意識を持つ ように指導することが重要です。
- 経営: TOC理論の導入を、一過性のプロジェクトとして終わらせるのではなく、継続的な改善活動として定着させる ことが重要です。改善活動を積極的に支援し、成果を上げた社員を適切に評価しましょう。
改善活動に終わりはありません。常に新たな制約に挑戦し続けることが、企業の持続的な成長につながります。
6. チームの連携と文化:現場と経営が一体となる風土づくり
「ONE TEAMで、課題に立ち向かう」
TOC理論を成功させるためには、現場と経営層が一体となり、ONE TEAM で問題解決に取り組む必要があります。
- 現場: 現場のリーダーは、部門間の壁を越えたコミュニケーション を促進し、チームワークを高めましょう。問題が発生した時は、関係者全員で知恵を出し合い、解決策を導き出すことが重要です。
- 経営: 経営層は、現場の声を積極的に吸い上げ、経営判断に反映させる ことが重要です。現場との定期的なミーティングを開催したり、提案制度を設けたりするなど、現場と経営層のコミュニケーションを活性化させましょう。
現場と経営が一体となることで、組織全体の力が最大限に発揮されます。
7. 成果の測定と報告:改善効果を見える化し、モチベーションを高める
「努力を見える化し、成長を実感する」
改善活動の成果を、具体的な数値データで測定し、現場と経営層で共有する ことが重要です。
- 現場: 生産量、リードタイム、不良率などのデータを収集し、改善活動の成果を「見える化」しましょう。現場のリーダーは、改善効果をわかりやすく説明し、チームのモチベーションを高める ことが重要です。
- 経営: 改善活動の成果を、経営指標(例:売上、利益、キャッシュフローなど)に結びつけて評価 しましょう。現場の努力が、経営にどのように貢献しているかを明確に示すことで、社員のモチベーション向上につながります。
成果を「見える化」することで、改善活動の意義が明確になり、現場と経営層のモチベーションを高めることができます。
まとめ:TOC理論で中小製造業を改善する事例研究
ここまで、TOC理論の基本原則、実践ガイド、そして成功への鍵について解説してきました。皆さんの心の中には、今、「自分の現場でも、TOC理論を実践してみたい!」 という熱い想いが、ふつふつと湧き上がっているのかもしれません。
しかし、現実的には、
「本当にうまくいくのだろうか…」 「何から始めればいいのかわからない…」 「現場のメンバーを巻き込めるだろうか…」
といった不安も、少なからず感じているかもしれません。
でも、心配はいりません!
TOC理論は、決して難しい理論ではありません。これまでお伝えしてきたように、「制約」 に注目し、「全体最適」 の視点を持って、「継続的な改善」 を続けていけば、必ず成果は現れます。
大切なのは、まず一歩を踏み出すことです。
- 今日、現場に戻ったら、「ウチの職場のボトルネックはどこだろう?」 という視点で、現場を観察してみてください。
- いつも仕掛品が溜まっている工程はありませんか?
- いつも忙しそうにしている作業者はいませんか?
- いつもトラブルが発生している設備はありませんか?
まずは、現場の「現実」を直視することから、全てが始まります。
そして、現場のメンバーと、「どうすれば、もっと仕事がやりやすくなるだろう?」 と、とことん話し合ってみてください。現場のリーダーである皆さんが、中心となって、「改善」の旗振り役 を担うのです。
「ウチの職場には、無理だ…」と、最初から諦めないでください。
小さな改善の積み重ねが、やがて大きな成果を生み出します。A社の事例でも見たように、TOC理論は、「現場の力」 を最大限に引き出し、「奇跡」 を起こす可能性を秘めています。
TOC理論は、皆さんを、そして皆さんの会社を、より良い未来へと導く、強力な羅針盤となるはずです。
さあ、今すぐ、TOC理論を実践しましょう!
皆さんの現場に、そして、日本の中小製造業に、大きな変革の波が押し寄せることを、心から願っています!