さて、製造現場で働く誰しもが、毎日、品質の高い製品をリーズナブルに納期通り、お客様に届けるために、色々な工夫をこらしているかと思います。でも「もっと早く作れ」「もっと安く作れ」って言われる一方で、「不良は絶対出すなよ」なんて、まるで綱渡りみたいな難題に挑戦して悩んでいる方もいるかもしれませんね。
「品質を上げようとしたら、どうしてもコストがかかるよな…」「納期を守るためには、ちょっとくらい不良が出ても仕方ないか…」そんな風に、品質(Quality)、コスト(Cost)、納期(Delivery)って、どうしてもどれか一つを良くしようとすると、別の何かが犠牲になる、そんな風に感じている方も多いかと思います。 まさに、QCDはトレードオフの関係にある、そんな常識が私たちの現場には根付いているかもしれません。
でも、ちょっと待ってください。すべてのパターンで本当にそうなるのでしょうか?
もし、不良品や手直しがなくなったらどうでしょう? 無駄な作業や検査の時間が丸ごと浮いて、もっとスムーズに製品が流れるようになるんじゃないでしょうか? それって、結果的にコストを下げることにつながるかと思います。 しかも、お客様からのクレームが減って、信頼が増せば、新しい仕事にも繋がりやすくなるはずです。
実は、品質を向上させることこそが、コストダウンの最強のエンジンになる、という考え方があります。そこで今回は、そんな「え?なんでQCDはトレードオフなのに、品質改善が原価低減につながることになるんだ?」という疑問に、現場の皆さんが「なるほど!」と納得できるような言葉で、その秘密をじっくりと解説していきたいと思います。
ぜひ今回も読み終えるまでのお時間、しばらくお付き合いくださいませ。
なぜ「品質改善=コスト増」は誤解なのか? – QCDの伝統的トレードオフ観を再考する
ではなぜ、QCDはトレードオフの関係=あちらを立てればこちらが立たずの関係なのに、品質改善が原価低減に結びつくのでしょうか?まずはQCDの基本要素から整理していきましょう。
QCDとは?品質・コスト・納期の基本要素を理解する
まず、私たちが普段から意識している「QCD」について、改めて確認しておきましょう。QCDとは、製造業の現場で、良い製品を作るための3つの重要な要素の頭文字を取った言葉です。
- Qは「品質(Quality)」のこと。これは単に壊れないとか、見た目がきれいということだけではありません。お客様が求めている機能を満たしているか、安心して長く使えるか、そういった製品そのものの価値のことです。
- Cは「コスト(Cost)」、つまり「原価」のことですね。材料費、人件費、設備費など、製品を作るためにかかる全てのお金のことを指します。もちろん、できるだけこのコストは抑えたいというのが、私たちの共通の思いでしょう。
- Dは「納期(Delivery)」のこと。お客様との約束の期日までに、きちんと製品を届けることです。納期を守ることは、お客様の信頼を得る上で非常に大切です。
このQCDは、良い製品を作る上で、どれも欠かすことのできない要素です。私たちは毎日、この3つのバランスを取りながら、より良い製品づくりを目指しているわけです。
トレードオフ認識の落とし穴 – 短期的な視点と全体最適の欠如
そして、多くの現場で言われているのが、「品質を上げようとすると、どうしても手間がかかってコストが上がってしまう」「納期を守るために、どうしても品質チェックの時間を削らざるを得ない」といった、いわゆる「トレードオフ」の関係です。一つの要素を良くしようとすると、別の要素が悪くなってしまう、そんな風に私たちは考えがちです。
例えば、「もっと丁寧に検査をしよう」となると、どうしても検査に時間がかかって、納期が遅れるんじゃないかと思ってしまいますよね。あるいは、「もっと良い材料を使おう」となると、材料費が上がって、コストが増えてしまうと感じるのも 当たり前のことです。
でも、ちょっと立ち止まって考えてみてください。この「トレードオフ」という考え方、もしかしたら目の前のことだけを見ている、短期的な視点に囚われているのかもしれません。
例えば、不良品を出荷してしまった場合を想像してみてください。お客様からのクレーム対応、返品、場合によっては作り直し…これって、実はものすごい時間と手間、つまりコストがかかっているはずです。検査の時間を少し増やしてでも不良品を防ぐことができれば、結果的にはトータルでのコストを抑えられるのではないでしょうか?
つまり、品質、コスト、納期は、それぞれがバラバラに動いているわけではなく、お互いに深く影響し合っているんです。短期的な視点だけで「品質を上げるとコストが上がる」と決めつけてしまうと、もっと大きな視点で見れば、実は損をしている可能性を見逃してしまうかもしれません。
トレードオフなのに品質改善がコスト削減に繋がる可能性
では、なぜ一般的にトレードオフの関係にあると考えられている品質とコストが、品質改善によって同時に良くなる可能性があるのでしょうか?
その秘密を解き明かすカギは、「不良」や「無駄」といった、私たちの現場に潜む様々なロスにあります。品質が悪いということは、不良品が発生したり、手直しが必要になったり、お客様に迷惑をかけてしまったりと、様々な形で無駄を生み出しています。
もし、この不良や無駄を徹底的に減らすことができたらどうでしょうか? 手直しにかかる時間、不良品として廃棄する材料、お客様対応にかかる手間…これらが全て削減できるとしたら、品質が向上するだけでなく、大幅なコストダウンにも繋がるはずです。
つまり改善活動とは、トレードオフのQCDの関係を抜本的に変えるパワーを持っていると言えます。そりゃ、進め方や過程を変えてしまうのですから、トレードオフとなる構造も変わりますよね。
品質改善が原価低減の「最強エンジン」となるメカニズム
さて、ここからは、品質改善がなぜ「コストを下げる最強のエンジン」になり得るのか?生み出す3つのメリットとその具体的な仕組みを見ていきましょう。まるで、今まで見過ごしてきた場所に、実は大きなコストダウンの宝が眠っているようなイメージです。
メリット1:失敗コストの劇的な削減 – 不良・手直し・保証対応の撲滅
品質が悪いと、どうしても発生してしまうのが「失敗コスト」です。これは、製品がお客様の要求を満たせなかったために発生する、いわば「ムダ金」のこと。そして、この失敗コストを減らすことこそが、品質改善がコストダウンに直結する一番分かりやすい理由なんです。
内部失敗コストの削減:廃棄、手直し、再検査などの低減
工場の中で不良品が出ると、どうなりますか? せっかく作った製品を泣く泣く廃棄したり(廃棄)、基準を満たすように手直ししたり(手直し)、もう一度ちゃんとできているか確認したり(再検査)と、余計な時間と手間がかかってしまいますよね。これらの「廃棄」「手直し」「再検査」にかかるコストが、内部失敗コストです。品質が向上すれば、これらの無駄な作業が減り、その分、本来の生産活動に集中できるわけです。
外部失敗コストの削減:クレーム、返品、リコール、そして信頼失墜の防止
さらに、不良品がお客様の手に渡ってしまうと、もっと大変なことになります。お客様からのクレーム対応に追われたり(クレーム)、製品を返品されたり(返品)、最悪の場合には、製品を回収するリコールなんてことにもなりかねません(リコール)。これらの対応には、直接的な費用だけでなく、お客様の信頼を失ってしまうという、計り知れない損失も伴います。品質改善によって不良品をなくすことができれば、これらの大きな外部失敗コストを未然に防ぐことができるのです。お客様からの信頼は、お金では買えない、本当に大切な財産ですから。
メリット2:効率性と生産性の向上 – 無駄を排除し、スムーズな業務フローを実現
品質改善は、単に不良品を減らすだけでなく、私たちの仕事のやり方そのものをスムーズに変えてくれます。まるで、油を差した機械のように、動きが滑らかになるイメージです。
評価コストの最適化:検査から予防へシフト
不良品を見つけるための検査(評価)は、もちろん大切です。でも、もし不良品がほとんど出ないような仕組みを作ることができたら、どうでしょうか? 毎回、厳しい検査をする必要がなくなり、その分の時間や人員を他の業務に回せるようになりますよね。品質改善が進むと、不良を「見つける」ためのコストから、不良を「作らない」ための仕組みづくり(予防)に重点を置けるようになるのです。
リードタイムの短縮とボトルネックの解消
不良品や手直しが多いと、どうしても作業が滞って、製品が完成するまでの時間(リードタイム)が長くなってしまいます。また、特定の工程で不良が集中すると、そこがボトルネックとなって、全体の流れを悪くしてしまいます。品質改善によって不良が減れば、これらの停滞やボトルネックが解消され、製品がより早くお客様に届けられるようになるのです。
資源の有効活用と歩留まりの向上
品質が悪ければ、材料を無駄にしてしまったり、せっかくかけた労力が水の泡になってしまったりすることがあります。しかし、品質が安定すれば、投入した材料を最大限に活かすことができ(歩留まりの向上)、無駄な資源の消費を抑えることができます。これは、コスト削減に直接つながるだけでなく、環境への負荷を減らすことにも貢献します。
メリット3:顧客ロイヤルティと市場競争力の強化 – 長期的な視点でのコストメリット
品質改善がもたらすメリットは、工場の内部にとどまりません。お客様からの信頼を得て、会社の外にも大きな影響を与えるのです。
リピート率向上と顧客獲得コストの削減
品質の良い製品をお届けできれば、お客様はきっと満足して、また私たちの製品を選んでくれるようになります(リピート率の向上)。そして、満足したお客様の良い評判は、新しいお客様を連れてきてくれます。これは、広告や営業にかかるコストを抑えながら、安定した受注に繋がる、非常に大きなメリットです。
ブランドイメージ向上と価格競争力の強化
高品質な製品を作り続けることで、私たちの会社のブランドイメージは向上します。「あの会社の製品は品質が良いから安心だ」という評判は、他社との競争において大きな武器になります。多少価格が高くても、「品質が良いなら」と選んでくれるお客様が増える可能性もあります。つまり、品質改善は、価格競争に巻き込まれることなく、高い収益性を維持することにも繋がるのです。
このように見ていくと、品質改善は、単に不良品を減らすだけでなく、工場の内部の効率化、お客様からの信頼獲得、そして会社のブランド価値向上といった、様々な側面からコスト削減に貢献する「最強のエンジン」であることが理解できると思います。では、次はこの品質改善の考え方をさらに深めるための「品質コスト」という重要な概念について解説していきます。
知っておくべき「品質コスト」の概念 – 投資対効果を最大化する考え方
さて、品質改善がコストダウンの強力なエンジンになる理由を見てきましたが、ここで、その考え方をさらに深めるための重要なキーワード「品質コスト」についてお話しましょう。
品質コストとは? – 目に見えないコストを可視化する
「品質コスト」と聞くと、「品質を維持するためのお金のことかな?」と思われるかもしれません。確かにそれも一部ですが、実はもっと広い意味を持っています。品質コストとは、良い製品を作るためにかかる全てのお金と、品質が悪かったために発生してしまった全てのお金を合わせたものなんです。
例えば、新しい検査機器を導入したり、従業員に品質に関する研修を受けさせたりする費用は、良い製品を作るために「かけた」お金ですよね。一方で、不良品を廃棄したり、お客様からのクレームに対応したりする費用は、品質が悪かったために「発生してしまった」お金です。
普段、私たちは材料費や人件費といった目に見えるコストは意識しやすいですが、不良品やクレーム対応にかかるコストは、一つひとつは小さいように見えても、積み重なると意外と大きな金額になっていることがあります。品質コストという考え方を理解することで、今まで見過ごしてきた「もったいないお金」を可視化できるようになるのです。
PAFモデル:予防コスト、評価コスト、失敗コストの内訳
品質コストは、一般的に「PAFモデル」という考え方で3つに分類されます。この分類を知っておくと、どこに無駄が多いのか、どこに力を入れるべきなのかが見えてきます。
予防コストへの戦略的投資 – 問題発生を未然に防ぐ
「予防コスト」とは、不良品や問題が起こらないように、事前に投資するお金のことです。例えば、
- 作業手順書をしっかり作る
- 従業員に正しい作業方法を教える研修を行う
- 設備のメンテナンスを定期的に行う
- 新しい製品を設計する段階で、品質の問題が起きにくいように工夫する
などがこれにあたります。一見すると、これらの活動にはお金がかかるように見えますが、実は、後で発生する大きな失敗コストを防ぐための、賢い投資だと言えますよね。
評価コストの最適化 – 無駄な検査を見直す
「評価コスト」とは、製品の品質が良いかどうかをチェックするためにかかるお金です。例えば、
- 完成した製品を検査する
- 製造工程の途中で品質を確認する
- 検査に使われる測定器を校正する
などがあります。もちろん、品質を確保するために検査は必要ですが、もし工程の品質が安定して、不良品がほとんど出ないのであれば、過剰な検査は無駄なコストになってしまいます。品質改善が進めば、この評価コストを最適化できる可能性があります。
失敗コストの削減こそ最大の効果 – COPQ(質の悪いコスト)を最小化
そして最も重要なのが「失敗コスト」です。これは、製品がお客様の要求を満たせなかったために発生するコストで、さらに「内部失敗コスト」と「外部失敗コスト」に分けられます。
- 内部失敗コスト:工場内で見つかった不良品(廃棄、手直し、再検査など)にかかるコスト
- 外部失敗コスト:お客様の手に渡ってから発覚した不良(クレーム対応、返品、リコール、信頼失墜など)にかかるコスト
この失敗コストこそが、品質コストの中で最も大きく、そして削減する効果も大きい部分です。「COPQ(Cost of Poor Quality)」、つまり「質の悪いことによるコスト」とも呼ばれます。不良品一つひとつを見ると小さな損失かもしれませんが、積み重なると会社の利益を大きく圧迫する可能性があります。品質改善活動は、このCOPQを最小化することを最大の目標と考えるべきです。
品質コスト分析による改善ポイントの特定と意思決定
品質コストという考え方を理解し、それぞれのコストを把握することで、私たちは「どこに問題があるのか」「どこを改善すれば最も効果的なのか」をデータに基づいて判断できるようになります。
例えば、もし失敗コストが非常に高いのであれば、「不良を減らすための対策(予防コストへの 投資)」を優先的に行うべきだという判断ができます。逆に、評価コストが高すぎるのであれば、「工程の安定化を進めて、検査の頻度を見直す」という対策が考えられます。
このように、品質コストの分析は、無駄をなくし、 投資の効率を最大化するための、非常に強力な武器になるのです。では、次に具体的にどのように品質改善を進めていくのか、そのためのフレームワークをご紹介します。
実践!品質主導のコスト削減を実現するフレームワーク
ここからは、実際に品質改善を進めて、コストダウンを実現するための具体的な「枠組み(フレームワーク)」についてお話していきます。「なんだか難しそうだな…」と思うかもしれませんが、基本的な考え方は、私たちの現場でも取り入れられるものばかりです。
TQM(総合的品質管理) – 全員参加で「質」を高め、無駄をなくす
「TQM(Total Quality Management)」は、日本語では「総合的品質管理」と言われます。ちょっと難しそうな名前ですが、簡単に言うと「会社全体の全員が、製品やサービスの質を高めるために、それぞれの持ち場で力を合わせる」という考え方です。
TQMの基本原則と導入ステップ
TQMにはいくつかの大切な考え方があります。
- お客様第一主義(消費者指向): 何よりもまず、お客様が何を求めているかを理解し、それを満たすことを目指します。
- 全員参加: 社長から現場の作業者まで、全ての人が品質向上に責任を持ち、積極的に関わります。
- プロセスコントロール: 製品を作る工程(プロセス)そのものを良くしていくことが、良い品質を生み出すと考えます。
- 継続的改善: 一度良くなったら終わりではなく、常に「もっと良くするにはどうすればいいか」を考え、改善を続けていきます。
- 事実に基づく管理: 思いつきや勘ではなく、データに基づいて問題を見つけ、対策を考えます。
導入のステップとしては、まずは経営層が「品質を良くしていくぞ!」という強い姿勢を示すことが大切です。そして、目標を具体的に定め、従業員一人ひとりが品質について考え、行動できるような教育や仕組みを作っていきます。小さなことからでも良いので、できることから始めて、徐々に会社全体に広げていくイメージです。

品質文化の醸成と継続的改善(カイゼン)
TQMを成功させるためには、「品質は当たり前のもの」という文化を会社全体に根付かせることが重要です。そのためには、日々の業務の中で、ちょっとした改善のアイデアを出しやすい雰囲気を作ったり、良い改善をした人を褒めたりすることが大切です。
「継続的改善(カイゼン)」という言葉を聞いたことがある方もいるかもしれません。これは、大きな改革だけでなく、日々の小さな工夫や改善を積み重ねていくことで、少しずつでも確実に品質を向上させていく考え方です。現場の皆さんの「こうすればもっと良くなるのに」という気づきこそが、大きな改善の第一歩になるのです。
リーン生産方式 – 無駄の徹底排除が品質とコストを同時に改善
「リーン生産方式」は、トヨタ自動車が作り上げた生産方式で、「無駄を徹底的になくすことで、品質を高めながらコストも下げる」という考え方です。私たちの現場でも、この考え方を取り入れることで、大きな効果が期待できます。

リーンの基本原則と「7つの無駄」
リーン生産方式には、以下のようないくつかの基本的な考え方があります。
- 価値の明確化: お客様にとって何が価値なのかを明確にすることから始めます。
- 価値の流れの特定: 製品がお客様に届くまでの全ての工程(流れ)を見える化します。
- 流れの創出: その流れの中で、無駄をなくし、スムーズに製品が流れるように改善します。
- 引っ張り(プル)方式: お客様の注文に応じて必要なものだけを作るようにします(作りすぎの無駄をなくす)。
- 完璧性の追求: 無駄をなくす改善活動を終わりなく続けていきます。
そして、リーン生産方式では、徹底的に排除すべき「7つの無駄」というものがあります。
- 作りすぎの無駄: 売れる見込みのないものまで作ってしまう無駄
- 手待ちの無駄: 作業者が材料や指示を待っている時間などの無駄
- 運搬の無駄: 製品や部品を移動させるだけの無駄な作業
- 加工そのものの無駄: 付加価値を生まない余計な加工
- 在庫の無駄: 必要以上の部品や製品を持つことによる保管スペースや管理の無駄
- 動作の無駄: 作業者の不必要な動き
- 不良を作る無駄: 手直しや廃棄につながる不良品の発生
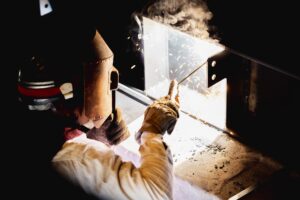
これらの無駄を一つひとつなくしていくことが、品質向上とコスト削減に繋がるのです。
ジャストインタイム(JIT)と自働化による品質向上
リーン生産方式の代表的な手法に「ジャストインタイム(JIT)」と「自働化」があります。
- ジャストインタイム(JIT): 必要なものを、必要な時に、必要な量だけ作るという考え方です。これにより、在庫の無駄を減らすだけでなく、不良在庫のリスクも減らすことができます。もし不良品が後工程で発見されれば、すぐに原因を突き止めて対策を講じることができるため、品質向上にも繋がります。
- 自働化: これは、単なる自動化とは違い、「異常が発生したら機械が自動的に停止する」仕組みを取り入れることです。これにより、不良品が大量に作られてしまうのを防ぎ、問題が起きたときにすぐに気づけるようになります。また、作業者が機械の異常に気づいてラインを止めることも「自働化」の重要な要素です。
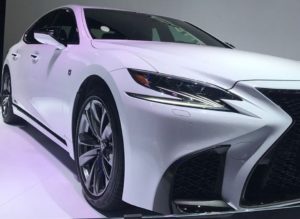
シックスシグマ、VAVEなど – その他の有効なアプローチ
TQMやリーン生産方式以外にも、品質改善とコスト削減に役立つ様々な手法があります。
- シックスシグマ: 統計的な手法を用いて、製品やプロセスのばらつきを極限まで減らし、不良品の発生をほぼゼロに近づけることを目指す取り組みです。
- VAVE(Value Analysis / Value Engineering): 製品の機能とコストを分析し、必要な機能を維持しながらコストを最小限に抑えるための手法です。
これらの手法は、少し専門的な知識が必要になる場合もありますが、基本的な考え方は、無駄をなくし、効率を高めるという点で、TQMやリーン生産方式と共通しています。
これらのフレームワークや手法は、すぐに全てを取り入れるのは難しいかもしれませんが、それぞれの考え方を理解し、私たちの現場でできることから少しずつ試していくことが、品質向上とコスト削減への第一歩となるはずです。次のセクションでは、実際にこれらの考え方を取り入れて、大きな成果を上げた企業の事例を見ていきましょう。
成功事例に学ぶ!品質改善が原価低減に繋がった実例
さて、ここまで品質改善がコストダウンに繋がる仕組みや、そのための考え方を見てきましたが、「本当にそんなうまくいくのか?」と思っている方もいるかもしれません。そこでこのセクションでは、実際に品質改善に取り組み、大きな成果を上げた企業の事例をご紹介します。これらの事例から、私たちの現場でもヒントになるような学びがあるはずです。
自動車部品メーカー:プロセス改善による不良率低下とコスト削減
ある自動車部品メーカーでは、プレス加工でどうしても小さな傷がついてしまうという問題が長年続いていました。傷がついた部品は、手作業で修正するか、最悪の場合は廃棄するしかありません。これは、時間と材料の無駄であり、コスト増の原因となっていました。
そこで、現場のリーダーを中心に、徹底的に原因を調査しました。すると、プレス金型の微妙な摩耗が傷の原因になっていることが分かりました。そこで、より耐久性の高い材質の金型に変更し、定期的なメンテナンスを徹底することにしたのです。
改善の効果: 新しい金型とメンテナンスの導入には初期投資が必要でしたが、傷の発生率が劇的に低下。手直しや廃棄の数が減り、結果的に材料費と人件費を大幅に削減することができました。また、不良品が減ったことで、納期遅延も解消され、お客様からの信頼も向上しました。
金属加工メーカー:治具導入と工程集約による品質・コスト・納期改善
ある金属加工メーカーでは、様々な金属部品の溶接や切断作業を行っていました。しかし、作業者の熟練度に左右される部分が多く、品質のばらつきや作業時間のムラが課題でした。また、複数の工程を経ることで、部品の移動や管理にも手間がかかっていました。
そこで、この会社では、各工程に合わせた専用の「治具(じぐ)」を設計・導入しました。治具を使うことで、誰が作業しても一定の品質で加工ができるようになり、作業時間も短縮されました。さらに、複数の工程を一つにまとめる「工程集約」も行い、部品の移動回数を減らし、リードタイムの短縮にも成功しました。
改善の効果: 治具の導入と工程集約により、品質の安定化と作業時間の短縮が同時に実現。不良品の発生も減少し、手直しにかかるコストも大幅に削減されました。また、納期も短縮されたことで、お客様からの評価も高まり、新たな受注にも繋がっています。
電子部品メーカー:自動化とAI活用による検査効率向上と品質安定化
ある電子部品メーカーでは、製品の最終検査を人の目で行っていました。しかし、部品が非常に小さく、検査員の集中力や経験によって検査の精度にばらつきが出るという課題がありました。また、検査にかかる時間も長く、生産性の向上を妨げていました。
そこで、この会社は、AI(人工知能)を活用した自動検査システムを導入しました。カメラで撮影した部品の画像をAIが解析し、瞬時に不良品を検出する仕組みです。
改善の効果: 自動検査システムの導入により、検査時間が大幅に短縮され、生産性が向上しました。また、AIによる客観的な判断により、検査の精度も向上し、見逃されていた微細な不良も発見できるようになりました。これにより、品質が安定し、お客様からのクレームも減少しました。
トヨタ自動車:TQM/リーン生産方式による世界的な競争力確立
言わずと知れたトヨタ自動車は、「TQM(総合的品質管理)」と「リーン生産方式」を長年にわたり徹底的に実践してきた企業です。製造プロセスのあらゆる無駄を排除し、従業員一人ひとりが品質改善に積極的に関わる文化を築き上げてきました。
改善の効果: その結果、高品質でありながら低コスト、そして短い納期での製品供給を実現し、世界的な自動車メーカーとしての地位を確立しました。在庫の削減、生産性の向上、不良率の低さなど、その効果は多岐にわたります。
その他の業界における品質改善とコスト削減の成功事例
製造業以外でも、品質改善はコスト削減に大きく貢献しています。例えば、
- サービス業: 業務プロセスの標準化やITツールの導入によるミス削減、顧客満足度向上によるリピート率増加
- 食品加工業: 衛生管理の徹底による異物混入防止、歩留まり向上による原材料費削減
- 建設業: 事前の綿密な計画と品質管理による手戻り防止、工期短縮による人件費削減
など、様々な業界で、品質を重視した取り組みが、結果的にコスト削減に繋がっている事例は枚挙にいとまがありません。
これらの事例からわかるように、業種や規模に関わらず、品質改善は必ずコスト削減に繋がる可能性があります。大切なのは、自社の現場の課題をしっかりと見つめ、紹介した考え方や手法を参考に、できることから一歩ずつ取り組んでいくことです。
はい、承知いたしました。最後のまとめとして、中小製造業の現場リーダー、あるいはリーダー候補の皆さんが、QCDのトレードオフの常識を打ち破り、品質改善に今すぐ取り組みたくなるような、力強いメッセージを込めたドラフトを作成します。
まとめ:品質改善はコスト削減のための戦略的投資である
さて、いかがだったでしょうか?ぜひ改めて考えてみていただきたいと思います。我々は日々の現場で、不良品や手直しにどれだけの時間と労力を費やしているでしょうか? お客様からのクレーム対応に、どれだけの神経を使っているでしょうか? それらは全て、目に見えないコストとして、私たちの会社の利益をじわじわと蝕んでいるのです。
「品質を上げればコストも上がる」—もしあなたがそう思っているのであれば、それは過去の常識です。今回でお伝えしてきたように、品質改善という改善はそのトレードオフの構造さえ見直すため、決してコスト増の要因とはなりません。むしろ、不良という名の最大の無駄を排除し、業務の流れをスムーズにし、お客様からの信頼という未来への財産を築き上げるための、「最強のコスト削減エンジン」となります。
もう、そろそろ改善という最強の武器を全員で手に取ることを選択しましょう。品質という土台をしっかりと固めることこそが、結果としてコストを下げ、納期を守り、ひいては会社の競争力を高める、最も賢い戦略的投資となります。
そりゃ、すぐに大きな変化を起こすのは難しいです。しかし、今日からできることは必ずあります。例えば、朝のミーティングで品質に関する小さな問題提起をしてみる。不良が発生した原因を、表面的な現象だけでなく、もっと深く掘り下げて考えてみる。そして、「もっとこうすれば良くなるはずだ」という現場のアイデアを、積極的に提案してみる。
小さな一歩が、やがて大きな変化を生み出します。品質改善は、一部の専門家だけの仕事ではありません。現場で働く皆さん一人ひとりの意識と行動が、その成否を握っています。
さあ、私たち自身の手で、長年の「QCDはトレードオフ」という常識を打ち破って、品質改善という名のエンジンに点火し、無駄のない、効率的で、そして何よりもお客様に喜んでいただける製品づくりを、共に目指しましょう。
その先に待っているのは、きっと今よりもずっと強く、そして豊かな会社の姿です。今こそ、行動を起こしましょう。